A comprehensive understanding of real production process of low-speed electric vehicles
For a long time, low-speed electric vehicles have been labeled as no standards, no technology, and small workshops. In order to understand the real production process of low-speed electric vehicles, we went into the production workshop of an electric vehicle plant to find out for you.
As we all know, vehicle production includes four major processes: stamping, welding, painting and assembly. We visited an EV plant's entire production process and first led everyone into the stamping workshop.
Stamping is the first step in all manufacturing processes. Here, pieces of steel plates will be stamped into parts with complex shapes and structures such as car doors, rear covers, and body sides. We saw rows of stacked molds, which are used to stamp different parts and need to be replaced frequently. The molds used by the EV plant can be shaped in one go, which greatly improves production efficiency compared to the multiple flanging and shaping procedures of traditional molds. Next to the stamping equipment, we saw about dozens of steel plates stacked on a trolley, and on the other side of the stamping equipment, the stamped body parts will be transported to the cutting production line.
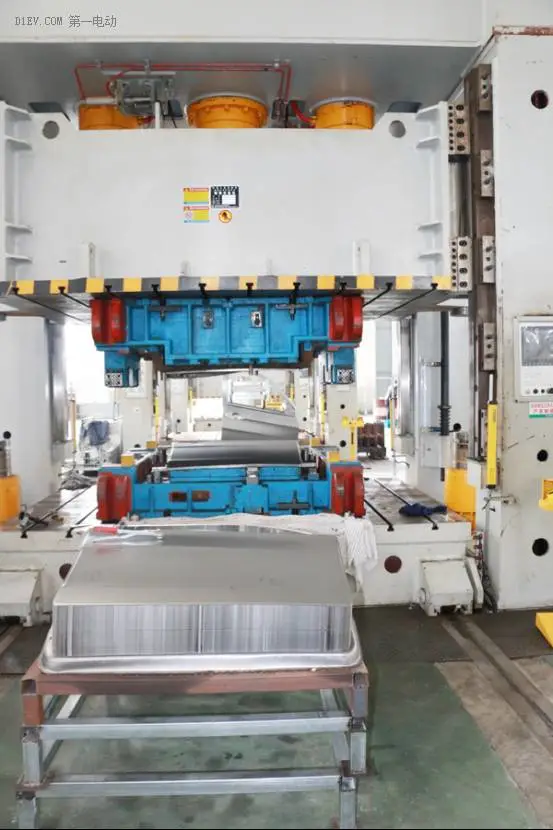
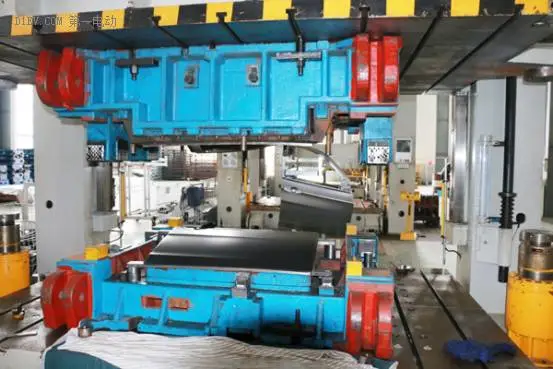
As an aside, I was a little surprised when I first entered the stamping workshop because there were few people walking around. I couldn't help but sigh, "It's so quiet." This was also the first time we walked into the production line of low-speed electric vehicles. Unlike the factory workshops that everyone imagines, there is no noise or banging here. It is as quiet as a university study room. All this is due to the low manpower and low noise brought by the mechanized production line. The highly automated production line also brings a lot of convenience to the update and iteration of Jiangsu Weilong's products. New products such as the 340SUV, 370SUV, 340 microcar, and 370 microcar that will be launched next year only need to replace the mold, and other production lines only need to be slightly adjusted to go into production.
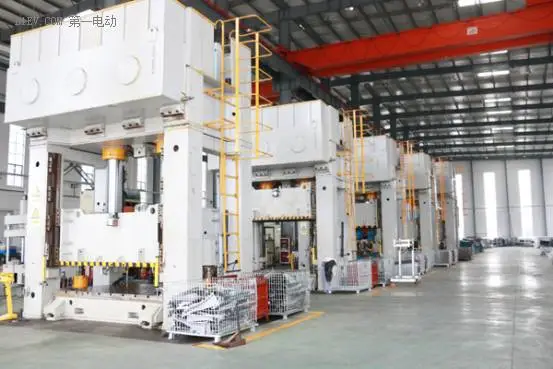
On the cutting production line, you can see Staubli's robotic arms flexibly performing cutting, punching and other processes. Even if you take photos very close to the robotic arms, it still feels very quiet. After the robotic arms stop working according to the process, the staff needs to replace the stamping parts with new ones for a new round of cutting. A female staff member was seen here. When asked if her work was tiring, she smiled and said that the robot had done most of the work, and she only needed to sort and classify the cut parts, which was very easy.
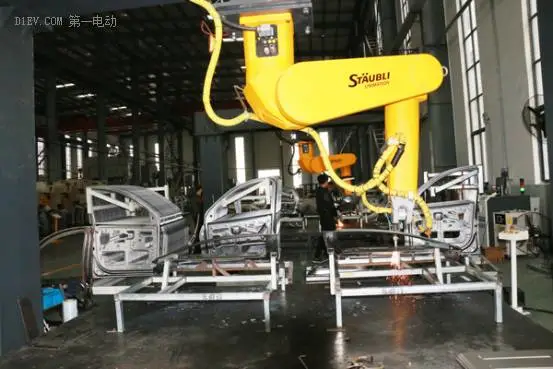
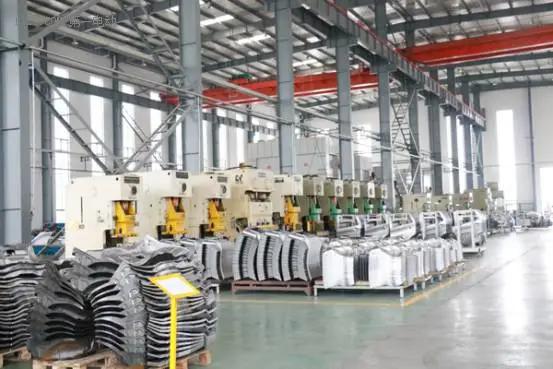
After walking out of the stamping workshop, you will enter the welding workshop, where parts of various shapes will be welded to form the basic body contour of the vehicle. Unlike the stamping workshop, the welding production line is colorful and has a visual impact. You can feel it for yourself by looking at the pictures.
Colorful welding line

KUKA Robot
On the welding production line, nine fully automatic German Kuka robots complete the welding mission. Because the robot arms are not competent in some parts, the body frames coming off the welding production line are transported to the brackets, waiting for the staff to further weld and perfect them.
Here we have to mention KUKA Robotics, which is the earliest robot company in Germany and one of the world's leading industrial robot manufacturers. Its users are as well-known as its reputation, such as General Motors, Chrysler, Ford, Porsche, BMW, Audi, Mercedes-Benz, Volkswagen, Ferrari, Harley-Davidson, FAW-Volkswagen and other automobile companies are all loyal users of KUKA Robotics.
Car body that needs further welding
Next, we will show you the third process of the four major processes - painting. In the painting workshop, the welded body frame is dressed in beautiful clothes, but if you think it is just sprayed with color directly, it is too young and too simple. Because the body frame needs to go through electrophoresis, baking paint, spraying and other processes to become what you want to see.
Car body in electrophoresis
Car body in electrophoresis
In the electrophoresis part, the car body needs to pass through more than a dozen swimming pools, and the negatively charged paint will be evenly attached to the car body. The car body that comes out of the swimming pool is military green. Although the car body after coming out of the swimming pool is not very good-looking, it has more functions such as anti-corrosion and anti-rust. On the paint line, we saw the staff applying yellow jelly on the welding parts. After asking the staff, we learned that this is sealant, which is to prevent rust at the seams. You see, in the invisible details, the staff on the production line are pursuing excellence in every step.
Workers apply sealant
Then it was the turn of the spraying robots. 14 automated robots were on standby to complete the painting work. In order to prevent the robots from being splashed, the staff considerately "fully armed" them. At first glance, they looked like a group of chemistry doctors and their original appearance was completely unrecognizable.
Spraying robot
Finally, we came to the assembly workshop, which was more like playing a jigsaw puzzle. The seats, steering wheels, wheels and other parts were installed here. However, everything was not that simple, especially the interweaving of various wires, which made people dizzy. From a high altitude, the car bodies looked like soldiers lined up waiting for inspection. When they arrived at the assembly workshop, it meant that they would soon be reborn from a pile of steel plates into electric cars!
The car body is equipped with simple interior and wiring
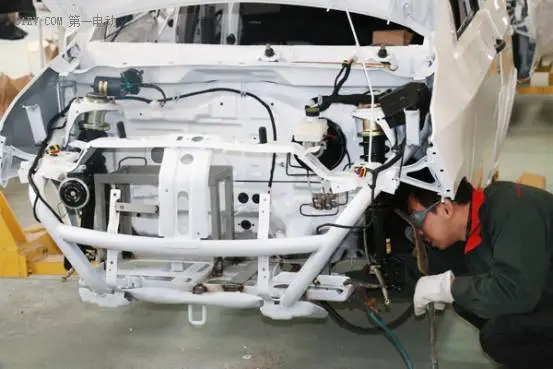
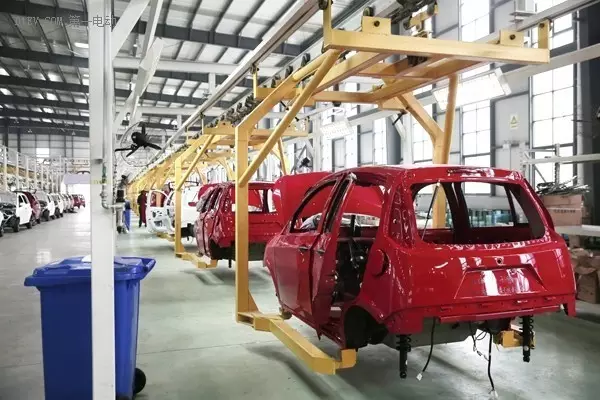
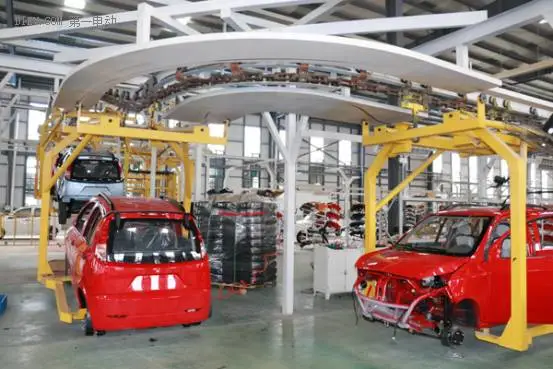
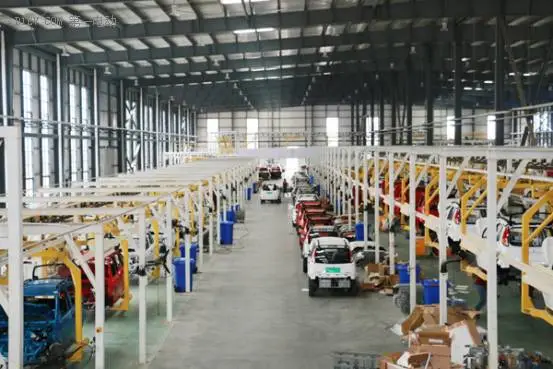
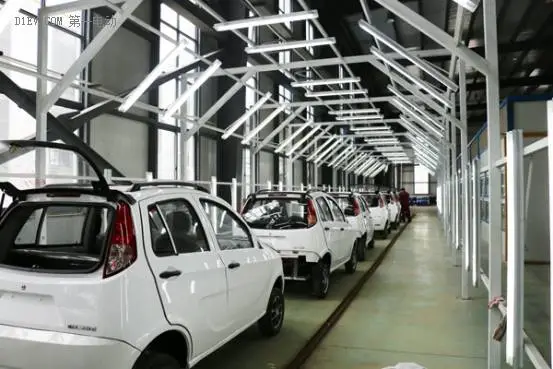
Walking through the production workshops one by one, we have a deeper understanding of the vehicles and are deeply impressed by the EV plant's spacious and bright production workshops, neat and orderly production processes, quiet environment, and careful control of details. I believe that everyone has a better understanding of the four major process production lines of low-speed electric vehicles. With these highly automated production technologies and processes, there is more confidence in the quality and production of low-speed electric vehicles.
This year, a series of policies on low-speed electric vehicles have been introduced, especially the National Standards Committee has officially approved the technical conditions for low-speed electric vehicles, granting the legal status of four-wheel national vehicles, and powerful companies have begun to practice in accordance with the direction of technical standards. However, this has also put low-speed electric vehicles at the forefront of the storm again. Faced with opportunities and challenges, where will low-speed electric vehicles go, and how will companies stand out?