Two ways of braking the motor
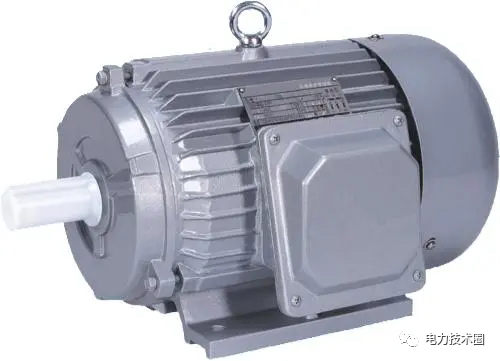
Motor braking is a problem often encountered in motor control. Generally, motor braking will appear in two different occasions. One is to achieve the purpose of rapid parking, and use various methods to make the rotation direction of the motor's rotating magnetic field and the rotation direction of the rotor On the contrary, an electromagnetic braking torque is generated to make the motor stop and rotate quickly; the other is that in some occasions, when the rotor speed exceeds the rotating magnetic field speed, the motor is also in a braking state. Motor braking methods are generally divided into: reverse braking, energy consumption braking ( DC braking ) and regenerative braking. The following is a brief introduction to the principles and precautions of these braking methods.
There are two types of motor braking:
1. Mechanical brake: After the power is cut off, the method of using a mechanical device to stop the motor quickly is called mechanical brake. There are two types of mechanical braking devices that are widely used: electromagnetic brakes and electromagnetic clutches.
2. Electric braking: After the motor is cut off from the power supply, it generates an electromagnetic torque (braking torque) that is opposite to the actual rotation direction of the motor, forcing the motor to stop quickly. The method is called electric braking. Commonly used electric braking methods include reverse connection braking and energy consumption braking.
The principle of electric braking is as follows:
1. Reverse connection braking is to reverse the power supply of the motor in motion to change the phase sequence in the motor stator winding, so that the rotating magnetic field of the stator winding is reversed, and the rotor stops quickly due to the braking torque opposite to the original rotation direction. change.
2. The so-called dynamic braking means that after the motor is separated from the three-phase power supply, a DC voltage is added to the stator winding, and a DC current is passed in to generate a static magnetic field, and the braking is achieved by using the rotor induced current and the static magnetic field. the goal of.
Reverse connection braking: After the motor is disconnected from the power supply, in order to stop the motor quickly, use the control method to add a power supply that is opposite to the normal operating power supply on the power supply of the motor. The rotation direction of the motor is opposite. At this time, the electromagnetic torque generated by the motor is the braking torque, which accelerates the deceleration of the motor. As shown in the figure below, use the switch Q to disconnect the voltage at both ends of the armature from the power grid, and immediately connect it to a braking resistor RL . At this time, the main magnetic field in the motor remains unchanged, and the armature continues to rotate due to inertia. The torque at this point is the braking torque, so the motor speed decreases until it stops.
The biggest disadvantage of reverse braking is: when the motor speed is 0 , if the reversed power supply is not removed in time, the motor will reverse.
There are two ways to solve this problem:
1. A time relay is added to the control circuit of the reverse phase power supply of the motor. When the reverse phase is braked for a period of time, the reversed phase power supply is cut off, so as to avoid the reverse rotation of the motor. But because the braking time of this method is difficult to estimate, the braking effect is not accurate.
2. Add a speed relay in the control loop of the motor's reverse-phase power supply. When the sensor detects that the motor speed is 0 , it will cut off the motor's reverse-phase power supply in time. Since the speed relay monitors the motor speed in real time in this method, the braking effect is much better than the previous method. It is precisely because of the characteristics of reverse braking that, for machines that do not allow reverse rotation, such as some lathes, the braking method cannot use reverse braking, but can only use energy-consuming braking or mechanical braking.
Dynamic braking: A direct current is passed through the stator winding to generate a constant magnetic field. At this time, the rotor cuts the magnetic force lines in the direction of rotation, thereby generating a braking torque. Because this braking method does not feed back the energy generated during braking to the power grid like regenerative braking, but relies solely on the motor to consume kinetic energy, it is called dynamic braking. And because the DC current is passed through the stator winding for braking, the dynamic braking is also called DC injection braking. As shown in the figure below, use the reverse switch Q to reverse the point voltage to the power grid. At this time, the armature current will be duplicated, and the current will be of the same magnitude, resulting in a large braking motor torque. stalled.
Dynamic braking is to rely solely on the motor to consume kinetic energy to achieve the purpose of parking, so the braking effect and accuracy are not ideal. In some occasions that require short braking time and good braking effect, this braking method is generally not used. Such as hoisting machinery, its operation is characterized by low motor speed, frequent start, stop, forward and reverse, and dragging the heavy objects to run. In order to achieve accurate and flexible control, the motor is often in a braking state, and requires a large braking torque. The energy consumption braking can not meet the above requirements. Therefore, hoisting machinery generally adopts reverse braking, and mechanical braking is required to prevent heavy objects from slipping during operation or when power is lost.
Regenerative braking: Regenerative braking is different from the above two braking methods. Regenerative braking is only a working state of the motor under special circumstances, and the above two methods are artificially imposed on the motor in order to achieve the purpose of rapid parking. The principle of regenerative braking: When the rotor speed of the motor exceeds the rotation speed of the synchronous magnetic field of the motor, the rotation direction of the electromagnetic torque generated by the rotor winding is opposite to the rotation direction of the rotor. At this time, the motor is in a braking state. The reason why the state at this time is called regenerative braking is because the motor is in the state of generating electricity at this time, that is, the kinetic energy of the motor is converted into electrical energy. At this time, certain measures can be taken to feed back the generated electric energy to the grid. To achieve the purpose of energy saving. Therefore, regenerative braking is also called generating braking.
Regenerative braking occurs in the following two situations:
1. When the weight of the crane is lowered, the rotor of the motor is under the manual action of the weight of the weight, and the speed of the rotor may exceed the synchronous speed. At this time, the motor is in the state of regenerative braking. At this time, the braking torque of the motor is to prevent the falling of the heavy object, until the braking torque is equal to the torque formed by gravity, the heavy object will stop falling.
2. When adjusting the speed by frequency conversion, when the frequency converter lowers the frequency, the synchronous speed also decreases accordingly. However, due to the effect of load inertia, the rotor speed will not decrease immediately. At this time, the motor will also be in the state of regenerative braking until the speed of the drag system also decreases.