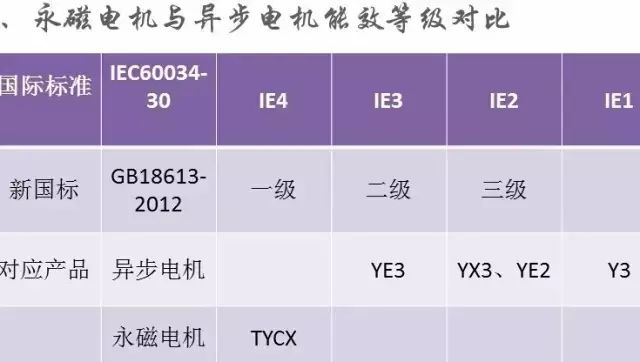
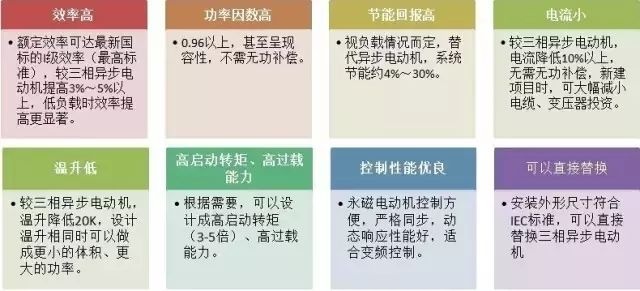
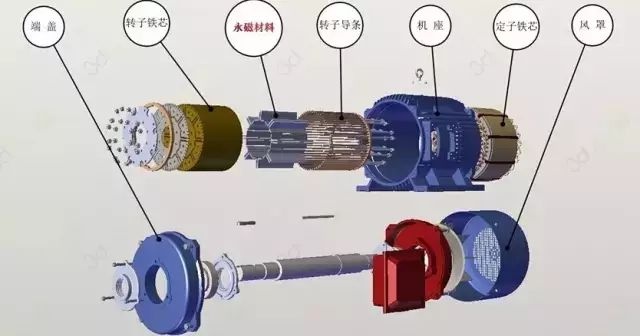
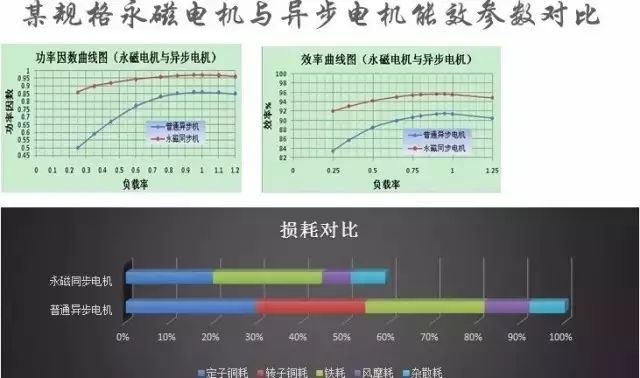
The development history of permanent magnet motor
The development of permanent magnet motors is closely related to the development of permanent magnet materials. my country is the first country in the world to discover the magnetic properties of permanent magnet materials and apply it to practice. More than 2,000 years ago, my country used the magnetic properties of permanent magnet materials to make a compass, which played a huge role in navigation, military and other fields. It became one of the four great inventions in ancient my country.
The world's first motor that appeared in the 1920s was a permanent magnet motor that generated an excitation magnetic field from a permanent magnet. But the permanent magnet material used at that time was natural magnetite (Fe3O4), the magnetic energy density was very low, and the motor made of it was bulky, and was soon replaced by electric excitation motor.
With the needs of the rapid development of various motors and the invention of current magnetizers, people have conducted in-depth research on the mechanism, composition and manufacturing technology of permanent magnet materials, and have successively discovered carbon steel and tungsten steel (the maximum magnetic energy product is about 2.7 kJ/m3 ), cobalt steel (maximum energy product about 7.2 kJ/m3) and other permanent magnet materials. Especially the AlNiCo permanent magnets that appeared in the 1930s (the maximum energy product can reach 85 kJ/m3) and the ferrite permanent magnets that appeared in the 1950s (the maximum energy product can now reach 40 kJ/m3), the magnetic properties are excellent. It has been greatly improved, and various micro and small motors have used permanent magnet excitation. The power of permanent magnet motors is as small as a few milliwatts and as large as tens of kilowatts. It is widely used in military, industrial and agricultural production and daily life, and its output has increased sharply.
Correspondingly, during this period, breakthroughs have been made in the design theory, calculation method, magnetization and manufacturing technology of permanent magnet motors, and a set of analysis and research methods represented by the diagrammatic method of permanent magnet working diagrams have been formed. However, the coercive force of AlNiCo permanent magnets is low (36-160 kA/m), and the remanence density of ferrite permanent magnets is not high (0.2-0.44 T), which limits their application range in motors. Until the 1960s and 1980s, rare earth cobalt permanent magnets and neodymium iron boron permanent magnets (both collectively referred to as rare earth permanent magnets) came out one after another. Their high remanence density, high coercive force, high magnetic energy product and linear demagnetization curve The excellent magnetic properties of the permanent magnet motor are especially suitable for the manufacture of motors, so that the development of permanent magnet motors has entered a new historical period.
Characteristics and application of permanent magnet motor
Compared with traditional electric excitation motors, permanent magnet motors, especially rare earth permanent magnet motors, have significant advantages such as simple structure, reliable operation, small size, light weight, low loss, high efficiency, and flexibility in the shape and size of the motor. . Therefore, the application range is extremely wide, covering almost every field of aerospace, national defense, industrial and agricultural production and daily life. The main characteristics and main application occasions of several typical permanent magnet motors are introduced below.
1. Rare-earth permanent magnet generator Compared with traditional generators, permanent magnet synchronous generators do not need collector rings and brush devices. The structure is simple and the failure rate is reduced. The use of rare earth permanent magnets can also increase the air gap flux density, increase the motor speed to the optimum value, and improve the power-to-mass ratio. Almost all generators used in contemporary aviation and aerospace use rare earth permanent magnet generators. Its typical products are 150 kVA 14-pole 12 000 r/min ~ 21 000 r/min and 100 kVA 60 000 r/min rare earth cobalt permanent magnet synchronous generators manufactured by General Electric Company of the United States. The first rare earth permanent magnet motor developed in China is a 3 kW 20 000 r/min permanent magnet generator.
Permanent magnet generators are also used as auxiliary exciters for large turbogenerators. In the 1980s, my country successfully developed the 40 kVA-160 kVA rare earth permanent magnet auxiliary exciters with the largest capacity in the world at that time, equipped with 200 MW-600 MW turbogenerators. Greatly improve the reliability of power station operation.
At present, internal combustion engine-driven small generators for independent power sources, permanent magnet generators for vehicles, and small permanent magnet wind turbines directly driven by wind wheels are being gradually promoted.
2. High-efficiency permanent magnet synchronous motor Compared with induction motor, permanent magnet synchronous motor does not need reactive excitation current, can significantly improve power factor (up to 1, even capacitive), reduces stator current and stator resistance loss, and There is no rotor copper loss during stable operation, which can reduce the fan (even the fan can be removed for small-capacity motors) and the corresponding wind friction loss, and the efficiency can be increased by 2 to 8 percentage points compared with the induction motor of the same specification. Moreover, the permanent magnet synchronous motor can maintain high efficiency and power factor in the range of 25% to 120% of the rated load, so that the energy saving effect is more significant during light load operation. This type of motor generally has a starting winding on the rotor, which has the ability to start directly at a certain frequency and voltage. At present, it is mainly used in fields such as oil fields, textile and chemical fiber industries, ceramic glass industries, and fans and pumps with long annual operating hours.
The high-efficiency and high-starting torque NdFeB permanent magnet synchronous motor independently developed by my country can solve the problem of "big horse-drawn trolley" in oil field applications. The starting torque is 50% to 100% larger than that of induction motors, which can replace a larger frame size Induction motors, the power saving rate is about 20%.
The moment of inertia of the load in the textile and chemical fiber industry is large, requiring high pull-in torque. Reasonable design of no-load leakage coefficient, salient pole ratio, rotor resistance, permanent magnet size and stator winding turns of permanent magnet synchronous motor can improve the pull-in performance of permanent magnet synchronous motor and promote its application in new textile and chemical fiber industries.
Motors for fans and pumps of hundreds of kilowatts and megawatts used in large-scale power stations, mines, petroleum, and chemical industries are large energy consumers. However, the efficiency and power factor of the motors currently used are low. After switching to NdFeB permanent magnets, not only It improves the efficiency and power factor, saves energy, and has a brushless structure, which improves the reliability of operation. At present, the 1120kW permanent magnet synchronous motor is the most powerful asynchronous start high-efficiency rare earth permanent magnet motor in the world. Its efficiency is higher than 96.5% (the efficiency of the same specification motor is 95%), and its power factor is 0.94. It can replace 1 to 2 powers larger than it Grade ordinary motors.
3. AC servo permanent magnet motors and brushless DC permanent magnet motors are now increasingly using variable frequency power supplies and AC motors to form AC speed control systems to replace DC motor speed control systems. In the AC motor, the speed of the permanent magnet synchronous motor maintains a constant relationship with the power frequency during stable operation, so that it can be directly used in an open-loop frequency conversion speed regulation system. This type of motor is usually started by gradually increasing the frequency of the frequency converter. There is no need to set a starting winding on the rotor, and the brush and commutator are omitted, which is convenient for maintenance.
The permanent magnet synchronous motor powered by the frequency converter and the closed-loop control system of the rotor position constitute a self-synchronous permanent magnet motor, which not only has the excellent speed regulation performance of the electric excitation DC motor, but also realizes brushless, and is mainly used in high control precision and high reliability. Sexual occasions, such as aviation, aerospace, CNC machine tools, machining centers, robots, electric vehicles, computer peripherals, etc.
NdFeB permanent magnet synchronous motors and drive systems with wide speed range and high constant power speed ratio have been developed. The speed ratio is as high as 1:22 500 and the limit speed reaches 9 000 r/min. The permanent magnet synchronous motor has the characteristics of high efficiency, small vibration, low noise and high torque density, and it is the most ideal motor in driving devices such as electric vehicles and machine tools.
With the continuous improvement of people's living standards, the requirements for household appliances are getting higher and higher. For example, household air conditioners are not only large power consumers, but also the main source of noise. The development trend is to use permanent magnet brushless DC motors with stepless speed regulation. It can automatically adjust to the appropriate speed to run for a long time according to the change of room temperature, reduce noise and vibration, make people feel more comfortable, and save 1/3 of the power consumption of the air conditioner without speed regulation. Others such as refrigerators, washing machines, dust collectors, fans, etc. are also gradually switching to brushless DC motors.
4. The permanent magnet DC motor adopts the permanent magnet excitation, which not only retains the good speed regulation characteristics and mechanical characteristics of the electric excitation DC motor, but also has the advantages of simple structure and process, small volume and high efficiency because the excitation winding and excitation loss are omitted. Less copper, high efficiency and other characteristics. Therefore, permanent magnet DC motors are widely used in household appliances, portable electronic equipment, electric tools, and precision speed and position transmission systems that require good dynamic performance. Among the micro DC motors below 500 W, permanent magnet motors account for 92%, while permanent magnet motors below 10 W account for more than 99%.
At present, my country's automobile industry is developing rapidly. The automobile industry is the largest user of permanent magnet motors. Motors are key components of automobiles. In a super luxury car, there are more than 70 motors for various purposes, most of which are low-voltage permanent magnet motors. Magnetic DC micromotor. The starter motors for automobiles and motorcycles can reduce the weight of starter motors by half by using NdFeB permanent magnets and planetary gears for reduction.
Classification of permanent magnet motors
There are many types of permanent magnet motors. According to the function of the motor, it can be roughly divided into two categories: permanent magnet generator and permanent magnet motor.
Permanent magnet motors can be further divided into permanent magnet DC motors and permanent magnet AC motors. The permanent magnet AC motor refers to a multi-phase synchronous motor with a permanent magnet rotor, so it is often called a permanent magnet synchronous motor (PMSM).
Permanent magnet DC motors are classified according to whether they have motors and commutators. It can be further divided into permanent magnet brushed DC motor and permanent magnet brushless DC motor (BLDCM).
In today's world, modern power electronics theory and technology are developing greatly. With the continuous advent of power electronic devices, such as MOSFET, IGBT, MCT, etc., fundamental changes have taken place in control devices. Since F. BlascEke proposed the principle of AC motor vector control in 1971, the development of vector control technology has created a new era of AC servo drive control. The continuous introduction of various high-performance microprocessors has further accelerated the replacement of DC servo systems by AC servo systems. development of. It has become an inevitable trend that the AC servo system replaces the DC servo system. However, the permanent magnet synchronous motor (PMSM) with sine wave back EMF and the brushless DC motor (BLIX~) with trapezoidal back EMF will become the mainstream of developing high-performance AC servo system because of their excellent performance.
Precautions for permanent magnet motors
1. Magnetic circuit structure and design calculation
In order to give full play to the magnetic properties of various permanent magnet materials, especially the excellent magnetic properties of rare earth permanent magnets, and manufacture cost-effective permanent magnet motors, the structure and design calculation methods of traditional permanent magnet motors or electric excitation motors cannot be simply applied. , must establish a new design concept, re-analyze and improve the magnetic circuit structure. With the rapid development of computer hardware and software technology, as well as the continuous improvement of modern design methods such as electromagnetic field numerical calculation, optimization design and simulation technology, through the joint efforts of the electrical academia and engineering circles, the design theory of permanent magnet motors, Breakthroughs have been made in calculation methods, structural technology and control technology, and a complete set of analysis and research methods and computer-aided analysis and design software combining electromagnetic field numerical calculation and equivalent magnetic circuit analytical solution have been formed, and are being continuously improved. .
2. Control issues
After the permanent magnet motor is made, it can maintain its magnetic field without external energy, but it also makes it extremely difficult to adjust and control its magnetic field from the outside. It is difficult for permanent magnet generators to adjust their output voltage and power factor from the outside, and permanent magnet DC motors can no longer adjust their speed by changing the excitation. These limit the application range of permanent magnet motors. However, with the rapid development of power electronic devices such as MOSFETs and IGBTs and control technologies, most permanent magnet motors can be used without magnetic field control but only with armature control. The design needs to combine the three new technologies of rare earth permanent magnet materials, power electronic devices and microcomputer control, so that the permanent magnet motor can operate under brand-new working conditions.
3. Irreversible demagnetization problem
If the design or use is improper, the permanent magnet motor is under the action of the armature reaction generated by the impact current when the temperature is too high (NdFeB permanent magnet) or too low (ferrite permanent magnet), or under severe mechanical vibration. There may be irreversible demagnetization, or demagnetization, which will reduce the performance of the motor and even make it unusable. Therefore, it is necessary to research and develop methods and devices for checking the thermal stability of permanent magnet materials suitable for motor manufacturers, and to analyze the anti-demagnetization capabilities of various structural forms, so that corresponding measures can be taken to ensure Permanent magnet motors do not lose magnetism.
4. Cost issues
Ferrite permanent magnet motors, especially miniature permanent magnet DC motors, are widely used because of their simple structure and process, light weight, and generally lower total cost than electric excitation motors. Since rare earth permanent magnets are still relatively expensive at present, the cost of rare earth permanent magnet motors is generally higher than that of electric excitation motors, which needs to be compensated by its high performance and operating cost savings. In some occasions, such as the voice coil motor of the computer disk drive, the performance of NdFeB permanent magnets is improved, the volume and mass are significantly reduced, and the total cost is reduced. In the design, it is necessary to compare the performance and price according to the specific use occasions and requirements to decide the choice, and to innovate the structure and process and optimize the design to reduce the cost.