Let’s talk about mainstream insulation materials for motors
As we all know, any live equipment or machine is most afraid of leakage and short circuit.
The so-called "a layman looks at the excitement, and an insider looks at the doorway", the doorway of the insulation structure and system has always been a key topic of continuous discussion and research within major OEMs.
Today we will take a look at the application status of the main insulation materials used in new energy vehicle drive motors from beginning to end.
01Insulation system
Typical insulation solutions for current drive motors can generally be divided into primary insulation and secondary insulation, as shown in the figure below.
Main insulation is crucial to the safe operation of the motor, including electromagnetic wire insulation, slot insulation, phase insulation, slot wedge insulation, impregnating paint, etc.;
The secondary insulation mainly serves as an auxiliary insulation effect, and at the same time provides mechanical support and protection for the coil, including insulating sleeves, tying ropes, busbar insulation and solder joint coating, etc.
02Corona-resistant enameled wire
The drive motors are turning faster and faster, and the power density of the electric drive system is getting higher and higher. The performance and quality requirements of enameled wires are bound to become more and more stringent.
The paint film of this enameled wire developed from the early three-coat layer to the later two-coat layer. Due to the short life of the three-coat layer and the relatively poor adhesion of the paint film, it gradually cannot keep up with the requirements.
In 2000, DuPont developed a two-coat corona-resistant enameled wire. The bottom coating is a nanoparticle-modified polyesterimide corona-resistant coating, and the top coating is a PAI coating.
Since its introduction, the secondary coating has been widely used in the field of drive motors. In recent years, with the rise of oil-cooled motors, PAI single-coated corona-resistant enameled wire has become more and more widely used due to its resistance to ATF oil and high temperature.
Corona resistant enameled flat copper wire
And we all know that what materials and technologies to choose are constantly changing according to the technology of the application subject, and no material is a panacea.
03Insulating impregnated resin
Motor stator insulation treatment mainly adopts vacuum impregnation resin (VI) and vacuum pressure impregnation resin (VPI). Generally speaking, the matrix resin is modified polyester or polyesterimide with high strength and high heat resistance.
It is worth mentioning that the nano-particle modification technology, by adding nano-inorganic particles, can improve the painting efficiency, heat resistance and corona resistance.
Speaking of the status quo, in recent years, resins suitable for new processes such as winding energized heating curing, ultraviolet curing, and rotary drip immersion have also entered people's field of vision.
Among them, the electric heating process is a new method with high efficiency. It only takes a few minutes from impregnation to resin gel, and the whole process can be completed in about one hour. Moreover, the amount of hanging paint can be precisely controlled, the filling performance is good, and no resin curing waste residue is produced.
However, the main equipment of the electric heating process is still controlled by foreign companies in Germany and Italy, and the import price is relatively high. At present, there is no large-scale expansion in China.
04 soft composite material
At present, the mainstream non-oil-cooled drive motor slot insulation, slot wedge, and interphase insulation mainly use two layers of polyaramid fiber paper (such as Nomex) and a layer of PI film to form a soft composite material.
This kind of insulating material has H-class heat resistance and lower cost, so it has been widely used. However, its corona resistance and ATF oil resistance are slightly worse.
With the popularization of oil-cooled motors, such soft materials that are not resistant to oil are beginning to fail, and are prone to delamination, thereby reducing insulation performance.
This has brought about a "vicious circle": In order to improve the oil resistance performance, the motor development and design will use single-layer thick polyaramid fiber paper with better oil resistance;
However, the electrical performance of this material is relatively poor. In order to improve the insulation performance, the design thickness of the material must be increased. Increasing the thickness will inevitably affect the power density, thereby increasing the manufacturing cost of the entire motor.
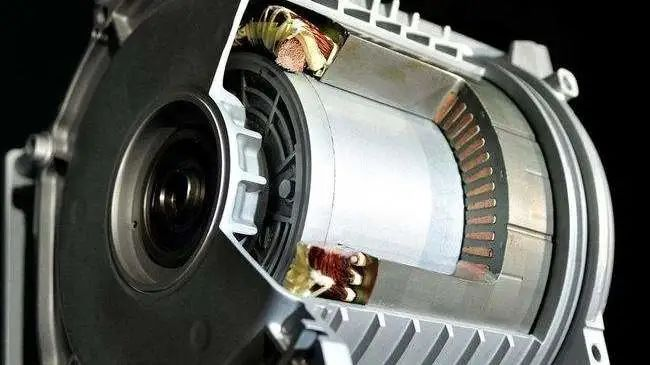