Understand the basics of pure electric vehicles
The basic components of pure electric vehicles
The main function of the generator is to convert mechanical energy into electrical energy, which is represented by the letter G in the circuit.
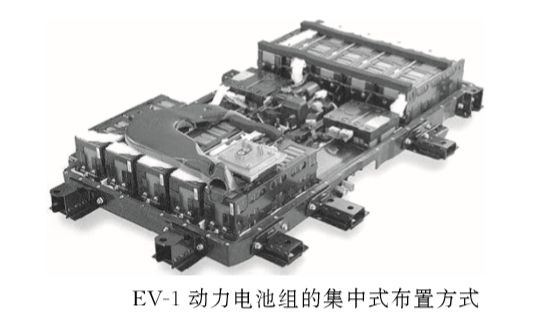
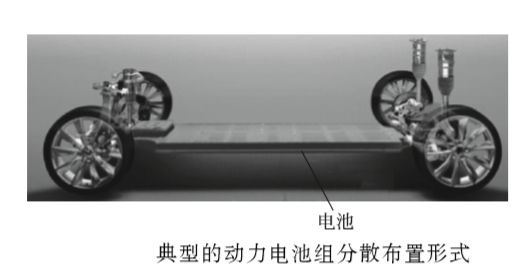
Types of pure electric vehicles
How Pure Electric Vehicles Work
Classification of pure electric vehicles
Classification by drive system composition and arrangement
The mechanical transmission type pure electric vehicle is developed on the basis of the structure of the front and rear-wheel drive of the engine of the fuel vehicle, and the transmission system of the internal combustion engine vehicle is retained. The difference is that the internal combustion engine is replaced by an electric motor. This structure can ensure the starting torque of the pure electric vehicle and the backup power at low speed, and has low requirements on the drive motor, so a motor with a lower power can be selected.
C—clutch; D—differential; FG—fixed ratio reducer; GB—transmission; M—motor
A structure of a pure electric vehicle without transmission is shown in the figure. The biggest feature of this structure is that the clutch and transmission are cancelled, and a fixed speed ratio reducer is used to realize the speed change function by controlling the electric motor. The advantage of this structure is that the mechanical transmission device is light in weight and small in size, but the requirements for the motor are relatively high, not only requiring high starting torque, but also requiring large backup power to ensure the starting of pure electric vehicles. , climbing, acceleration and other dynamic performance.
Classification according to the number of vehicle power supplies
Key Technologies of Pure Electric Vehicles