Comprehensive interpretation of high-efficiency motors
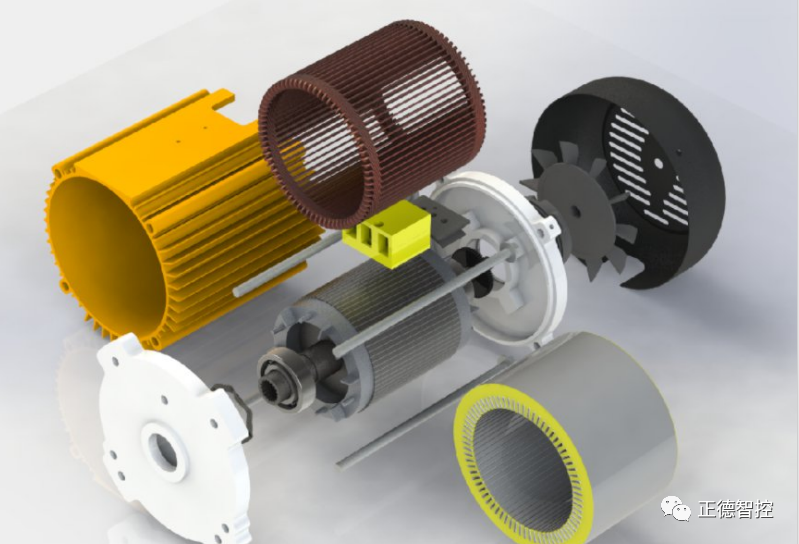
Main ways to improve efficiency
Add materials
The purpose of improving efficiency is to increase the outer diameter of the iron core, increase the length of the iron core, increase the size of the stator slot and increase the weight of the copper wire. For example: Y2-8024 motor increases the outer diameter from the current Φ120 to Φ130, and some abroad increase the outer diameter by Φ145, while increasing the length from 70 to 90. The amount of iron used in each motor increases by 3Kg and the copper wire increases by 0.9Kg.
Use silicon steel sheets with good magnetic permeability
Improve machining accuracy
Performance parameter optimization
Using cast copper rotor
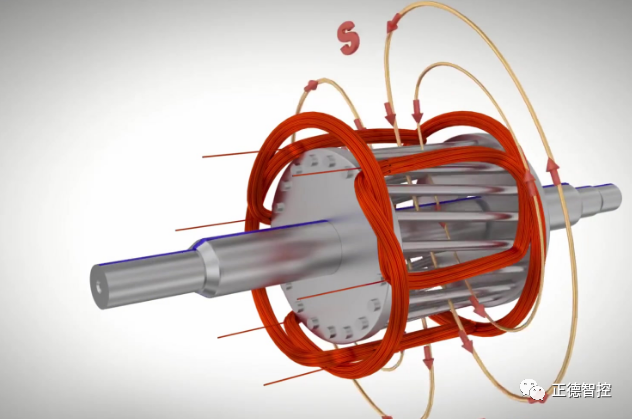
Energy saving measures
Motor energy saving is a systematic project involving the entire life cycle of the motor.
Design of energy-saving electric motors
Improve efficiency by looking at losses
While the motor converts electrical energy into mechanical energy, it also loses a part of its energy. Typical AC motor losses can generally be divided into three parts: fixed loss, variable loss and stray loss. Variable losses change with load and include stator resistance losses, rotor resistance losses and brush resistance losses; fixed losses have nothing to do with load and include core losses and mechanical losses. Iron loss is composed of hysteresis loss and eddy current loss, which is proportional to the square of the voltage, and hysteresis loss is also inversely proportional to frequency; other stray losses are mechanical losses and other losses, including friction losses of bearings and fans and rotors. etc. Windage losses due to rotation. You can start with losses to improve efficiency.
High efficiency motor features
Save energy and reduce long-term operating costs. It is very suitable for use in textiles, fans, water pumps, and compressors. The cost of motor purchase can be recovered by saving electricity in one year. Asynchronous motors can be fully replaced by direct startup or speed regulation with a frequency converter; rare earth permanent magnets The high-efficiency and energy-saving motor itself can save more than 15% of electric energy than ordinary motors; the power factor of the motor is close to 1, which improves the quality factor of the power grid without adding a power factor compensator; the motor current is small, saving power transmission and distribution capacity and extending the overall operating life of the system; starting from the power saving budget Look, taking a 55-kilowatt motor as an example, a high-efficiency motor saves 15% more electricity than a normal motor. The electricity cost is calculated at 0.5 yuan per kilowatt hour. If you use an energy-saving motor, you can recoup the cost of replacing the motor by saving electricity within one year.
Advantages of high-efficiency motors
Direct start, can fully replace the asynchronous motor; the rare earth permanent magnet high-efficiency energy-saving motor itself can save more than 3% of electric energy than ordinary motors; the motor power factor is generally higher than 0.9, improving the quality factor of the power grid without adding a power factor compensator; the motor current is small, saving money transmission and distribution capacity, extending the overall operating life of the system; adding a driver can achieve soft start, soft stop, and stepless speed regulation, further improving the power saving effect.