8 major market applications of high-speed motors!
High-speed motors have the advantages of high efficiency, large specific power, high power factor, high reliability and easy maintenance. In advanced industrial countries, high-speed motors have been widely used in aviation, aerospace and mold industries. my country's high-speed motor industry began in the 1990s. Products have continued to develop from low-end to high-end, and the market size has also continued to expand.
What is a high-speed motor? There is no clear boundary definition. Generally, any motor exceeding 10,000 r/min can be called a high-speed motor. It is also defined by the linear speed of the rotor rotation. The linear speed of a high-speed motor is generally greater than 50 m/s. The centrifugal stress of the rotor is proportional to the square of the linear speed. Therefore, the division by the linear speed reflects the difficulty of the rotor structure design. Some foreign scholars use the product of speed and power under the root sign to define high-speed motors. This division not only considers the difficulty of the rotor, but also considers the energy of the motor, which is more scientific and reasonable. According to this standard, high-speed motors can be defined into two categories: high-speed and ultra-high speed.
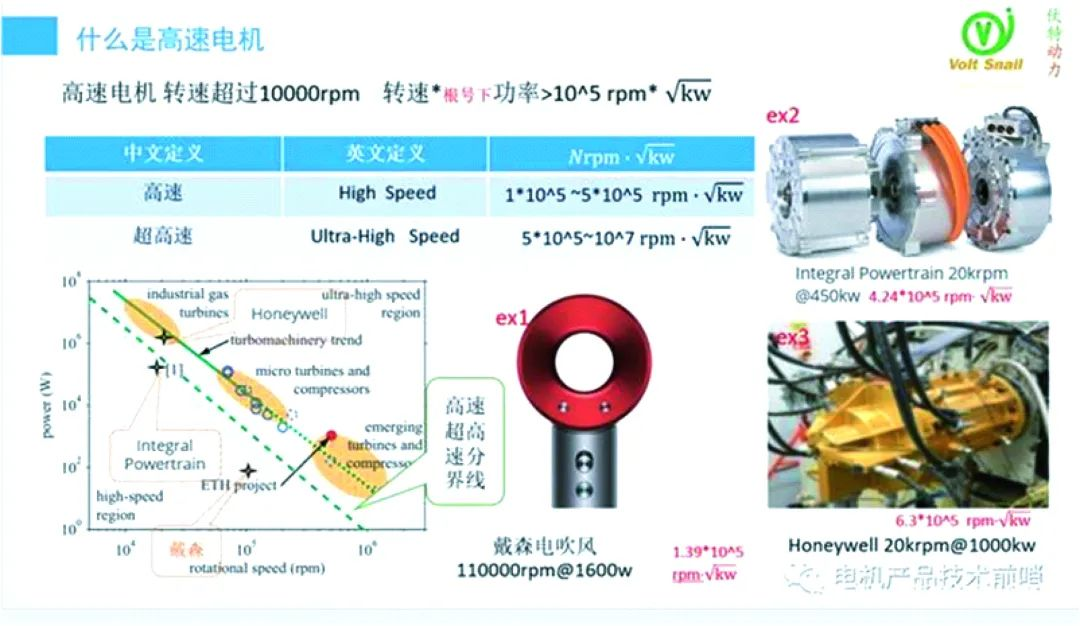
The difference between high-speed motors and ultra-high-speed motors lies in the product of power and speed. We use three cases to understand this concept:
Case 1 is the very famous Dyson hair dryer motor in small household appliances. This motor is 110 k r/min, 1 600 W. The product of its root power and rotational speed is 1.39×10 5 , as shown in the figure on the upper side , below the high-speed/ultra-high-speed dividing line, it is a high-speed motor;
Case 2 is a vehicle drive motor developed by Integral Powertrain Company, 20 k r/min , 450 kW. The product of power and speed under the root sign is 4.24×10 5 . The larger the product, the greater the high speed and the difficulty higher;
The third case is Honeywell's aircraft drive motor, 20 k r/min , 1 000 kW, the product of its power and speed under the root sign is 6.3×10 5 , which belongs to the scope of ultra-high-speed motors, and the technology used is more advanced.
In terms of high-speed operating point alone, the difficulty of the motor increases stepwise with the product of power and speed, so we can use this indicator to judge the degree of high-speed motor.
The application of high-speed motors is expanding in an explosive manner, and in order of high speed, there are the following applications.
The picture below is the electric transfer product of westwind company, 200 W, 300 kr/min, adopts the coreless PCB winding process, and integrates the control chip, the volume is very small, this electric transfer can also be used in dental and other medical equipment .
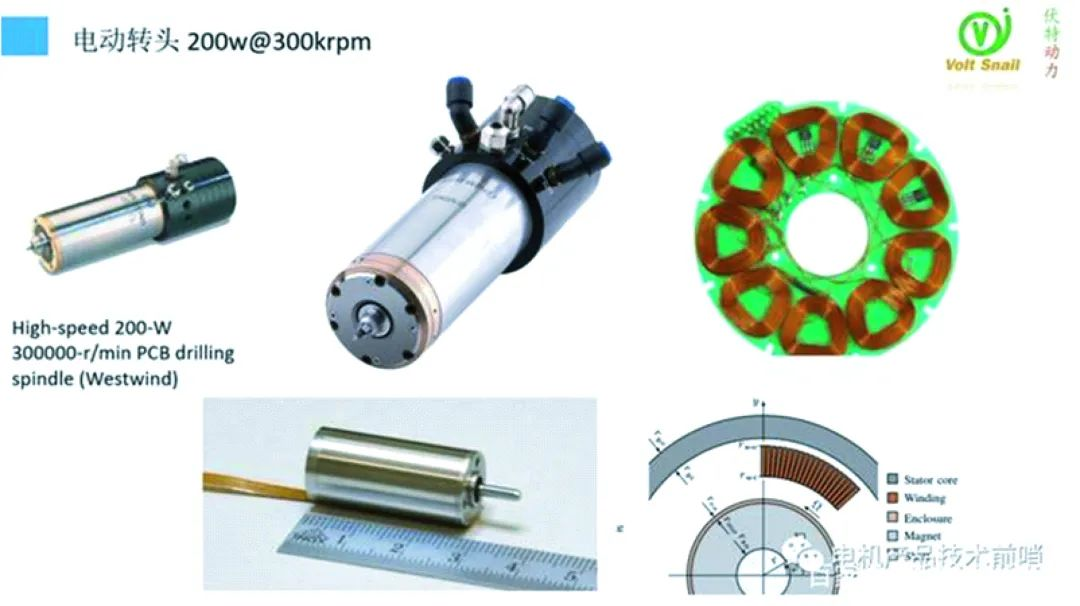
Molecular pump is a common physical device to obtain high vacuum, and it can also be used to separate air and obtain high clean air. The motor speed of this application can reach 32 kr/min, 500 W, and the scheme of induction motor can be used, and the scheme of concentrated winding permanent magnet motor can also be used to design.
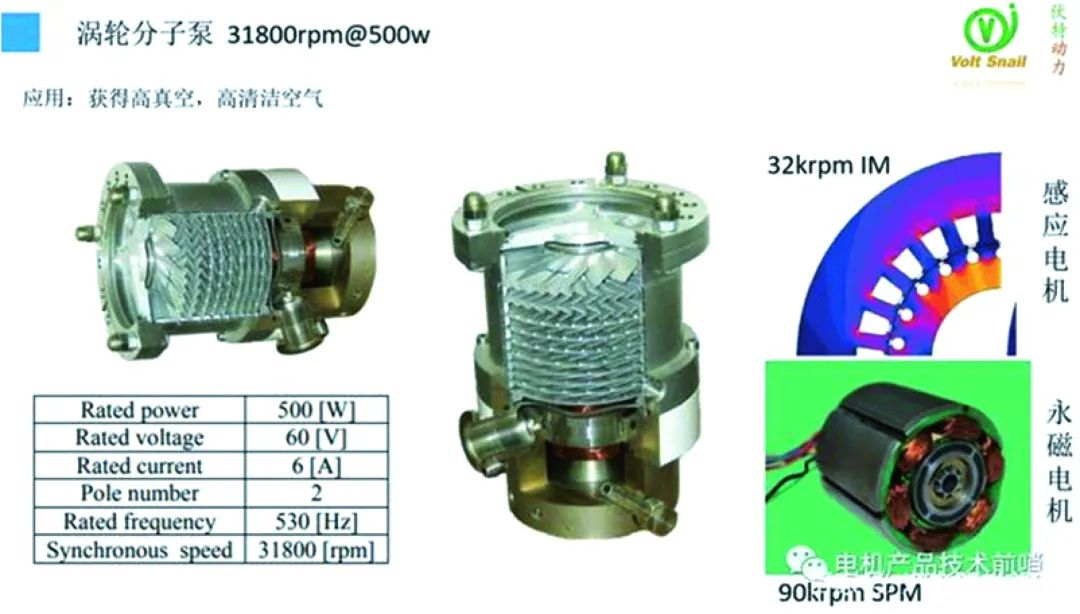
There are many subdivided fields of energy storage, such as flywheel energy storage used in aircraft and flywheel energy storage used in power stations. The following example is a flywheel energy storage product driven by a vehicle. Its concept is equivalent to battery energy storage for hybrid vehicles. Or supercapacitor energy storage, when the car needs explosive power, the flywheel energy storage motor can be used as a generator to supply electricity to the power supply. The following energy storage motor has a power of 30 kW and a speed of 50 kr/min. It adopts the scheme of an induction motor, and the rotor is a solid iron block.
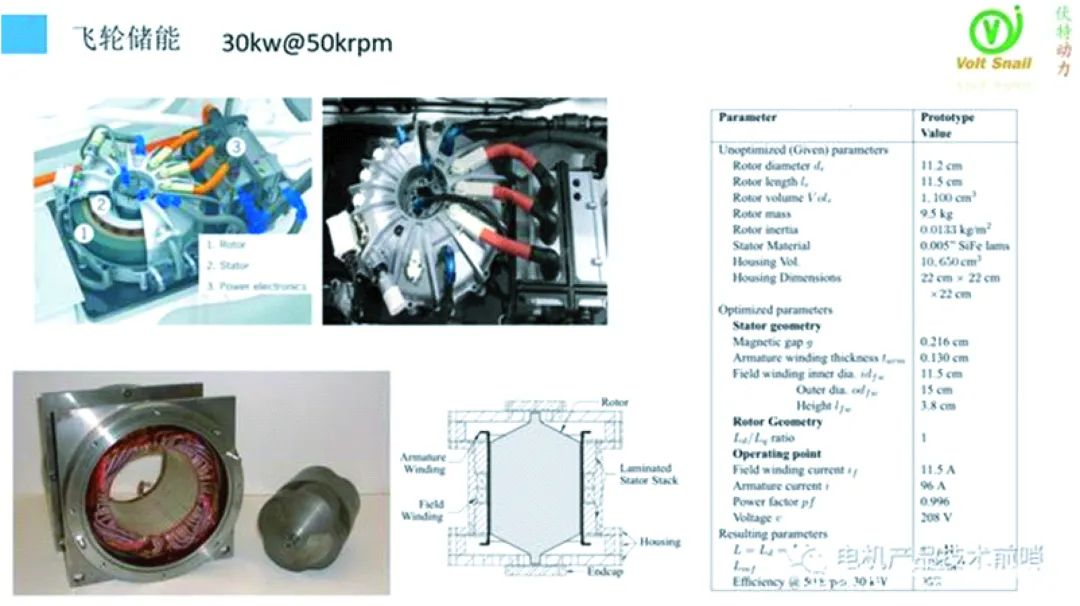
Electronic turbocharging is a new technology that has emerged in recent years. Its function is to supercharge the car engine at low speeds to slow down the vortex hysteresis and increase the explosive torque. The picture below shows a 10 kW, 100 kr/min product developed by BorgWarner. It adopts a permanent magnet motor structure with 2 poles and 24 slots. Because the working environment temperature is high, in addition to high speed, the design of this type of motor is also Magnetic steel loss and temperature rise need to be controlled.
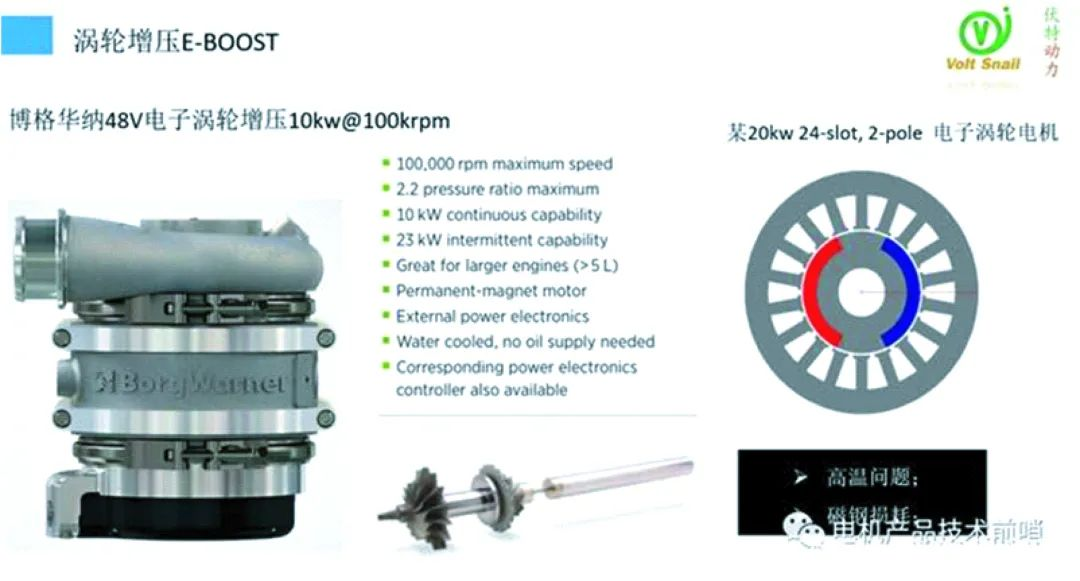
The micro gas turbine is definitely a legendary product. A pencil-long machine can generate 50 kW of power. It is said that it can reduce the volume of the engine by 95% when applied to a car. Many devices besides cars need this kind of small engine. . Its working principle is shown in the figure below, which requires a permanent magnet synchronous motor to convert the kinetic energy generated by combustion into electrical energy. This motor adopts a 2-pole 6-slot structure.
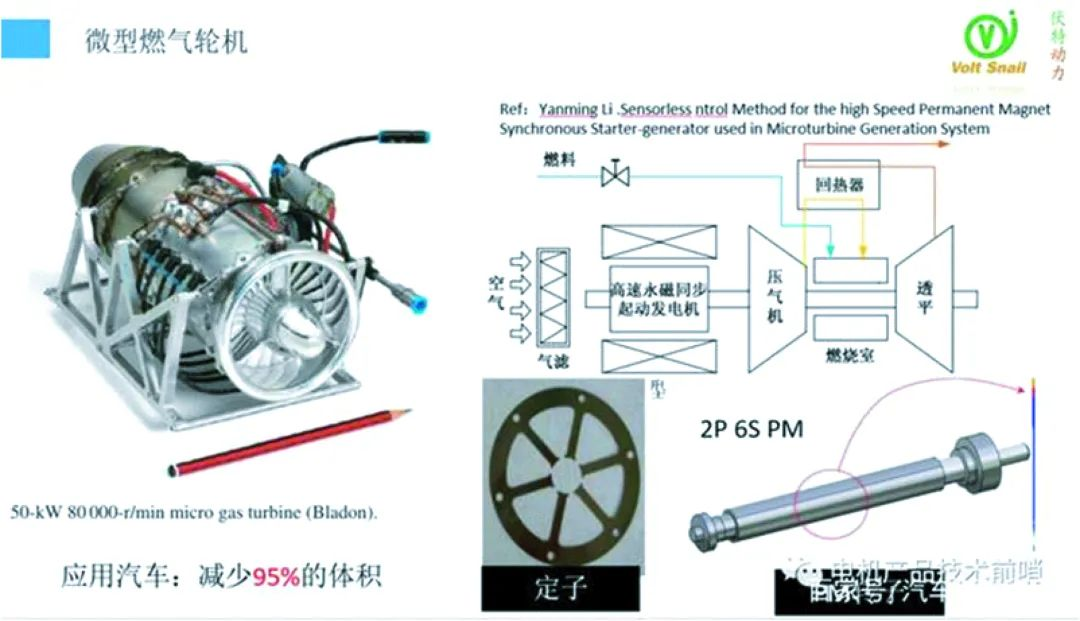
High-speed air compressor is currently the most common type of high-power high-speed motor, with a rotation speed of tens of thousands of rpm and a power between 100-700 kW. It generally uses magnetic bearings and drives turbines or blades through the motor to pressurize the air. The high-speed direct drive motor replaces the original low-speed motor + speed increaser system, which has the advantages of compact structure and high reliability. Two types of motors commonly used are surface-mounted permanent magnet synchronous motors and induction motors. The relevant manufacturers are shown in the figure below.
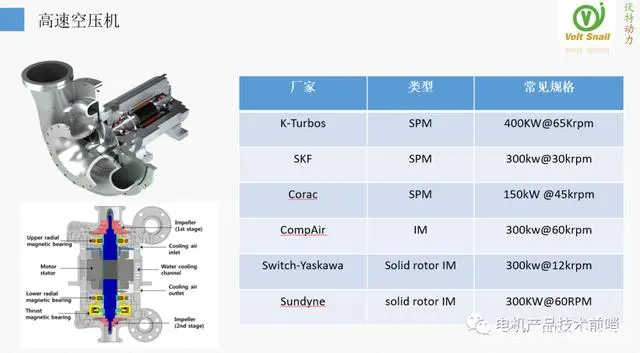
The centrifugal fan in the following case should also be regarded as a type of high-speed air compressor, using a 4-pole 24-slot SPM motor. The use of permanent magnet motors can improve efficiency and reduce size.
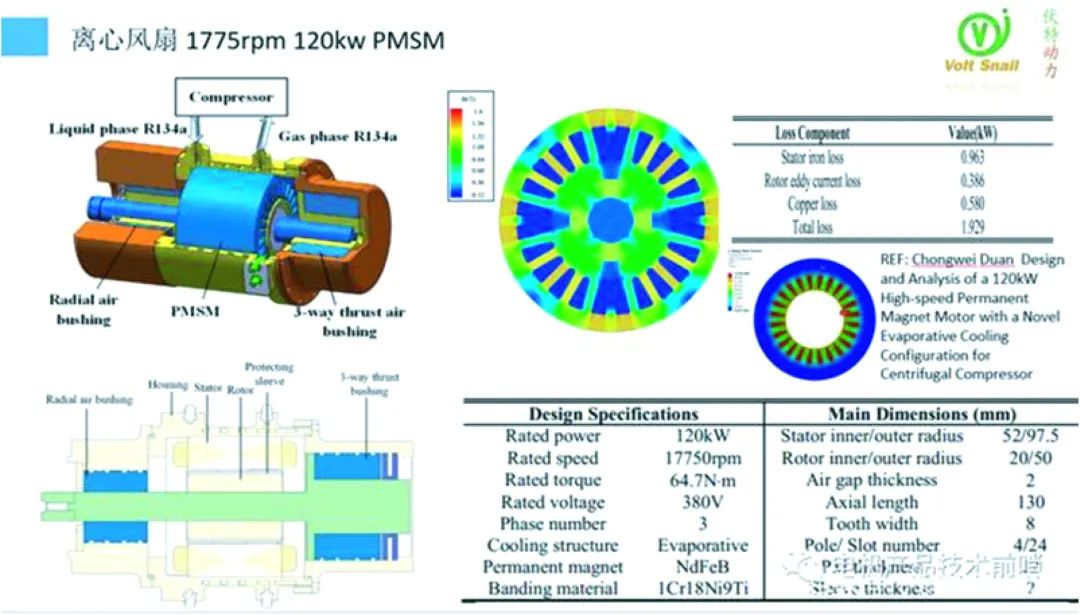
Vehicle drive motors are still the hottest field at present. The mainstream speed of passenger cars is within 16,000 r/min, and motors with higher speeds are being developed one after another. The figure below shows a 25,000 r/min, 225 kW induction motor developed by a certain company, with an outer diameter of 290 mm, a stack height of 230 mm, a maximum torque of 358 N m, and a water-cooled structure.
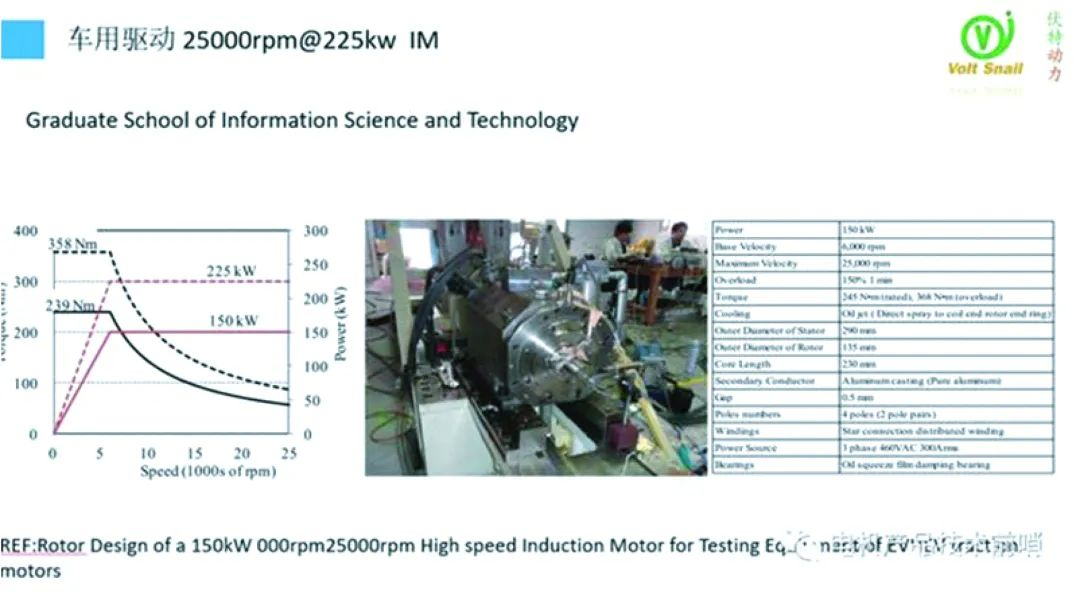
In order to improve the power density, the 20000 r/min, 450 kW permanent magnet motor system developed by Integral Powertrain has a maximum torque of 900 N m and a weight of only 28 kg. It adopts advanced winding oil injection cooling, and the stator radial Cooling, rotor axial cooling and a series of technologies. The controller matching it is a SiC platform.
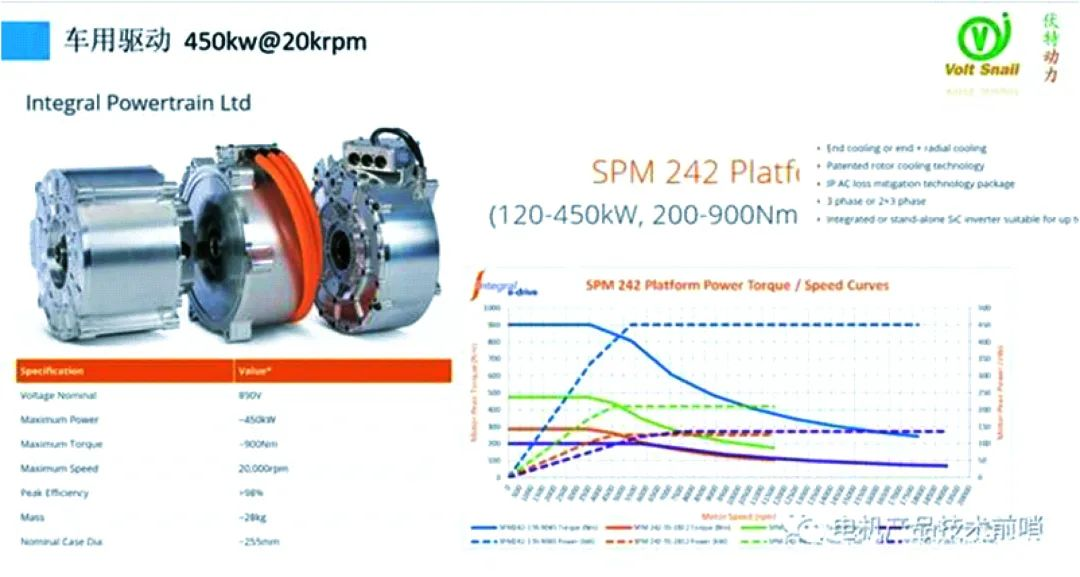
Coincidentally, AVL's next generation 20,000 r/min drive motor product also uses oil-cooled permanent magnet motor technology, with a motor power of 230kW and a corresponding weight of 45 kg.
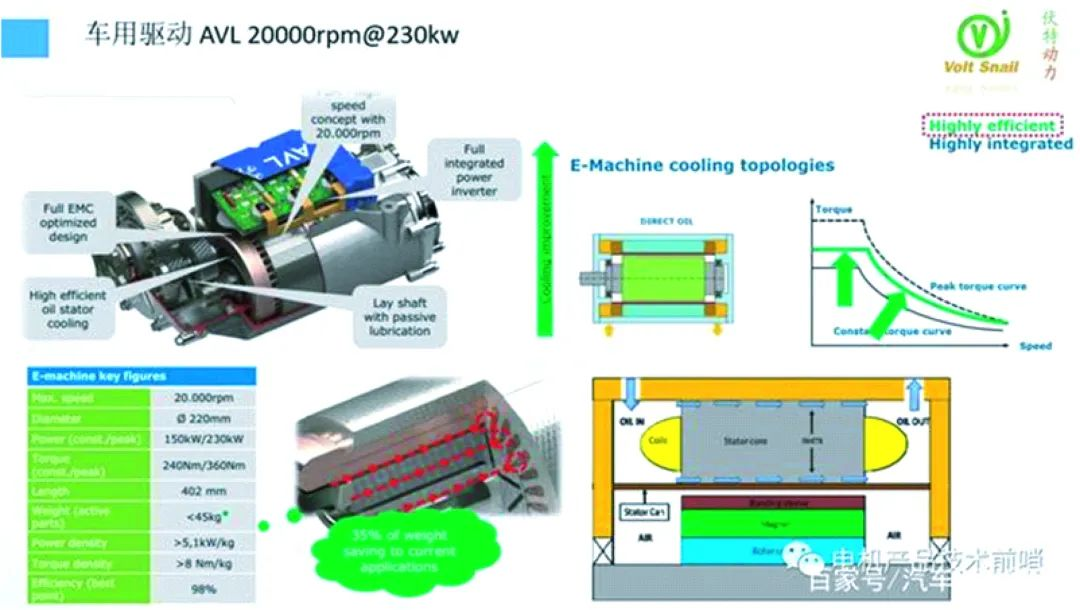
As the pace of aircraft electrification and semi-electricity accelerates, the demand for high-power and high-speed motors is also rising. The picture below is a 300 kW, 35 kr/min permanent magnet motor using a concentrated winding permanent magnet motor solution. The motor weighs 28.4 kg.
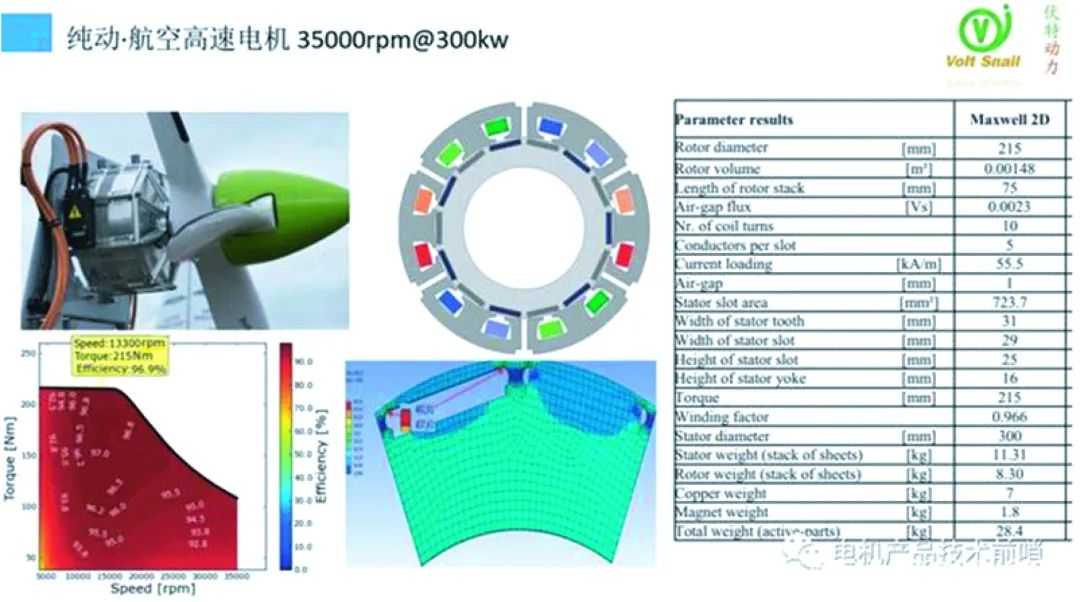
Higher power aviation motors are used in hybrid aircraft. As the core of similar extended-range hybrid architectures, these motors generally use forced air-cooling structures to take advantage of high-speed airflow. The power of Honeywell's motors can reach 1 MW. In order to improve efficiency Permanent magnet motors are used more than induction motors.
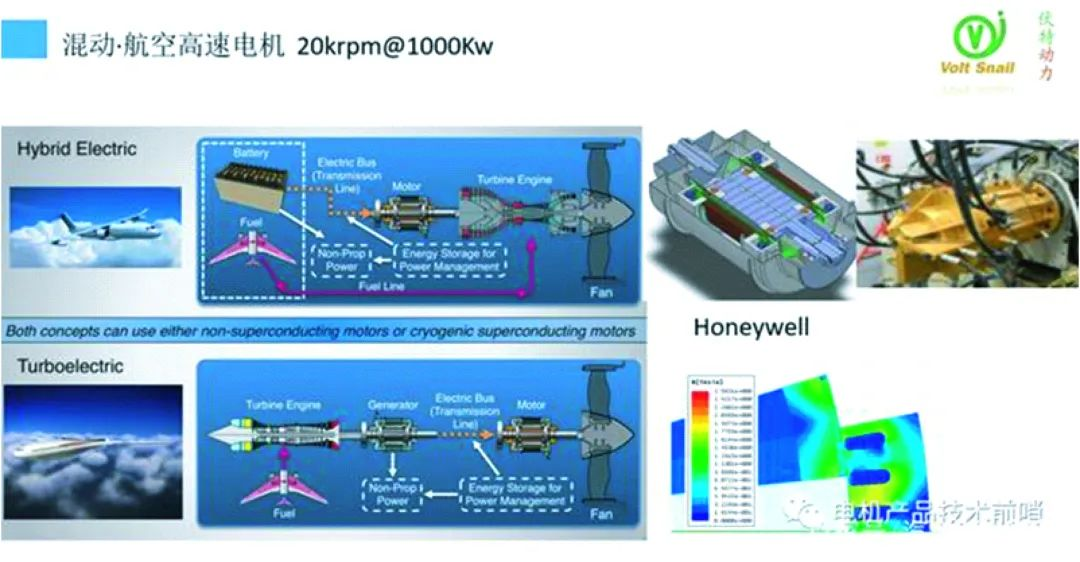
Information source: Xinda Motor