Discussion on process measures to reduce motor noise
The noise generated by electrical equipment varies in size and model due to different sizes and models of the equipment . Motor noise is mainly divided into two categories, one is the noise generated by electromagnetic equipment, and the other is the noise generated by motor mechanical equipment.
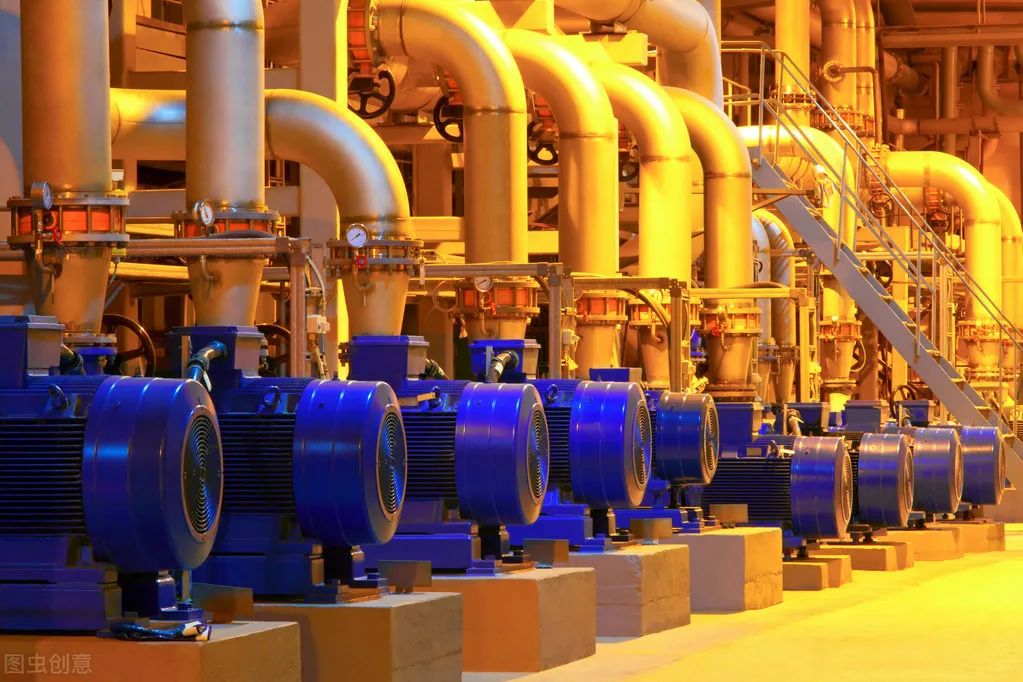
There are many reasons for the noise generated by mechanical equipment. Most of them are caused by the wear and tear of motor equipment during normal production. There are also many abnormal noises caused by operator misoperation or hidden faults in motor equipment. Therefore, as a motor technician, you should conduct investigations from many aspects to find out the causes of motor noise, and use effective process measures to effectively eliminate the noise so that motor noise exists in its normal form.
1 The main causes of motor noise in daily production
1.1 Noise caused by unbalanced internal components of motor equipment
Noise produced by motor equipment used in daily production is usually caused by imbalance of mechanical equipment. There are three main types of imbalances in electrical equipment: dynamic imbalance, static imbalance, and mixed imbalance. Dynamic unbalance will cause centrifugal force, causing noise to vibrate against each other on the supports. The greater the noise in production, the more violent the vibration. In addition, the construction and later maintenance of electrical equipment are not paid attention to, and the noise of many electrical equipment will become louder and louder. Static unbalance is mainly due to the size of the centrifugal force. Caused by phase vibration imbalance. Mixed unbalance is generally used in large motor companies, and decision makers generally only pay attention to the role of dynamic balancing in the production process.
1.2 Noise caused by motor bearing wear
As one of the main components of motor equipment, the overall noise generated by bearings can be summarized into body noise and noise generated by motor matching components. Most of the noise generated by the motor body occurs on rolling bearings and rolling balls. These rolling bearings have shaft rings inside and outside, including ball necklaces, to ensure that the motor equipment can roll smoothly during work without causing huge noise due to friction or installation. In addition, in modern bearing production They will all be equipped with noise measuring instruments and effective noise reduction instruments, which also occupy a majority of positions in the production of motor factories;
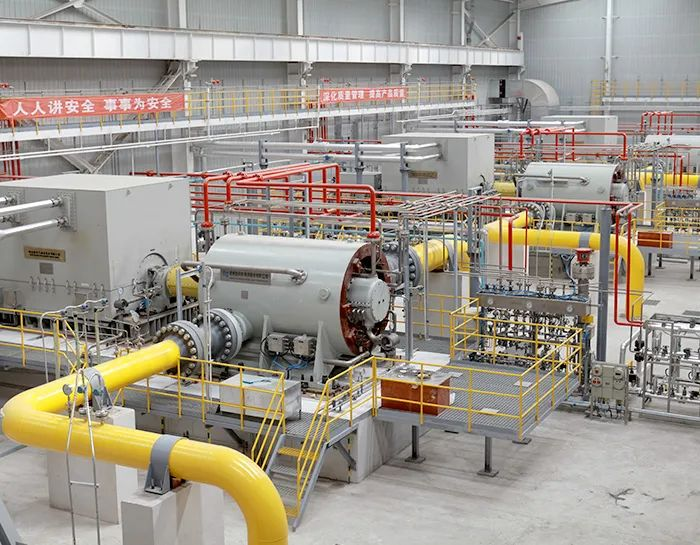
Since the noise generated by motor components is usually considered to be appropriate for most motor manufacturers, the corresponding size of the bearing is used. After conducting a noise decibel test, the noise emitted by the bearing is the largest. There are two reasons for this:
( 1) The gaps between the bearings are small and the original manufacturing methods of the bearings cannot be matched. As a result, there is a gap between the inner ring and the outer ring after the bearings are installed in the motor. Long-term use will cause the bearings to deform, cause friction and generate noise. .
(2) Inappropriate stiffness of the motor end cover and frame produces noise. Due to the elliptical deformation of the bearing inner ring assembled on the rotating shaft, the radial weakening of the vibration system of the bearing and the motor causes "tuning", thus causing axial vibration with a large amplitude. It is worth noting that the electromagnetic force waves that cause electromagnetic vibration of the stator core also act on the rotor. Under normal circumstances, if the rotor stiffness is good, the bending vibration caused by it can be ignored, but it will be transmitted to the end cover and the entire motor through the bearing.
1.3 Motor noise caused by many reasons
There is another reason for the noise. For example: Under normal circumstances, mechanical noise is the main source of motor noise. Normally, due to the need for heat dissipation, the sealing performance of the motor is limited. As a result, after long-term operation, the amount of adsorbed dust will continue to increase, affecting the heat dissipation of the motor. The thermal stress generated during operation can easily cause shaft bending and displacement, and the shaft Thermal bending and thermal displacement will increase the noise of the motor.
2 Process measures to reduce motor noise
2.1 Solve the mechanical imbalance of the rotor to effectively control noise
The unbalance of the rotor should be minimized as much as possible, otherwise the balance accuracy will be low.
The balance accuracy is related to the specifications, properties and usage conditions of the motor. For example: marine motors have large bumps, long running time, small vibration and noise, and high balance accuracy requirements. The greater the ratio between the diameter and length of the rotor core, the greater the centrifugal force and the higher the balance accuracy.
The higher the rotor speed, the higher the balance accuracy requirements. The basic conditions of the motor during use, such as poor rigidity of the bearings and supporting parts, require high balance accuracy.
2.2 Main methods of reducing noise of motor bearings
The specific methods for reducing bearing noise in motor equipment can start from the following points:
(1) Pay attention to the selection of bearings. During the operation of most motor bearings, the vibration level of the bearing will increase as the inner diameter of the bearing increases. For every 5mm increase in diameter, the vibration increases by about 1 to 2dB.
(2) Pay attention to the size of the bearing radial clearance. Excessive radial clearance will cause low-frequency noise to increase, and conversely, too small a clearance will cause high-frequency noise to increase. In order to reduce vibration and noise when the bearing rotates, the radial working clearance of the bearing should be controlled within the range of 1 to 9 μm.
(3) Appropriately pressurize the bearings. Its purpose is to eliminate the axial clearance of the rotor. Generally, wave spring washers or three-point elastic washers can be used and placed at the shaft extension end.
(4) For motors with relatively high noise requirements, low-noise bearings must be selected. When the load is small, oil-impregnated sliding bearings can be used, and their noise is generally about 10dB smaller than rolling bearings of the same size.
(5) The same motor should be assembled with bearings of the same batch, specifications and models produced by the same manufacturer to avoid mixed installation.
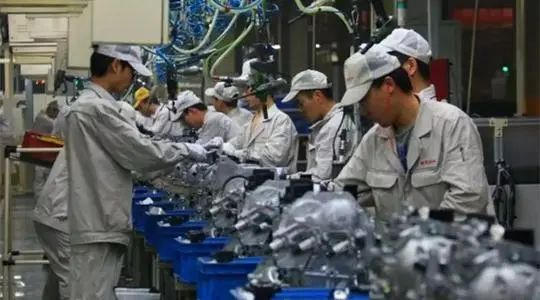
2.3 Other noise reduction methods
There are many methods for noise reduction technology of motor equipment, among which two points are given as examples:
(1) The bearing shaft configuration should avoid noise caused by repeated knocking of the bearing. Before assembling the bearing, the bearing should be cleaned and demagnetized. The thermal expansion method should be used during assembly, and an appropriate amount of corresponding type of grease should be applied.
(2) The stator, rotor and bearings are responsible for preventing noise
Establish quality control points, implement key controls, and ensure that the processing accuracy is as close to the middle value of the tolerance zone as possible; at the same time, the production company's technological level, production equipment and tooling must be able to ensure the accuracy of mechanical processing. To improve the quality of mechanical processing, there must be absolute guarantees in the establishment of quality control points and detection methods.