How to protect motors from moisture in humid environments?
Date:2023-11-01 Author:Shandong Xinda Motor Co., Ltd.
1. Source of moisture
2. Hazards caused by moisture inside the motor
3. Waterproof measures for the shell of explosion-proof motors
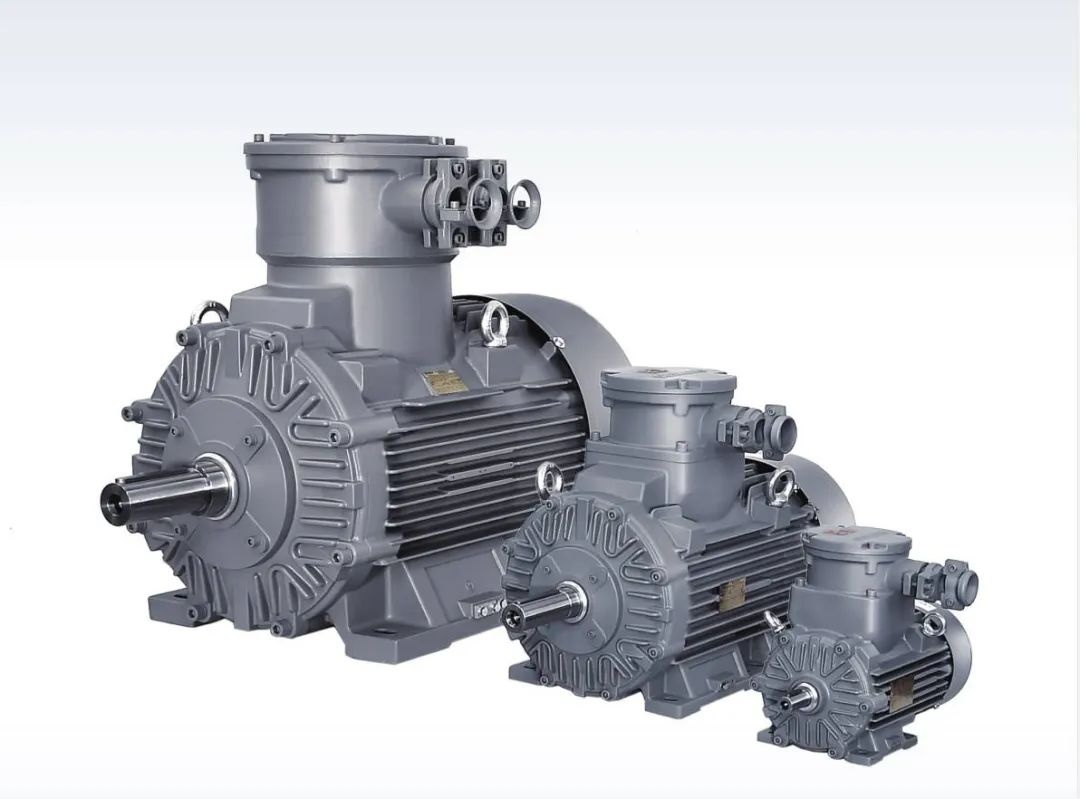