It is difficult to inspect the defects of cast aluminum rotors of electric motors. In the actual production and processing process, it is necessary to rely on process parameters and experience to control and grasp, and some defects can only be found in the later test process. Today, Ms. will discuss with you about the shrinkage cavity and crack defects of cast aluminum rotors, and I am very willing to have good opinions and suggestions from you.Shrinkage cavity is a defect caused by extremely poor local feeding during the solidification process of cast aluminum rotors. Its shape is irregular, the hole is rough and uneven, and coarse grains can be seen visually. Small shrinkage cavities that are slightly dispersed are called shrinkage porosity. Shrinkage cavities often occur in the inner rings of the upper and lower end rings of cast aluminum rotors close to the iron core, and shrinkage cavities in the upper end rings are common.Causes of shrinkage and porosity●The temperature matching of aluminum water, mold and iron core is not suitable, and the purpose of sequential solidification and reasonable feeding cannot be achieved. The temperature of the upper mold is too low, the core preheating temperature is uneven, and the temperature difference is large, which are often the main reasons for the shrinkage cavity and porosity of the upper end ring.●The unreasonable mold structure, especially the too small section of the gate or the poor feeding of the diverter is also a reason for the shrinkage cavity and porosity of the upper end ring. Due to poor sealing of the mold or improper installation, aluminum leakage is caused, and the aluminum water at the gate is reduced, which will also cause shrinkage cavity or shrinkage porosity.●The speed of the centrifuge is low, and the pressure generated is too small.●Shrinkage cavity and porosity of the upper end ring of low-pressure cast aluminum often occur at the root of the fan blade, which is often caused by the temperature of the upper mold being too high, the preheating temperature of the iron core being too low or the inner gate being narrow.Measures to prevent shrinkage and porosity●Properly and reasonably grasp the preheating temperature of the mold and iron core, so that the molten aluminum can be solidified and fed sequentially.●Modify the mold, appropriately increase the cross-section of the inner gate, or reduce the height of the diverter to increase the feeding effect.● Properly increase the rotational speed of the centrifuge, and adopt a pouring method suitable for the rotor to be poured.●For low-pressure aluminum casting, the upper mold should be cooled in time; the iron core preheating temperature should be appropriately increased; the cross-section of the inner gate should be appropriately increased; and the solidification time should be prolonged.
Description of crack defects in aluminum casting process
Cast aluminum rotor cracks are mainly caused by the casting stress generated during the cooling process of the rotor, which exceeds the ultimate strength of the aluminum conductor at that time (referring to the moment when the crack occurs). Cast aluminum rotor cracks are mostly radial. There are hot cracks and cold cracks. Hot cracks are generated at high temperatures during the crystallization process. The surface of the crack opening is oxidized, and the shape is tortuous and irregular. Cold cracks are produced during the further cooling of solidified aluminum. The cracked surface is clean, smooth, and the color is the same as the cross section of aluminum at room temperature. Cold cracks are often continuous straight lines without crossing, and often appear on the surface.
●The impurity content in aluminum is unreasonable. Industrial pure aluminum often contains iron and silicon. These impurities affect the plasticity of aluminum. A large number of experimental analyzes have confirmed that the impurity ratio of silicon to iron has a great influence on cracks. When the ratio of silicon to iron is less than 1.5 or greater than 10, no cracks will appear. Cracks are prone to appear when the iron ratio is between 1.5 and 10. The research shows that the unreasonable content of Si/Fe is the main cause of cracks in the cast aluminum rotor, while the cast aluminum process parameters, the size and shape of the end ring and other factors only affect the transition zone.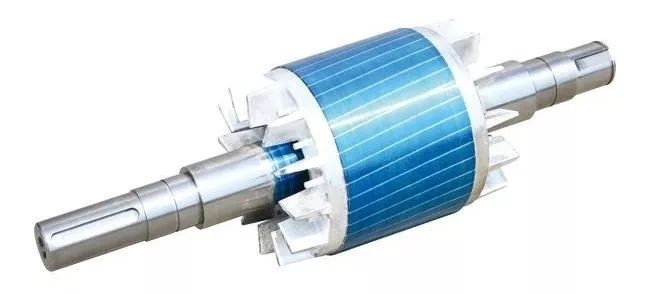
●If the temperature of aluminum water is too high, the crystal grains of aluminum will become thicker, and the elongation rate will be reduced, and cracks will form due to the inability to bear the contraction force generated during the condensation process. As the temperature of aluminum water increases, the solubility of gas increases, especially the incorporation of hydrogen, which accounts for about 60-90% of the total gas content in aluminum water. When aluminum water is poured into the mold and cooled, hydrogen will be precipitated to make the casting form needles. Pores seriously affect the strength of the casting, and cracks appear on the surface.
●Influence of rotor end ring size Unreasonable end ring size is one of the important factors for cracks (especially cold cracks). Generally, when the ratio of thickness to width of the end ring is less than 0.4, cracks are prone to occur.Cast aluminum crack control measures●Adjust the ratio of ferrosilicon content in aluminum, that is, Si/Fe≤1.5, or increase Si/Fe≥10, but it is better to reduce it. Because of the low silicon content, the casting performance is good and the cost is low. It is only necessary to add an appropriate amount of waste silicon steel sheets during production (preheat and dry before adding), but the amount of iron added should not be too much, otherwise it will reduce the conductivity of aluminum, increase the resistance of the rotor, and easily cause broken bars.●When designing the rotor end ring, the ratio of thickness to width should be greater than 0.4.●Strictly control the temperature of aluminum water, the maximum shall not exceed 780℃.