Motor rotor dripping paint insulation treatment process
The motor involves the insulation process from winding the coil to assembling the finished product. Motor insulation has always been an important link in motor production. According to production experience, once the motor insulation structure is determined, electromagnetic wires, lead wires, shaft insulation, slot insulation, inter-turn insulation, wiring boards and other components are generally less likely to malfunction if properly selected.
If the insulation paint is improperly selected or the quality of the insulation paint is unstable during the insulation treatment process, or the insulation treatment process is not strictly followed, generally speaking, there will be many problems, and some problems are not easy to find at the time until the complete machine is installed or shipped. It does not appear until the customer, which will bring great losses to the company. Therefore, insulation treatment process designers, craftsmen and operators should pay enough attention to this link when selecting materials and process operations.
Insulation treatment is to fill the gaps between the winding insulation layers and the slots with a certain amount of insulating paint, glue and other impregnating agents, so that the entire winding insulation is bonded into a whole. The treated workpiece surface forms a dense, smooth and complete continuous paint film. This improves the heat resistance, thermal conductivity, electrical strength, mechanical strength and environmental medium corrosion resistance of the entire insulation structure. Different insulation treatment processes are selected according to different usage conditions and insulation structures of the product.
This article mainly introduces the insulation treatment materials and rotor drip paint-related processes suitable for power tool series motors (hereinafter referred to as motors).
1. Motor requirements for insulating paint
1. Electrical performance requirements
For electric tools, there are two main indicators: the electrical strength (E) and the insulation resistance coefficient (ρv, ρs) of the paint. For these two indicators, the insulating paint currently produced in my country can meet the requirements.
2. Mechanical properties
For electric tools, they are affected by vibration force, hot and cold impact force, and rotational centrifugal force, causing the temperature to rise instantaneously. Therefore, it requires good adhesion of the insulating paint. Especially at high temperatures (such as 155°C or 200°C), the bonding force must be strong, and the material itself must have a high thermal deformation temperature to maintain sufficient impact strength and toughness at high temperatures to ensure the safety of the motor under intense mechanical stress during operation. Works and has a long lasting life.
Penetration is important when it comes to impregnating paints. Paint-impregnated coils with poor penetration ability can easily lead to no paint in the depths, which will not improve the performance of other insulating materials in the depths, easily causing weaknesses, causing breakdown or shortening their lifespan. Generally speaking, paints that are excessively polymerized (viscosity increases when observed with the naked eye) or use inappropriate solvents have poor permeability. For some rotors that require a high slot filling rate and use enameled wire with a small diameter (for example, Φ0.20mm or less), they are required to have good permeability to the paint.
3. Thermal performance
When power tools are working, as the temperature rises, molecular materials will crack, hydrolyze, and oxidize, making the materials hard and brittle, and cracks will appear, resulting in reduced insulation resistance, electrical breakdown strength, mechanical strength, and stress deformation. etc. to increase. Therefore, improving the heat resistance of insulation materials is of great significance to ensure the safe operation of the motor and increase the power of the motor.
There are many methods to evaluate the thermal properties of paint films, such as thermoelasticity, temperature index, etc. The temperature index is recommended by the International Electrotechnical Commission to indicate the long-term heat resistance ability of insulation materials. Specifically, it uses a number to express its level.
4. Physical properties
The viscosity is required to be moderate to facilitate penetration and appropriate amount of paint; the solid content should be large to reduce the proportion and volatilization of the solvent as much as possible; the water absorption should be small; the color should be light; the paint film should have good cold and heat shock resistance, etc.
5. Chemical properties
Due to the different use occasions of insulating paint, the resistance to hot and humid weather, solvent resistance and compatibility with other insulating materials must be considered.
6. Process performance
Since the insulating paint is not the final product, it needs to be impregnated into the stator and rotor during the motor manufacturing process and then solidified before it can play its due role in the motor. Due to the large production volume of electric tools, it is required that the curing speed should be fast when impregnating rotors and stators, so as to ensure fast-paced production. The curing speed and the storage period (use period) of paint are a pair of contradictions. If the curing speed is fast, the storage period (use period) must be short. If the storage period (use period) is long, the curing speed must be slow.
In order to solve this contradiction, most of the dripping paints currently supplied on the market are supplied in a two-component form of paint base and curing agent. When using, the two-component insulating paint must be mixed according to the specified proportion before use. This requires a long service life and good permeability after the two-component insulating paint is prepared, but it must also have little loss and not have harmful effects on other materials such as copper wires.
7. Rationality and advancement of technology and economy
Power tools are large-volume and wide-ranging products similar to household appliances, and the material cost directly affects the product price. Therefore, while ensuring that the product has certain advanced indicators, economics must be considered, otherwise the product will lack competitiveness due to its high price.
2. The purpose of insulation treatment
Although the coils and other components of the motor already have certain insulation capabilities when they are made into the stator and rotor, for example, enameled wires are insulated by paint films; there are slots in the core slots for insulation, etc. However, a thin layer of paint film on the enameled wire serves as wire insulation, which is very weak and susceptible to damage. Moreover, the enameled wire, slot insulation, and slot wedges move with each other. When the motor starts running and stops, the insulating material has to withstand electromagnetic vibration and mechanical vibration. It is also subject to impact, moisture, dust, salt spray in the air, corrosive gases or liquid droplets in the working environment, and aging under heating conditions during operation. In order for the motor to work normally under such conditions, the coil must be connected to its Adjacent parts are impregnated with insulating paint, so that insulating components such as wires and slot insulation are encapsulated with insulating resin to form a dense and solid whole.
The most common motor failures during use are winding breakdown, winding short circuit, winding open circuit, winding burnout, etc. These are all motor insulation problems. The length of motor life mainly depends on the insulation quality, and the quality of motor insulation is not only related to the motor insulation structure, but also related to the motor insulation treatment. The insulation structure is a design issue, and the insulation treatment is a manufacturing process issue. Therefore, in order to ensure the long-term reliable operation of the motor, once the insulation structure is designed and finalized, the insulation treatment is a key link in motor manufacturing. The following purposes can be achieved through insulation treatment:
1. Improve the moisture resistance of motor insulation
Any insulating material in humid air will always absorb moisture to a greater or lesser extent. For example, electrical cardboard, etc., moisture in the air can easily penetrate into the insulating material along the capillary tubes, so the performance of the insulating material will be significantly reduced. The insulation treatment forms a smooth pinhole-free paint film or insulating sealing layer on the surface of the windings and coils, which can greatly reduce moisture intrusion, thereby improving the moisture-proof performance of the motor.
2. Improved heat resistance of motor insulation
Before the motor insulation material is impregnated with insulating paint, after the material is heated, the interior of the material will decompose into low-molecular substances such as gas water molecules, accompanied by oxidation, and the material properties will change, such as a decrease in mechanical strength, a decrease in moisture resistance, and the material becoming brittle. , the electrical properties such as insulation resistance and breakdown voltage are reduced successively. This phenomenon is called the aging of the insulating material. However, after the insulation treatment, the contact area between the insulating material and the air is greatly reduced, and the oxidation rate is greatly reduced. Under the same service life, , the operating temperature of the motor can be increased. Therefore, the heat resistance of the motor insulation is improved.
3. Improved thermal conductivity of the motor
There are a large number of air gaps in the motor insulation layer, and the thermal conductivity of the air gaps is low. After the air gaps are filled with impregnating paint, the impregnating paint and pouring body have better thermal conductivity than the air gaps, so the motor and electrical appliance windings are increased accordingly. The conduction of heat will greatly reduce the temperature rise of the motor. Experimental data shows that the temperature rise can be reduced by 10-20%.
4. Improve the electrical and mechanical properties of motor insulation
After the motor windings and coils are insulated, the windings and core are bonded into a solid whole. The paint film fills the gaps inside the windings and slots, forming an insulating layer of a certain thickness at the winding ends. There are no gaps or moisture inside. It is not easy to enter, so the insulation resistance and breakdown voltage are improved. At the same time, there is no relative movement between the winding and the core. It has sufficient mechanical strength to resist external vibration and stress, and withstand mechanical impact during the motor assembly process, thus avoiding mechanical effects of damage.
After the motor windings are impregnated, the winding insulation system and the iron core form a solid whole, which reduces the impact of mechanical vibration and electromagnetic force vibration caused by the motor during operation, plays a mechanical reinforcement role, and prevents the conductors from intersecting or interfering with each other. The insulation structure is damaged due to loose vibration and displacement friction with the core groove wall. The organic insulating material inside the motor not only improves the heat resistance and electrical properties after impregnation, but also improves the mechanical strength of the insulating material itself. Because when the insulating material is heated, the material will change. It will decompose and release gas, moisture and carbon, and the material will lose flexibility. However, after impregnation treatment, the processes such as cracking and hydrolysis in the hot state can be greatly delayed, and the mechanical flexibility of the material will be reduced. At the same time, the paint film formed by the insulating paint has a certain degree of elasticity and adhesion in the hot state, which strengthens the bonding force between materials and forms a solid whole, greatly improving the strength of the system.
5. Improve chemical corrosion resistance
After the motor is impregnated, it can prevent direct contact between the insulation material and various solvents and corrosive chemicals around the motor. This can improve the stability of the motor against chemical substances. Due to the insulation encapsulation, contact with external foreign matter is cut off. , improves the stability of the winding, and the selection of appropriate materials can also make the winding insulation anti-mildew, anti-oil, anti-corona, flame-retardant and other properties.
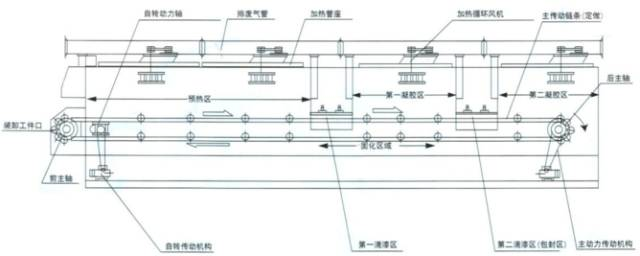
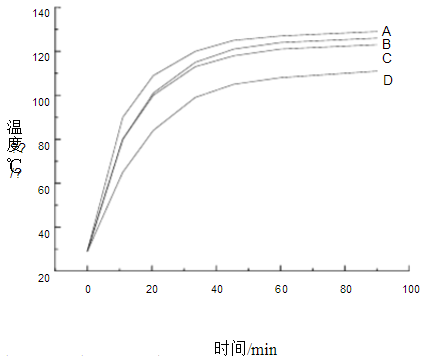
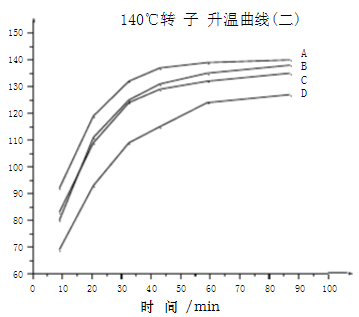
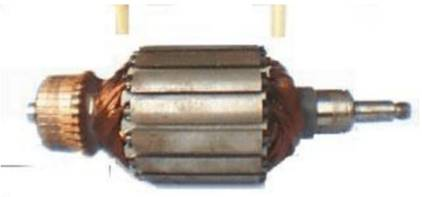