The power of the motor should be selected according to the power required by the production machinery, and try to make the motor run under the rated load .The following two points should be paid attention to when choosing:
① If the power of the motor is selected too small, the phenomenon of "small horse-drawn cart" will appear, resulting in long-term overload of the motor. Its insulation is damaged due to heat, and even the motor is burned.②If the power of the motor is selected too large, the phenomenon of "big horse and small cart" will appear, and its output mechanical power cannot be fully utilized, and the power factor and efficiency are not high, which is not only unfavorable to users and the power grid. And also can cause the waste of electric energy.To correctly select the power of the motor, the following calculations or comparisons must be made:In the formula: P-calculated power [KW], F-required pulling force [N], V-working machine line speed [M/S]For the constant load continuous working mode, the power of the required motor can be calculated according to the following formula:In the formula, n1 is the efficiency of the production machinery; n2 is the efficiency of the motor, that is, the transmission efficiency.The power P1 obtained by the above formula is not necessarily the same as the product power. therefore. The rated power of the selected motor should be equal to or slightly greater than the calculated power.also. The most commonly used is the analogy method to select the power of the motor.The so-called analogy method is to compare with the power of the motor used in similar production machinery.Find out how much power motors are used by similar production machinery in this unit or other nearby units, and then choose a motor with similar power for test run . The purpose of the test run is to verify whether the selected motor matches the production machinery.The verification method is:Make the motor drive the production machinery to run, measure the working current of the motor with a clamp ammeter, and compare the measured current with the rated current marked on the nameplate of the motor. If the actual working current of the motor is not much different from the rated current marked on the nameplate. It indicates that the power of the selected motor is appropriate.If the actual working current of the motor is about 70% lower than the rated current marked on the nameplate . It means that the power of the motor is selected too large, and a motor with a smaller power should be replaced.If the measured working current of the motor is more than 40% greater than the rated current marked on the nameplate, it indicates that the power of the motor is selected too small, and a motor with a larger power should be replaced.It is applicable to the mutual conduction of the relationship between the rated power, rated speed and rated torque of the servo motor, but the actual rated torque value should be based on the actual measurement, because there is an energy conversion efficiency problem, the basic value is roughly the same, there will be subtle decrease. . .What if I use stepless speed regulation?In terms of motor output power and torque, what are the characteristics and differences between AC frequency conversion speed regulation and DC speed regulation?Discussion on AC Frequency Conversion Speed Regulation and DC Speed Regulation1. The development of frequency converter DC motor drive and AC motor drive were born successively in the 19th century. It has a history of more than 100 years and has become the main driving device of power machinery. However, due to technical reasons, for a long period of time, AC motors (including asynchronous motors and synchronous motors) are used in the constant speed drive system, which accounts for about 80% of the entire electric drive system. The controlled drag system basically uses a DC motor.However, as we all know, due to structural reasons, DC motors have the following disadvantages :(1) Regular replacement of brushes and commutators is required, which is difficult to maintain and has a short service life;(2) Due to the commutation sparks of DC motors, it is difficult to apply to harsh environments with flammable and explosive gases;(3) The structure is complex, and it is difficult to manufacture a DC motor with large capacity, high speed and high voltage.Compared with DC motors, AC motors have the following advantages :(1) Sturdy structure, reliable operation and easy maintenance;(2) There is no reversing spark, and it can be used in harsh environments with flammable and explosive gases;(3) It is easy to manufacture AC motors with large capacity, high speed and high voltage.Therefore, for a long time, people have hoped to replace DC motors with adjustable-speed AC motors in many occasions, and a lot of research and development work has been done on the speed control of AC motors. However, until the 1970s, the research and development of the AC speed control system has not been able to obtain truly satisfactory results, which also limits the popularization and application of the AC speed control system. It is also for this reason that baffles and valves have to be used to adjust wind speed and flow in electric drive systems that require speed control such as fans and water pumps that are widely used in industrial production. This approach not only increases the complexity of the system, but also causes a waste of energy.After the second oil crisis in the mid-1970s, people fully realized the importance of energy conservation, and further paid attention to and strengthened the research and development of AC speed control technology. With the development of power electronics technology, microelectronics technology and control theory, the performance of power semiconductor devices and microprocessors has been continuously improved, and the variable frequency drive technology has also been significantly developed.With the application of various complex control technologies in frequency converter technology, the performance of frequency converters has been continuously improved, and the scope of application has become wider and wider. At present, frequency converters have not only been widely used in traditional electric drive systems, but also have been extended to almost all fields of industrial production, and have also been widely used in home appliances such as air conditioners, washing machines, and refrigerators.Inverter technology is a comprehensive technology, which is based on control technology, power electronics technology, microelectronics technology and computer technology, and continues to develop with the development of these basic technologies. Table 1-1 lists the basic development process of frequency converter technology in recent years.2. Advantages of the frequency converter speed control system Compared with the traditional AC drive system, the AC drive system using the frequency converter to control the speed of the AC motor has many advantages, such as energy saving, easy to realize the adjustment of the existing motor Speed control can realize large-scale high-efficiency continuous speed control, easy to realize the forward and reverse switching of the motor, high-frequency start-stop operation, electrical braking, and multiple motors with one frequency converter. Speed control, high power factor, small required power capacity, can form a high-performance control system and so on.The following introduces the various main advantages of the frequency converter speed control system mentioned above.In many cases, the purpose of using frequency converters is to save energy, especially for fans, blowers and pump loads that are widely used in industry, speed control through frequency converters can replace traditional baffles and valves. The air volume, flow and head are controlled, so the energy saving effect is very obvious. Because the speed regulation operation for the purpose of energy saving does not have high requirements on the speed regulation range and accuracy of the motor, so a general-purpose frequency converter that is more economical in price is usually used.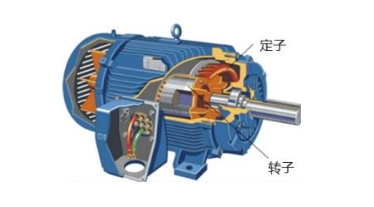
Since the frequency converter can be regarded as an AC power supply with adjustable frequency, for the existing asynchronous motor running at constant speed, it is only necessary to connect the frequency converter and corresponding equipment between the grid power supply and the existing motor to The frequency converter is used to realize speed regulation control, without the need for major equipment modification to the motor and the system itself. In the AC drive system using the frequency converter, the speed control of the asynchronous motor is realized by changing the output frequency of the frequency converter. Therefore, when performing speed control, the motor can work in a range with a small slip rate by controlling the output frequency of the frequency converter, and the speed range of the motor is wide, and the purpose of improving operating efficiency can be achieved.Generally speaking, the speed regulation range of general-purpose inverters can reach more than 1:10 , while the speed regulation range of high-performance vector control inverters can reach 1:1000.In addition, when the frequency converter of the vector control mode is used to control the speed of the asynchronous motor, the output torque of the motor can also be directly controlled. Therefore, the combination of a high-performance vector control frequency converter and a dedicated motor for the frequency converter can reach or exceed that of a high-precision DC servo motor in terms of control performance. In order to realize the forward and reverse switching of the motor in the AC drive system operated by the common grid power supply, it is necessary to use devices such as switches to commutate the power supply.When the frequency converter is used for speed control, it is only necessary to change the switching sequence of the commutation device in the inverter circuit inside the frequency converter to achieve the purpose of commutating the output, and it is easy to realize the forward and reverse switching of the motor without special settings Invert the toggle.In addition, when switching the forward and reverse rotation of the motor running under the grid power supply, if the phase sequence is switched before the motor stops, the motor will flow a current greater than the starting current due to the change of the phase sequence, and there will be a burnout. The motor is dangerous, so usually the commutation operation can only be performed after the motor has come to a complete stop. In the AC speed control system using the frequency converter, the motor can be accelerated according to the law of the ramp function by changing the output frequency of the frequency converter, so as to achieve the purpose of limiting the acceleration current.Therefore, it is easier to form an automatic control system with other equipment when using a frequency converter for speed control. For the AC drive system operated by common grid power supply, the motor cannot be started and stopped at high frequency due to the large starting current of the motor and the power loss proportional to the starting time.For the AC speed control system using frequency converter, since the start and stop of the motor are carried out in the low speed area and the acceleration and deceleration process is relatively smooth, the power consumption and heat generation of the motor are small, and higher frequency start and stop can be carried out. downtime. The above-mentioned characteristics of the frequency conversion speed regulation system can be used in conveyor belts and mobile workbenches using AC drive systems to achieve energy-saving purposes.This is because, in conveyor belts and mobile workbenches driven by asynchronous motors at constant speeds, the motors are usually in working condition all the time, and after speed regulation control with frequency converters, since the motors can be started and stopped at high frequencies, it is possible to Make the conveyor belt or mobile workbench stop running only when there are goods or workpieces, so as to achieve the purpose of energy saving.Since the speed regulation control of the motor in the inverter drive system is carried out by changing the output frequency of the inverter, when the output frequency of the inverter is lowered below the frequency corresponding to the actual speed of the motor, the mechanical energy of the load will be converted into Electric energy is fed back to the power grid to form electrical braking.In addition, some inverters also have a DC braking function, that is, when braking is required, a DC voltage can be applied to the motor through the inverter, and the current generated by this voltage can be used for braking. Compared with mechanical brake, electric brake has many advantages, such as small size, simple maintenance, good reliability and so on. However, it should also be noted that since the electric brake cannot generate the holding torque of the motor in a static state, corresponding measures must be taken in some occasions, such as using it with a mechanical brake at the same time. High-speed drive is one of the most important advantages of frequency converter speed control.This is because for DC motors, due to the constraints of factors such as brushes and commutation rings, high-speed operation cannot be performed. However, for asynchronous motors, due to the absence of the above-mentioned restrictive factors, theoretically speaking, the speed of asynchronous motors can reach quite high speeds.Since the speed of the asynchronous motor is:
In the formula:
n—motor speed, r/min;
f—power frequency, HZ;
p—number of motor poles;
s—slip rate.
When the asynchronous motor is driven by a commercial frequency power supply (50HZ), the maximum speed of the two-pole motor can only reach 3000r/min. In order to obtain a higher speed, it is necessary to use a dedicated high-frequency power supply or use a mechanical speed increaser to increase the speed. Compared with this, the output frequency of the current high-frequency inverter can reach 3000KHZ, so when this high-speed inverter is used to drive the two-pole asynchronous motor, a high speed of up to 180000r/min can be obtained.And with the development of inverter technology, the output frequency of high-frequency power supply is also increasing, so it will become possible to drive at a higher speed. In addition, compared with the high-speed drive system using a mechanical speed increaser, since there is no mechanical device other than the asynchronous motor in the high-speed drive system using a high-frequency frequency converter, its reliability is better, and maintenance and repair are also simpler. In the frequency converter speed control system, the frequency converter and the motor can be set separately.Therefore, through the proper combination with various asynchronous motors, an AC speed control system used in various working environments can be obtained, and there is no special requirement for the frequency converter itself. For example, for an environment with explosion-proof and anti-corrosion requirements, it is only necessary to replace the motor with a special motor, and use an ordinary frequency converter and install it in an ordinary environment other than the environment with explosion-proof and anti-corrosion requirements.Since the frequency converter itself can be regarded as an AC power source capable of frequency regulation and voltage regulation to the outside, one frequency converter can be used to drive multiple asynchronous motors or synchronous motors at the same time, thereby achieving the purpose of saving equipment investment. But for DC speed control system, it is difficult to do this. When a frequency converter is used to drive multiple motors at the same time, if the driving object is a synchronous motor, all the motors will run at the same speed (synchronous speed), and when the driving object is an asynchronous motor with different capacity and load , there will be a certain speed difference between the motors due to the slip. Because the frequency converter drives the asynchronous motor after the AC-DC power conversion, the power factor of the power supply is not affected by the power factor of the motor and is almost a constant value.In addition, when the grid power supply is used to drive the asynchronous motor, the starting current of the motor is 5-6 times the rated current, and when the frequency converter is used to drive the asynchronous motor, the output frequency of the frequency converter can be reduced to a very low level. When starting at low speed, the starting current of the motor is very small, so the capacity of the power supply at the input end of the inverter can also be relatively small. Generally speaking, the capacity of the power supply at the input end of the inverter only needs to be about 1.5 times the output capacity of the motor. This also shows that the frequency converter can also act as a decompression starter at the same time.With the development of control theory, AC speed regulation theory and electronic technology, frequency converter technology has also been fully valued and developed. At present, the performance of the control system composed of high-performance frequency converter and special asynchronous motor has reached and exceeded DC motor servo system. In addition, because the asynchronous motor also has the advantages of strong environmental adaptability and simple maintenance, which many DC servo motors do not have, this high-performance AC speed control system is gradually replacing it in many applications that require high-speed and high-precision control. DC servo system. And because the external interface function of the high-performance frequency converter is also very rich, it can be used as a component in the automatic control system to form the required automatic control system. Due to the above-mentioned advantages of the frequency converter, it has been widely used in various fields.3. The development trend of frequency converter technology The frequency converter has entered the practical period for more than 1/4 century. During this period, power electronics technology and microelectronic technology as the basis of frequency converter technology have undergone rapid development. With the new With the application of power electronic devices and high-performance microprocessors and the development of control technology, the performance-price ratio of frequency converters is getting higher and higher, and the volume is getting smaller and smaller, while manufacturers are still working hard to realize the further miniaturization of frequency converters. making new efforts.From a technical point of view, with the further expansion of the inverter market, the inverter technology will be further developed in the following aspects along with the development of inverter-related technologies in the future:
(1) Large capacity and small volume;
(2) High performance and multi-function;
(3) Improvement of ease of operation;
(4) Increased life and reliability;
(5) Pollution-free.
Large capacity and small volume will continue to develop with the development of power semiconductor devices. In recent years, the voltage-driven power semiconductor device IGBT (Isolated Gate Bipolar Transistor, isolated gate bipolar transistor) has developed rapidly, and is rapidly entering the traditional use of BJT (bipolar power transistor) and power MOSFET (field effect transistor) of various fields. In addition, the IPM (Intelligent Power Module, Intelligent Power Module) with IGBT as the switching device and the monolithic power IC chip integrate the power switching device, drive circuit, protection circuit, etc. in the same package, which has the advantages of high performance and good reliability , so with their development in high current and high withstand voltage, they will be more widely used in small and medium frequency converters. With the development of microelectronics technology and semiconductor technology, the performance of CPU and semiconductor devices used in frequency converters and various sensors is getting higher and higher.With the development of frequency converter technology, the theory of AC speed regulation is becoming more and more mature, and the modern control theory is also getting new applications. All of these provide conditions for further improving the performance of the frequency converter. In addition, with the further promotion and application of frequency converters, supporters are constantly putting forward various new requirements, prompting the manufacturers of frequency converters to continuously make new efforts in improving the performance and functions of frequency converters to meet the needs of users. Need and strive to remain invincible in the fierce market competition.With the continuous expansion of the inverter market, how to further improve the ease of operation of the inverter, so that ordinary technicians and even non-technical personnel can quickly master the use of inverter technology has become a problem that manufacturers must consider. Because only products that are easy to operate can continuously gain new users and further expand the market, new inverters will be easier to operate in the future. With the development of semiconductor technology and the development of power electronics technology, the life and reliability of various components used in the frequency converter are constantly improving, which will further increase the life and reliability of the frequency converter itself. In recent years, people have attached great importance to environmental issues, and thus the name of "green products" has appeared.Therefore, for the frequency converter, its impact on the surrounding environment must also be considered. In the initial stage of the popularization and application of frequency converters, the noise problem used to be a relatively big problem. With the emergence of IGBT low-noise frequency converters, this problem has basically been resolved.However, with the resolution of the noise problem, people's attention has turned to other impacts of the frequency converter on the surrounding environment and they are constantly exploring new solutions. For example, for a frequency converter that uses a diode rectifier circuit and a voltage-shaped PWM inverter circuit, the high-order harmonics caused by the frequency converter itself will distort the power supply voltage and current, and affect other devices connected to the same power supply. However, this problem can be basically solved by using a PWM rectifier circuit in the frequency converter. Although inverters using PWM rectification circuits have not yet been promoted due to price and control technology, but with the development of inverter technology and people's emphasis on environmental issues, the impact of inverters on the environment has been continuously reduced until the introduction of real inverters. The pollution-free inverter has also become the trend of the times.4. It is said that frequency conversion speed regulation is better than DC speed regulation. Is DC speed regulation really going to be eliminated?The reason why frequency conversion speed regulation is more widely used than DC speed regulation is that AC motors are not superior to the principle of frequency conversion speed regulation. Frequency conversion speed regulation can only be used for speed regulation, but the torque cannot be accurately controlled. The reason is very simple. The armature and excitation of DC speed regulation are not coupled, but separated, so that the armature current and excitation current can be precisely controlled. For AC speed regulation, the armature current and excitation current are coupled, so it is impossible to achieve precise control. Although the current variable frequency speed regulation has vector control, that is, using modern control theory, through vector conversion, the coupling in the AC motor The armature current and the excitation current are disentangled to control it, which is the principle of simulating DC speed regulation.But it is very difficult to achieve the control characteristics of DC speed regulation. Therefore, in rolling mills, papermaking and other industries that require high torque, DC speed regulation is still widely used. But only for speed control, the current variable frequency speed regulation can realize the characteristics of DC speed regulation, because the superiority of AC motors cannot be achieved by DC motors . The brush and volume of the DC motor limit its application range. The frequency conversion speed regulation can be said to be developed from fans and water pumps. It is due to the need for energy saving of fans and water pumps. Frequency conversion speed regulation is the best choice, but I personally think that compared with the current electricity price and the price of the inverter itself, this kind of energy saving is meaningless, because it takes at least 5-6 years to recover the investment of the inverter, and during these 5-6 years , the working conditions do not know what changes will take place. Therefore, the frequency converter is best used in occasions where speed regulation is required, but the requirements for starting performance and torque adjustment are not very strict, and such occasions abound, which is the reason why frequency conversion speed regulation is widely used. Therefore, it can be said that it is the best if the DC speed controller is used to control the AC motor. If you can really do this, you will be the second Bill Gates, and even get the Nobel Prize.