12 world top new energy vehicle motor suppliers!
The core technology that distinguishes new energy vehicles from traditional gasoline vehicles is the "three electrics": drive motor, power battery and vehicle electronic control, which can be said to be the three hearts of new energy vehicles.
While many new car manufacturers claim that they have mastered the "three electric" technologies, incidents of spontaneous combustion of electric vehicles on the road continue to occur. For example, one month ago, one of the trial vehicles in the WM Motor Research Institute caught fire and spontaneous combustion.
Behind the spontaneous combustion incident of new energy vehicles is doubts about the maturity of the core technology of the product. From the perspective of core three-electric technology and product safety, the threshold here is actually very high. No matter at home or abroad, enterprises still need to continuously invest a lot of research and development here.
Drive motor, as one of the three core components of new energy vehicles, has higher technical requirements than traditional industrial motors, and it is also a research and development direction that vehicle companies currently value.
1. Foreign traditional auto parts suppliers
1. Siemens (SIEMENS)
Company name: Siemens AG
Location: Germany
Founded: 1847
Research direction: Focus on the field of electrical and electronic engineering of electrification, automation and digitalization
Main products: Siemens' products focus on electric motors for electric and hybrid drives, ranging from 30 kW to 170 kW.
1. SIVETEC induction motor
Through innovation, SIVETEC induction motors achieve a higher power density, up to 95%.
SIVETEC permanent magnet motor
The permanent magnet synchronous motor has an energy efficiency of up to 96%, which is the best solution for applications with limited space but high power requirements. Siemens can apply its extensive experience in the field of industrial applications to PM technology to develop and realize many visions of the automotive industry.
Cooperative enterprises: Valeo, Shanghai Sunwin Bus, Green Packet, BAIC New Energy, Volvo Cars, Kia Motors, Volkswagen
Latest news: On January 18, 2018, Shanghai Zhonglianeng Innovative Energy Technology Co., Ltd. (hereinafter referred to as "Zhonglianengchuang") and Siemens reached a cooperation agreement on the localized production of electric drive systems for new energy commercial vehicles. The two parties will further deepen local cooperation on the basis of Siemens' global technology and development experience, and carry out localized production of Siemens' electric drive system technology.
In May 2018, Siemens announced to become a strategic partner of China's own brand new energy vehicle company "WM Motor Technology Co., Ltd." ("WM Motor"), helping WM Motor to comprehensively sort out the process and management of the product production cycle Implement a unified solution to build an innovative digital enterprise.
2. Hitachi Automotive Systems
Company Name: Hitachi Automotive Systems Co., Ltd.
Location: Japan
Founded: 1910
Research direction: Committed to household appliances, computer products, semiconductors, industrial machinery and other products, it is the largest comprehensive motor manufacturer in Japan.
Main products: As early as 1999, Hitachi began to put electric vehicle motors on the market. So far, the small, light-weight and high-power electric vehicle motor products developed by Hitachi have been widely used by global automobile manufacturers. Moreover, it is the only HEV drive system supplier in the world that can comprehensively provide motors, frequency converters, and transmission controllers as a supplier of comprehensive drive systems
Hitachi will gradually transform from the current engine-centered to the electric drive technology based on electric motors and inverters, helping to accelerate the development of hybrid electric vehicles (HEV), electric vehicles (EV), and fuel cell vehicles (FCEV).
1. Hitachi's electric four-wheel drive system that realizes comprehensive and coordinated control of the driving force of the electric motor and the driving force of the engine
2. Permanent magnet motor
Partners: Honda, Chevrolet, etc.
The latest news: Honda and Hitachi Automotive Systems (Hitachi AMS) jointly formed a team in July 2017 to establish a joint venture company to develop, produce and sell electric vehicle drive motors; on September 7, 2018, its joint venture company Hitachi Automotive Motor Systems The groundbreaking ceremony of the production base was held in the state-level Zengcheng Economic and Technological Development Zone, and it is expected to be completed and put into production in two years.
3. Continental
Company name: Continental AG
Location: Germany
Founded: 1871
Research direction: The automotive business mainly focuses on the technology research of automotive tires, chassis and safety, body electronics, powertrain and other components
Main products: Continental's motor products include electrically excited synchronous motors, permanent magnet synchronous motors (PMSM) and induction motors (IM)
Wait. Its high-voltage shaft drive system is highly integrated, integrating the motor, gearbox and power electronics. It can be applied to all performance levels from 80kW-130kW, and is widely used in various types of vehicles.
1. The power of the new electric drive system can reach 60kW-120kW, and it has good scalability, and is suitable for any vehicle, including plug-in hybrid vehicles and pure electric vehicles. In addition, it is compatible with asynchronous motors (ASM) and permanent magnet synchronous motors (PSM).
2. The third-generation high-voltage shaft drive system is a three-in-one highly integrated design integrating motor, reducer and inverter. Due to the omission of some high-voltage cables and connectors during integration, the weight is reduced by about 30%, and the cost is also relatively saved by 20%. It can be expanded up to 300kw and weighs only 75kg. This product is expected to be mass-produced in China in 2019.
Partners: Daimler, Baidu, NIO, FAW Jiefang, Didi Chuxing
Latest news: In July 2018, Continental and Didi Chuxing formally signed a strategic cooperation agreement. Based on Continental's advanced products and technologies in the field of Internet of Vehicles, rich experience in design and engineering research and development, and Didi's practical experience in the field of travel, the two parties will carry out projects in various forms in the field of intelligent networked vehicles and customized new energy vehicles Cooperation;
In July 2018, Continental announced that in early 2019, its powertrain division would be split into an independent entity. Meanwhile, the powertrain division will be launched in mid-2019;
At the 2018 Global Future Mobility Conference, which will open on September 20, Continental will showcase a series of electrification-related solutions.
4. Bosch
Company name: Bosch (BOSCH)
Location: Germany
Founded: 1886
Research direction: covering automotive, industrial technology, consumer goods, energy and construction technology and other aspects of component technology research.
main products:
1. In 2011, Bosch and Daimler established EM-motive, and the electric motors produced will be used in Mercedes-Benz and some small cars. By 2020, the joint venture is expected to produce 1 million electric motors.
2. Electric drive system eAxle
Mass production is expected in 2019, maximum output power: 50 - 300kW, maximum motor speed: 16000rpm. Can be installed in hybrid or pure electric vehicles,
Compared with traditional motors, Bosch's eAxle electric drive system can expand the modular platform, enabling rapid development of different power products and adapting them to different models, greatly shortening the development cycle, thereby bringing about 5%-10% cost-effectiveness. At the same time, the system can be highly integrated, and the volume is reduced by 20% compared with the traditional electric vehicle powertrain system.
Partners: Volkswagen, Daimler, BMW, Nikola, etc.
Latest news: On July 9, 2018, NIO and Bosch Group signed a strategic cooperation agreement in Berlin, Germany. The two parties will carry out key cooperation in the fields of sensor technology, autonomous driving, motor control and intelligent transportation systems.
Recently, Bosch announced plans to launch a series of drive motor products in 2019, which will be applied to pure electric freight vehicles with a total weight of 2 to 7.5 tons.
2. OEMs
2.1 BYD
Company Name: BYD Co., Ltd.
Location: Shenzhen, China
Founded: 1995
Research direction: In the automotive business, BYD focuses on technology research in vehicle manufacturing, mold research and development, model development, new energy, etc.; Product and technology research and development, as well as industry and market research, etc.
Main product: The motor developed and produced by BYD is a permanent magnet DC motor, which has been greatly improved in terms of efficiency and power density. However, its technical reserves and application fields are not yet mature, and the high cost of rare earth materials contained in permanent magnets has always been a persistent problem of permanent magnet synchronous motors.
1. Permanent magnet synchronous machine
Applied to BYD Yuan EV and other models, with a peak power of 160kW and a peak torque of 310Nm;
2. Motor control technology
BYD's drive motor adopts high-performance space vector pulse width modulation technology, more reliable IGBT drive protection technology, and high-precision rotary encoder to calculate the angular position of the motor rotor. Through the application of the above three free technologies, the safety, reliability and stability of BYD's new energy vehicles have been greatly improved.
Cooperative enterprises: BYD, Shenzhen Tengshi New Energy Automobile Co., Ltd. (a joint venture between BYD and Daimler)
The latest news: BYD's annual installed capacity is 91,858 units, which are mainly supplied to two car companies: BYD and its joint venture with Daimler. Among them, 87,734 BYD units were supplied throughout the year, accounting for more than 95.5%; 4,124 units were supplied to joint ventures;
On August 23, BYD signed an investment cooperation agreement to invest 10 billion yuan to build a power battery industry project with an annual output of 20GWh in Bishan District, Chongqing;
On September 9, the signing ceremony of BYD's 30GWh power battery project was held in Xi'an High-tech Zone. The project plans to invest a total of 12 billion yuan. After completion, it will become another "super factory" in the power battery industry;
2.2 BAIC New Energy
Company Name: Beijing New Energy Automobile Co., Ltd.
Location: Beijing, China
Founded: 2009
Research direction: Mainly engaged in technical research on the assembly of new energy vehicle power modules (specifically including power module motor system assembly, power module battery system assembly and power module electronic control system assembly), electric passenger vehicle production, etc.
Main products: The permanent magnet synchronous motor of BAIC New Energy is independently developed by it. In addition to the advantages of high power and large torque, it also has the advantages of small size, light weight and high reliability;
1. Permanent magnet synchronous motor
BAIC BJEV uses advanced electromagnetic design technology, multi-objective limit design, multi-field accurate analysis and system integration simulation technology applicable to new energy passenger vehicles to achieve a significant performance improvement.
The rated power of the motor is 160kW, and the starting acceleration is fast, which is equivalent to the torque output of a 2.0T engine, and the system output torque is large
2. e-Motion Drive super electric drive technology
The e-Motion Drive 2.0 intelligent electric drive not only breaks through innovations in hardware, but also develops a self-learning system in terms of software. Compared with the first-generation system such as the front cabin, four units are simplified into one assembly At the same time, through the integrated and intelligent management of vehicle batteries, motors, and electronic control systems, compared with the first-generation electric drive system, the number of main components is reduced by 30%, and the weight is reduced by 20%; the energy conversion rate is increased to 97%. %.
Cooperative enterprises: BAIC New Energy, Changhe Suzuki
Latest news: In 2017, BAIC BJEV's annual installed capacity reached 99,429 units, mainly supplying BAIC BJEV and Changhe Suzuki, of which 98,506 units were supplied to BAIC BJEV, accounting for over 99%; only 923 units were supplied to Changhe Suzuki.
At the beginning of September, BAIC New Energy acquired related assets of BAIC's Huanghua base, which will be used to build an economical pure electric vehicle production base to improve the industrial layout of BAIC New Energy.
On September 12, equipped with the latest motor products, BAIC New Energy EU5 was officially launched in the Central Plains region. EU5 is positioned as a "new model of artificial intelligence cars". According to the length of mileage, it is divided into two versions: R500 and R550. Among them, the R500 has a battery life of 416 kilometers and a constant speed of 520 kilometers; the R550 has a battery life of 460 kilometers and a constant speed of 570 kilometers.
2.3 Yutong Bus
Company Name: Zhengzhou Yutong Bus Co., Ltd.
Location: Zhengzhou, China
Founded: 1997
Research direction: Import business of raw and auxiliary materials, mechanical equipment, instruments and meters, spare parts and related technologies required for scientific research; operating the company's incoming material processing and "three to one supplement" business; bus and accessories, accessories, bus chassis design, production and sales; mechanical processing, technology development of automobiles and parts
Main products: The "Rui Control" bus control system independently developed by Yutong Bus, through the electronic control system, the five systems of vehicle control, vehicle energy, electrical accessories, motor drive and power make the electric bus run more efficiently
1. "Ruikong" bus control system
The "drive electrification" of Yutong buses is realized by the control of dual motors. The power transmission route of the whole vehicle is the engine, ISG motor, drive motor, transmission shaft, and main reducer. Two driving modes of hybrid drive, replace the traditional gearbox with high-efficiency motor, realize stepless speed change, improve driving comfort and improve reliability at the same time.
Cooperative enterprises: Yutong Bus, Dayun Automobile
Latest news: On August 28, 2018, in Zhengzhou, Henan, Yutong's new generation of commercial passenger car CL6 finally unveiled its mystery and officially released it to the market. This is another major product move of Yutong following the new upgrade of the whole series of new energy buses and "dual-configuration" hydrogen fuel cell buses this year.
On August 31, 2018, the Henan Provincial Delegation attending the 6th China-Eurasia Expo visited and inspected the Urumqi Branch of Zhengzhou Yutong Bus Co., Ltd. During the visit, He Songhao pointed out that Yutong Bus is a well-known brand product in Henan, and choosing to invest and build a large-scale branch in Xinjiang will play an important role in the development of local economy in Xinjiang and in promoting the export of Yutong Bus to five countries in Central Asia.
3. Professional motor control manufacturer
3.1 Dayang Motor's new power
Company name: Dayang Electric New Power Technology Co., Ltd.
Location: Zhongshan, China
Founded: 2000
Research direction: Dayang Electric is widely used in household appliances, automobiles, motorcycles, electric locomotives, bread machines, automatic control and other industries. The products involve single-phase capacitor asynchronous motors, shaded pole motors, DC motors, single-phase series motors, external rotor capacitors Technical research on the operation of six series of single-phase asynchronous motors and more than 500 varieties
Main products: The company's permanent magnet synchronous motors and drive system products for vehicles have the characteristics of high efficiency, wide range of high-efficiency work, large speed range and low torque pulse. Dayang Motor currently produces products with a wide power range, including 7.5kW, 15kW, 20kW, 30kW, 60kW, 110kW and 130kW series, which are widely used in 2T--8T urban sanitation vehicles, 12m pure electric buses, Midi cars (Foton ), Saab cars, etc.
Cooperative enterprises: Beiqi Foton, SAIC, FAW, Jianghuai Automobile and other enterprises
Latest news: At present, batch supply to BAIC New Energy, Beiqi Foton, Beijing Hyundai and Changan Automobile has been realized;
Dayang Motor stated on the investor interaction platform on August 23 that the company is an important supplier of BAIC New Energy, and its main supporting models include EV, EU, EX, and ARCFOX.
3.2 Shanghai EDRIVE
Company name: Shanghai Electric Drive Co., Ltd. (now acquired by Dayang Electric)
Location: Shanghai, China
Founded: 2008
Research direction: Mainly engaged in the R&D, production and sales of electric drive systems for new energy vehicles
Main products: At present, the company has formed a research and development platform suitable for hybrid and plug-in passenger cars, fuel cell and pure electric cars, hybrid and plug-in cars, small pure electric cars, etc., and has formed a series of products covering The power range of 3kW-200kW has been established, and more than 200 varieties of electric drive system products have been developed for domestic and foreign vehicle manufacturers.
1. The 35kW drive system and 35kW two-in-one system are suitable for passenger cars, with peak power: 35kW, rated power: 18 kW, applicable models: A00-class models, Zhidou D2 and Zhidou D3 are equipped with Shanghai Electric driven motor.
2. Double planetary row system suitable for commercial vehicles, peak power: drive 150kW, rated power: drive 100kW, applicable models: hybrid over 10 meters
Cooperative enterprises: Geely, Huatai, Chery, SAIC Motor, etc.
The latest news: The company's products are widely used in domestic and foreign well-known vehicle companies such as FAW Group, Chery, Dongfeng, Changan, Brilliance, Geely, GAC, Great Wall, SAIC, Shanghai, Volkswagen, Volkswagen, BAIC Group, Chongqing Yu'an, Jiangling, etc. application.
In January 2018, Shanghai Electric Drive and Dongfeng Industrial Co., Ltd. established a joint venture company to develop new energy vehicle powertrain systems.
3. CATL
Company Name: Ningde Times Motor Technology Co., Ltd.
Location: Shanghai
Founded: 2017
Research direction: Mainly for electric motor manufacturing, automotive engine manufacturing, generator and generator set manufacturing, micro motor and component manufacturing and other technology research and development; engaged in new energy vehicle motor, electronic control and key parts research and development and production
Main products: Its generator is the only generator in China that has been certified by UL in the United States; its products are mainly concentrated in the fields of commercial vehicles, buses, logistics vehicles, environmental protection vehicles, etc., and have covered motors, electronic controls, control software, electric drive assembly into its core components.
1. Water-cooled synchronous drive dual motors
The driving motor runs for a long time and has a wide operating speed range, and the engine is connected to the SG generator to improve efficiency to a greater extent. Currently equipped with King Long hybrid 12m buses, achieving a fuel saving rate of 46.9%
2. Water-cooled permanent magnet synchronous drive motor
It adopts the design of embedded permanent magnet + high excitation capacity rotor, and is equipped with two patented technologies for power motor winding and armature manufacturing. Small size, light weight, high speed, motor efficiency greater than 95%, relatively strong environmental adaptability. At present, complete vehicle supply has been carried out in Jinlong, Sinotruk and other car companies.
Cooperative enterprises: CRRC, King Long, Geely, Weichai Power, Sinotruk and other enterprises
The latest news: At present, Times Motor has the development capabilities of new energy pure electric buses, minibuses, commercial vehicles, sedans, sweepers, forklifts and tricycles, as well as generators, drive motors and powertrains of hybrid vehicles. The products cover a full range of generators, drive motors and powertrain products;
In August 2018, the Ministry of Industry and Information Technology released the "Catalogue of Recommended Models for the Promotion and Application of New Energy Vehicles" (the ninth batch in 2018). This batch of recommended catalogs includes a total of 288 models from 108 companies. The first place, reaching 82 models, accounting for about 28% of the number of supporting power batteries this time;
4. Jingjin Electric
Company Name: Jingjin Electric Technology Co., Ltd.
Location: Beijing
Founded: 2008
Research direction: research and development of automotive and industrial clean energy technology, electric drive technology, sales of self-developed products, and technical consultation
Main products: Products include drive motor systems for electric vehicles, hybrid vehicles, plug-in hybrid vehicles and other new energy vehicles. Jingjin Electric has successfully developed a 140kW drive motor and a 100kW high-performance generator and drive motor.
1.140kW drive motor
Applicable to the pure electric power system of small/compact cars, peak power: drive 140kW; the maximum efficiency of the motor reaches 96%
2.100kW high-performance generator
Suitable for small car/MPV/SUV plug-in hybrid system, peak power: drive 140kW.
Partners: Great Wall, GAC, Geely, Xiaopeng Motors, Fisker Automobiles
Latest news: This year, Jingjin Electric provides supporting motor services for many car companies, including Geely Automobile, GAC Motor, GAC Mitsubishi and Haima Automobile, and in July, the installed capacity of drive motors for new energy passenger cars ranked No. 1 in the country two.
5. Juyi
Company Name: Juyi Automation Equipment Co., Ltd.
Location: Anhui
Founded: 2005
Research direction: The first batch of national high-tech enterprises engaged in the research and development, production and sales of new energy vehicle motors and their control systems. The research covers intelligent manufacturing complete sets of automobiles and their key components and new energy vehicle electric drive systems.
Main products: Mainly produce permanent magnet synchronous motors, including 41KW electric drive system, 90KW electric drive system, 50KW electric drive system, 42KW electric drive system, etc.
1.90kw drive motor and its controller
Suitable for pure electric vehicles, rated power: 45kW; rated speed: 5000rpm
2.20kw drive motor and its controller
Suitable for hybrid vehicles, rated power: 10kW; peak speed: 5500rpm
Cooperative enterprises: Jianghuai Automobile, Chery Automobile, Yundu Automobile, etc.
The latest news: In 2017, the total installed capacity of Anhui Juyi Power was 27,065 sets, of which 16,983 sets were equipped with JAC's models, mainly including JAC iEV7s, JAC iEV6E and other hot-selling models, and also provided motor support for Chery eQ1.
On April 12, 2018, the 2018 New Energy Vehicle Power Transmission System and Assembly and Testing Technology Development Forum, sponsored by Juyi Automation Equipment Co., Ltd. and co-organized by China Automobile Manufacturing Equipment Innovation Alliance, officially kicked off in Hefei.
In June and July 2018, the installed capacity of drive motors for new energy passenger vehicles in Hefei Juyi ranked third in the country, with nearly 5,000 units.
-
First, the drive motor should have a higher energy density to achieve light weight and low cost, and adapt to the limited interior space of the car. At the same time, it should have energy feedback capability to reduce the energy consumption of the whole vehicle; -
Second, the drive motor has both high-speed wide speed regulation and low-speed high torque to provide high starting speed, climbing performance and high-speed acceleration performance; -
Third, the electronic control system must have high control precision, high dynamic response rate, and provide high safety and reliability at the same time.
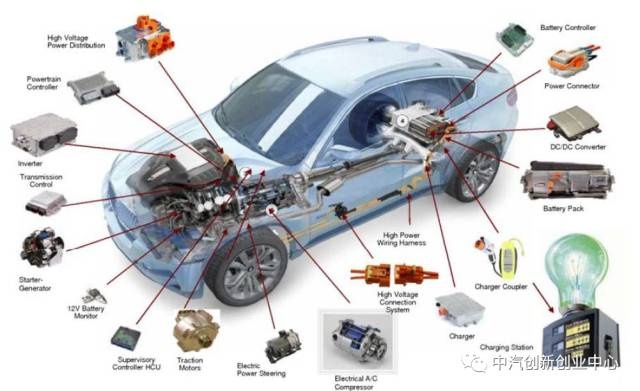
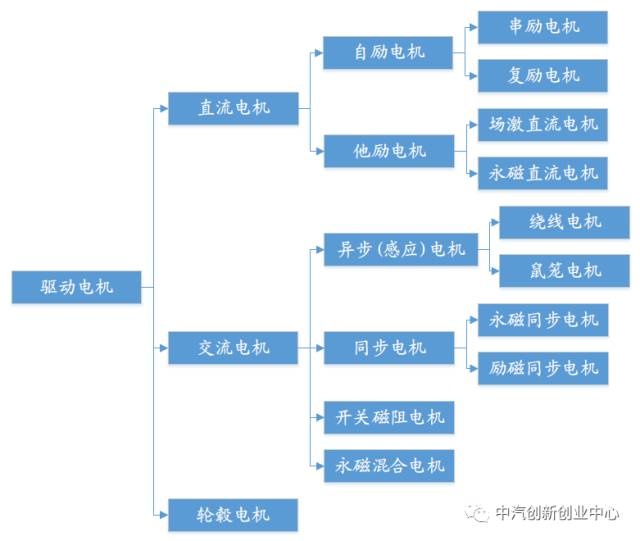
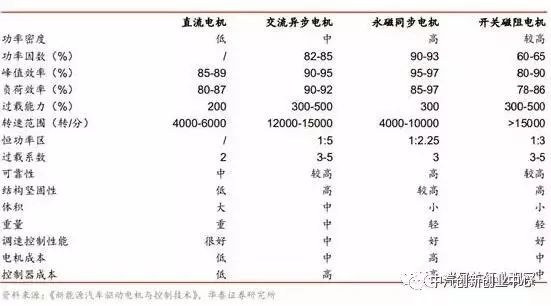
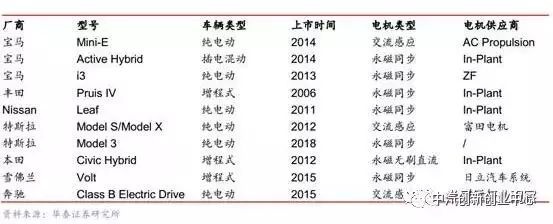
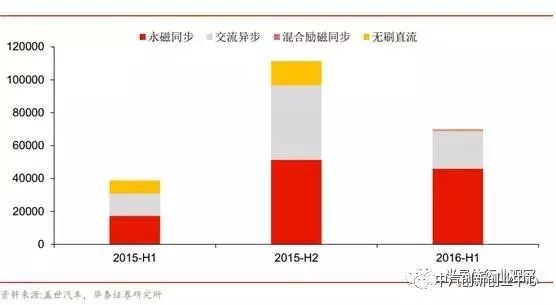
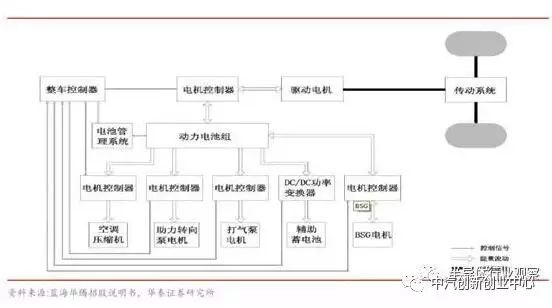
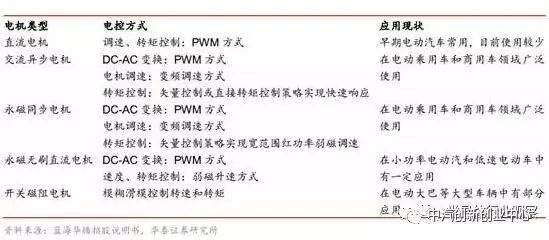
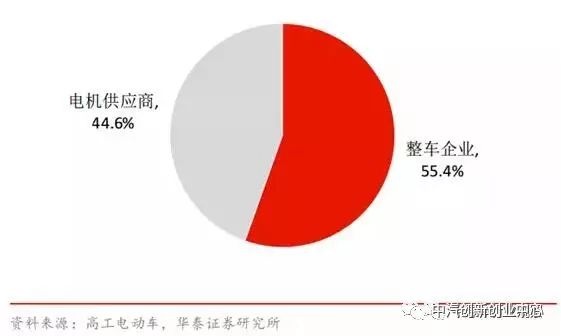
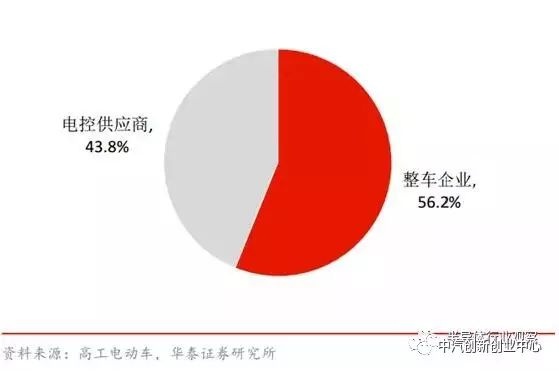
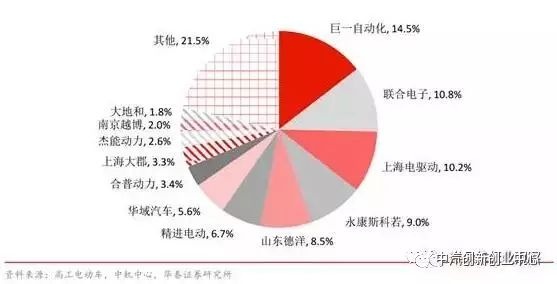
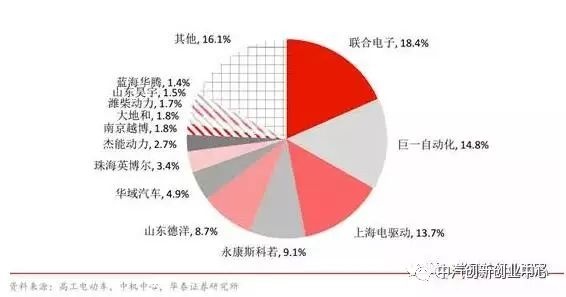
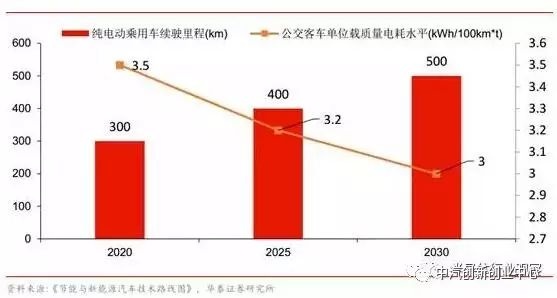
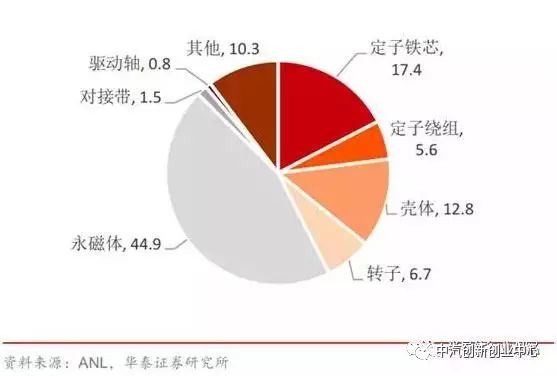

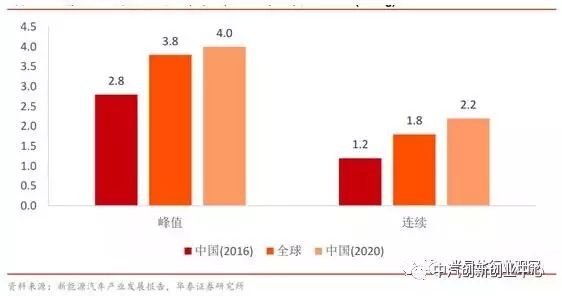
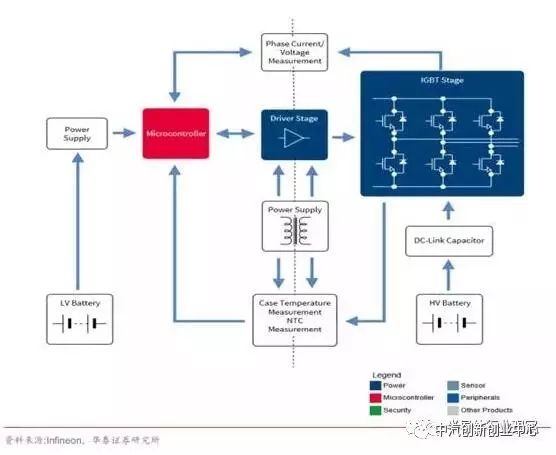
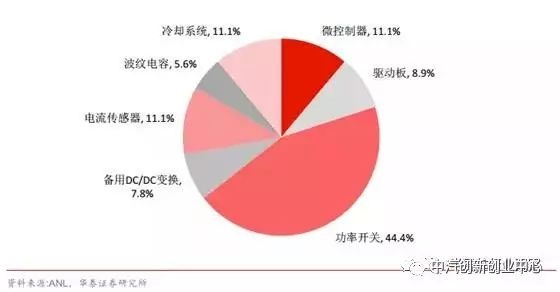
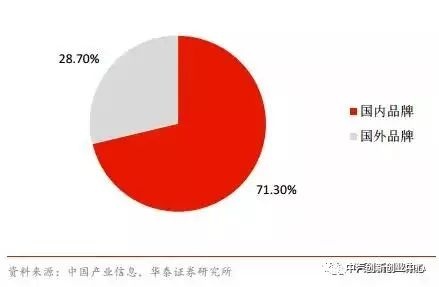
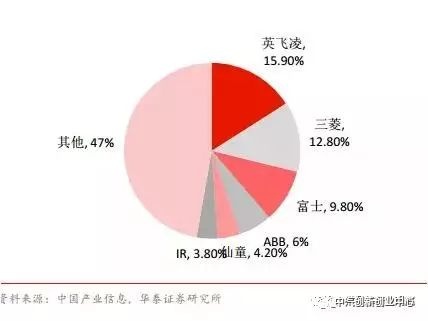
Comparison of the advantages and disadvantages of various new energy motors
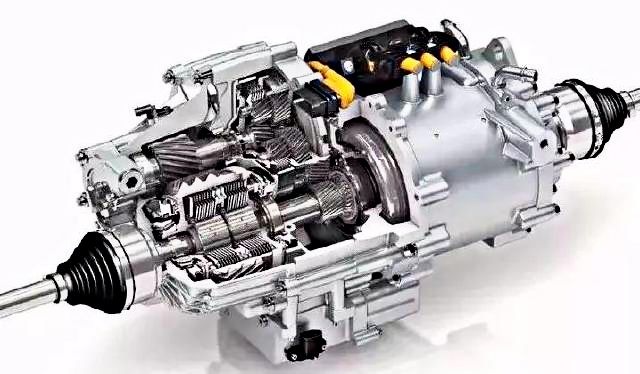
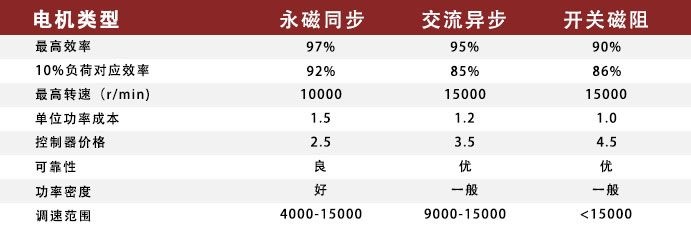
END