Where is the difficulty in motor calibration? chatgpt answer
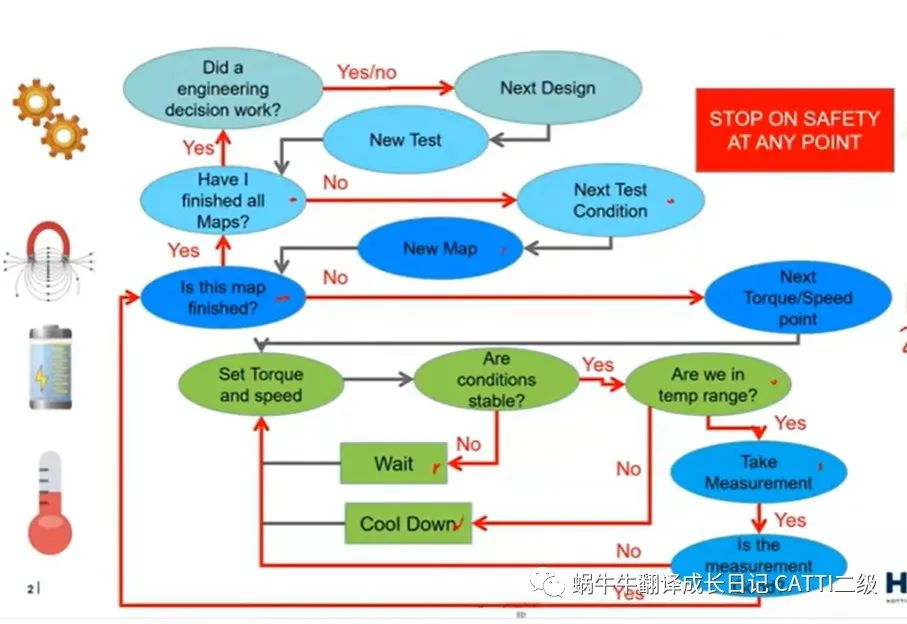
1. What parameters are usually involved in motor calibration ?
The parameters involved in calibrating a motor vary depending on the specific motor type, vehicle system, and manufacturer. However, common parameters for calibration include:
Torque Control : Adjust the torque output of the motor to ensure that it meets the expected performance and efficiency requirements.
Current and Voltage Limits : Set the motor current and voltage limits to prevent overloading or overheating .
Speed Control: Adjust the speed control of the motor to achieve the desired acceleration and deceleration characteristics.
Regenerative Braking : Configure the behavior of the motor during regenerative braking, where the motor acts as a generator and recovers energy during deceleration .
Thermal Management: Monitor motor temperature to prevent overheating from affecting performance and longevity .
PID Control Parameters: Adjust the proportional - positive integral - inverse (PID) control parameters to fine-tune the motor's response to different driving conditions.
Sensor Calibration : Calibrate sensors such as encoders , Hall effect sensors , or position sensors to accurately measure motor speed and position .
Efficiency Optimization : optimize motor operation to achieve maximum efficiency at different load conditions .
Start -Up and Stop Behavior : Defines how the motor starts and stops, ensuring smooth, controlled transitions .
Noise and Vibration Reduction :Modify the control parameters to minimize the noise and vibration generated by the motor.
Diagnostic and Error Handling:Configure diagnostic parameters to detect failures, errors, and abnormal health conditions.
It is worth noting that the calibration process can be complex and requires expertise , as improper calibration can lead to poor performance, safety issues or damage to motors and vehicle components. Be sure to refer to the manufacturer's guidelines and work with a professional experienced in motor calibration.
2. What components are usually involved ?
When calibrating an automotive motor, various components are often involved to ensure the motor's optimum performance and integration with the vehicle's systems. These components include :
Motor Controller : An electronic device responsible for controlling the operation of a motor, including adjusting speed, torque, and other parameters .
Sensors : Various sensors are used to provide feedback on motor speed, position, temperature, and other related variables . These sensors help to adjust the characteristics of the motor during the calibration process .
Inverters : Inverters convert the DC power in the car's battery into AC power that drives the electric motor . They play a vital role in controlling the speed and torque of the electric motor.
Battery Management System (BMS : Battery Management System ) : For electric vehicles, the BMS monitors and manages the state of charge, voltage and temperature of the battery, thereby affecting the performance of the motor.
Thermal Management System : The motor generates heat during operation. Proper thermal management components such as cooling systems or heat sinks can help keep motor temperatures within safe limits.
Communication Interfaces : Interfaces such as CAN or LIN facilitate communication between different vehicle systems and components to communicate calibration adjustments to the motor controller.
Software and Firmware: The software and firmware of the motor controller contain the control algorithms and logic that determine the behavior of the motor. Calibration is usually achieved by adjusting software parameters.
Diagnostic Tools : Professional diagnostic tools and equipment allow technicians to monitor motor performance, read sensor data, and make real-time adjustments during calibration.
Data Logging Systems : These systems record performance data , allowing engineers to analyze the behavior of the motor and make informed decisions during the calibration process.
Mechanical Components : The physical components of the motor, such as the rotor , stator , and gearbox ( if present ) , may also require tuning or calibration to optimize overall performance .
It's worth noting that the exact components involved will vary depending on the vehicle architecture, motor type, and manufacturer's design. Proper calibration requires an understanding of these components and their interactions, often involving collaboration between mechanical, electrical, and software engineering teams.
3. What tools are usually used ?
Calibrating an automotive motor requires the use of specialized tools and equipment to fine-tune various parameters to ensure optimal performance. Some commonly used motor calibration tools include:
Motor Controller Programming Interface : Through this tool, technicians can access the software and firmware of the motor controller to adjust control parameters and calibration .
Diagnostic Scanners : These tools interface with the vehicle's on-board diagnostic system to read sensor data, identify faults, and make real-time adjustments during the calibration process .
CAN Bus Analyzers : These devices help monitor and analyze communications on the Controller Area Network ( CAN ) bus , which is used for inter-component communication within a vehicle .
Oscilloscopes: Can measure and display electrical signals, which can help analyze motor performance, sensor output and signal integrity.
Data Loggers : These devices record performance data over a period of time, allowing engineers to analyze motor behavior, diagnose problems, and fine- tune parameters.
Power Analyzers : Power analyzers measure electrical parameters such as voltage, current, and power consumption to help optimize energy efficiency and performance.
Thermal Imaging Cameras : These cameras help visualize heat distribution , identify potential overheating issues, and assist in thermal management calibration .
Torque Sensors: Torque sensors measure the output torque of the motor and are essential for calibrating the torque control algorithm.
Load Banks: The load banks simulate the actual load on the motor, which can be tested and calibrated under different load conditions.
Signal Generators : Signal generators generate specific electrical signals for simulating various motor operating conditions during calibration .
Multimeters : Multimeters measure voltage, current , and resistance, providing necessary electrical readings for calibration and diagnostics .
Software Tools: Special software tools provided by motor manufacturers or third-party suppliers are used to connect with the motor controller and adjust software parameters.
Mechanical Tools : Depending on the motor type , mechanical tools may be required to adjust physical components such as gearboxes or mechanical linkages.
It is important to emphasize that these tools typically target the motor and vehicle system being calibrated. Proper training and expertise are essential to effectively use these tools and ensure accurate calibration results.
6. What are the challenges of calibration?
Calibrating automotive motors can be challenging due to the complexity of the task itself and what is involved in achieving optimal performance . Some of these challenges include :
Multivariable Optimization : A motor has many interdependent parameters that affect its performance . Balancing these variables to achieve desired results such as efficiency, torque and speed can be complex.
Nonlinear Behavior : Motors exhibit nonlinear behavior under different operating conditions , so it is challenging to develop control strategies that work stably over the entire operating range .
Integration with Vehicle Systems : Electric motors are integrated into larger automotive systems, and their calibration must account for interactions with components such as batteries, inverters, and thermal management systems .
Real -World Variability : Vehicles operate in a variety of environments with changing temperatures, loads, and driving conditions . Achieving consistent performance under these conditions requires reliable calibration.
Sensor Accuracy and Drift : Sensors used for feedback may have errors due to factors such as noise, calibration drift, or environmental conditions . Compensating for sensor errors is critical.
Trade-offs Between Performance and Efficiency : Optimizing one aspect of a motor's performance, such as torque output, can have a negative impact on energy efficiency . A calibrator must strike a balance between these tradeoffs.
Time and Resources : Extensive calibrations require extensive time and resources, including specialized equipment, software, and skilled technicians .
Model Complexity : Some motors have complex internal structures, such as permanent magnet designs, so the corresponding complex mathematical models can affect the calibration strategy.
Safety Concerns : Improper calibration can lead to unsafe conditions affecting vehicle stability, braking and overall safety .
Validation and Testing : Verifying the validity of a calibration requires thorough testing in a variety of situations to ensure that expected results are consistently achieved.
Changing Standards and Regulations : As EV technology develops, standards and regulations may change and require recalibration to meet new requirements.
Updating Software / Firmware : Since software and firmware are updated over time, it can be challenging to ensure that new versions do not affect existing calibrations .
Interdisciplinary Collaboration : Motor calibration involves expertise from multiple disciplines, including mechanical, electrical, and software engineering, thus requiring effective cross - functional collaboration .
Limited Documentation : Sometimes, motor manufacturers may not provide comprehensive calibration documentation, requiring trial and error to find the best settings .
Overcoming these challenges requires a combination of technical expertise, advanced tools, repeated testing and a deep understanding of electric motor characteristics and overall vehicle systems.