Motor product design takes a few steps, from "0-1" without worry
foreword
As an important module in the manufacturing industry, the design and manufacture of motors plays an important role in agricultural equipment, transportation and large industrial equipment. The task in the design process is clear. During product development, the first time is to thoroughly study the customer's technical requirements, DV/PV standards, especially product specifications and some performance parameters and corresponding operating conditions to carry out design calculations. Simply speaking, motor design generally includes the following process.
Communicate with customers to learn customer needs: including motor operating voltage, output power (speed torque), volume requirements (installation size), working system, and use environment. And determine the design requirements based on the potential needs of customers and the requirements of national standards. The design of new energy drive motors for vehicles has the characteristics of small reserved layout space and harsh working environment. Traditional steady-state motor design methods are difficult to meet the complex requirements of electric vehicle drive motors, and cannot well show the characteristics of electric vehicle drive motors.
According to the design input requirements, a preliminary model of the motor is initially established. After the requirements are initially met, a parametric model is established, and the model parameterization adjustment is carried out according to the following design principles.

Magnetic cloud map
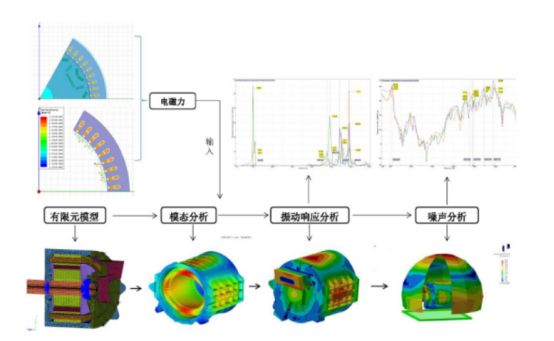
Electromagnetic vibration and noise simulation analysis process of motor
After the electromagnetic design meets the design requirements, start to determine the overall structure of the motor. Including motor protection type, bearing type and number, shaft extension type and number, installation method and cooling system, etc. Determine the structural type, shape and specific size of a certain component, and the materials used.
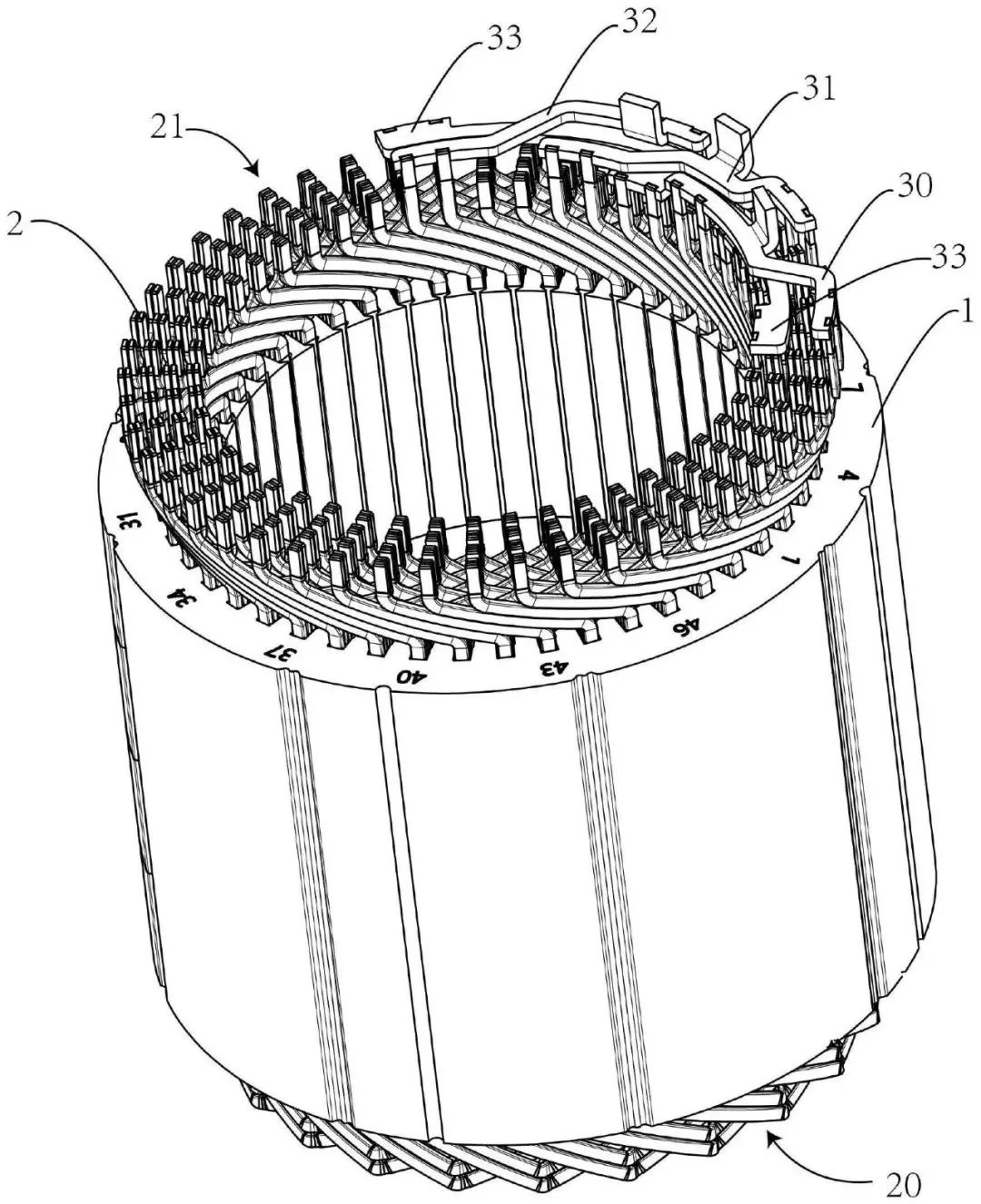
Flat wire stator structure design drawing
After the preliminary design of the motor is completed, it is necessary to formulate motor drawings with the manufacturer, that is, the selection of relevant materials, and feasibility analysis such as structural testing, heat dissipation and waterproofing, etc. to meet the requirements.
Finally, the design report and the motor stator and rotor size, winding diagram, motor material and other data are output.
The design requirements in the above link include the following aspects:
-
Design under electromagnetic, electrical, thermal and mechanical extreme operating conditions to meet changing performance requirements;
-
Motors typically operate over a wide torque-speed range;
-
Shorter development cycles are required in the face of increasingly fierce competition;
-
Realize highly optimized design scheme;
-
The motor has high efficiency, wide speed range, small size, light weight, high power density, low noise and low cost.
In order to complete tasks with high efficiency and low cost, in addition to the experience requirements of design engineers themselves, design tools also need to have:
-
Taking into account the theoretical depth of the magnetic circuit method and the high precision of the finite element method, it provides professional pre- and post-processing functions;
-
The coupling analysis of electromagnetic and thermal must be fast and efficient to meet the needs of the product development cycle;
-
The analysis of the mechanical strength of the motor needs to be carried out simultaneously in the electromagnetic design stage to reduce design iterations;
-
The integrated control algorithm realizes electromagnetic-thermal-mechanical fast coupling calculation in the full operating range.
In the early stage of the design of the drive motor body, the magnetic circuit analysis method is first used to reasonably analyze and calculate the precise variation range of the drive motor’s initial structural size, which provides an important prerequisite for reducing the calculation amount of the electromagnetic field finite element of the drive motor, improving the efficiency of the structure optimization design of the drive motor, shortening the prototype R&D cycle, and reducing production costs. As shown in the figure below, it is a pure electric vehicle drive motor structure design process.
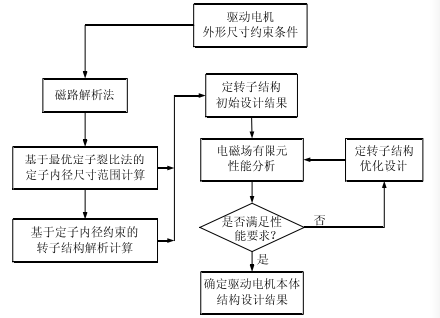
Motor Design Process
The next step is the simulation and optimization of the motor. For example, the mathematical model of the self-inductance and mutual inductance coefficient of the permanent magnet synchronous motor is established, and the internal mechanism of the two different magnetic field numerical calculation methods for the orthogonal axis inductance parameters is deeply analyzed, that is, the static state that ignores the cross-saturation effect Finite element method and frozen permeability method considering cross-saturation effects. The finite element calculation method of IPMSM with load starting for the rotor without cage damping guide is used to accurately calculate and analyze the load saturation magnetic field of the prototype. On this basis, two different finite element methods are used to calculate the working points of different loads Orthogonal axis inductance parameters, and the prototype orthogonal axis inductance parameters were measured experimentally by using the static AC experiment method. Through the comparison and analysis of the experimental test value and the two finite element calculation values, it was found that the static measured value of the prototype machine was the same as the static finite element that ignored the influence of cross saturation. The calculation results of the element are in good agreement, while the calculation results of the frozen permeability method considering the influence of cross saturation are closer to the orthogonal axis inductance parameter values at different load points of the prototype.
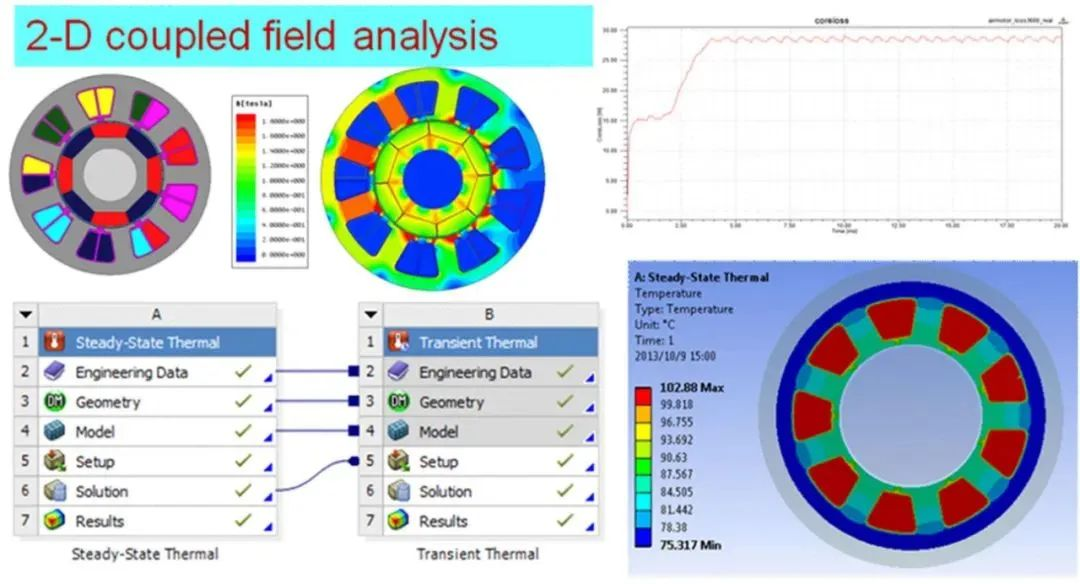
Coupling field analysis of motor simulation software
Summarize
The design of the drive motor is a very complicated process, and there are many factors to be considered. Here is just a general description of the design process. If you really want to design a motor yourself, you need to do more in-depth research. (Article source: Xinda Motor)