Stator core structure and manufacturing process and industrial development
Date:2023-03-15 Author:Shandong Xinda Motor Co., Ltd.
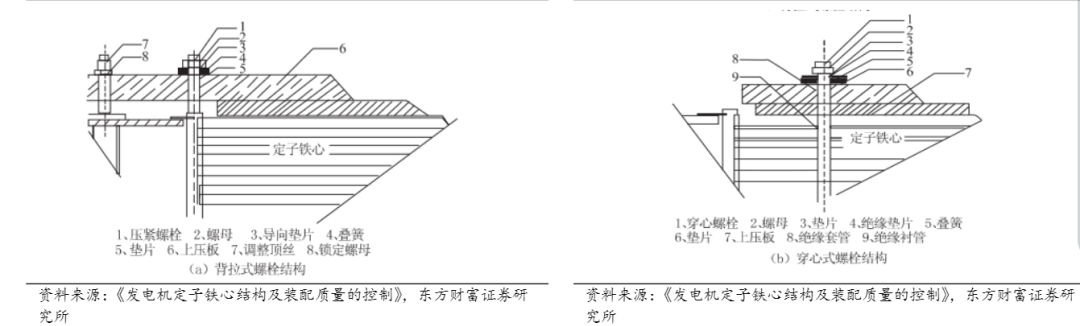
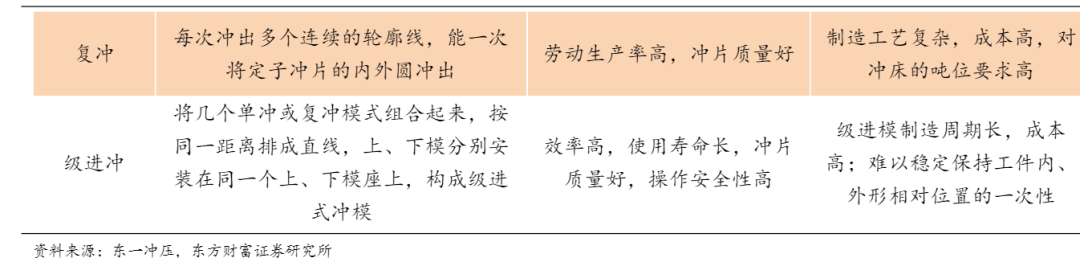
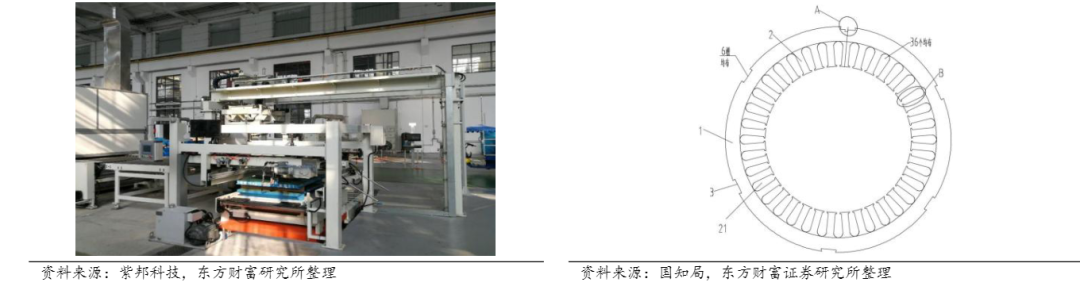
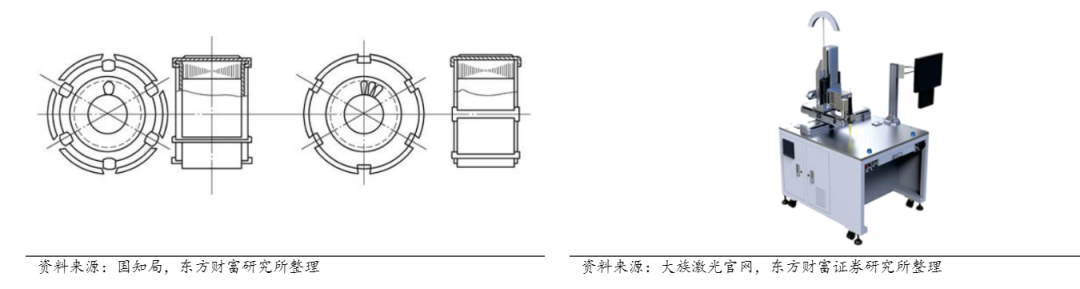
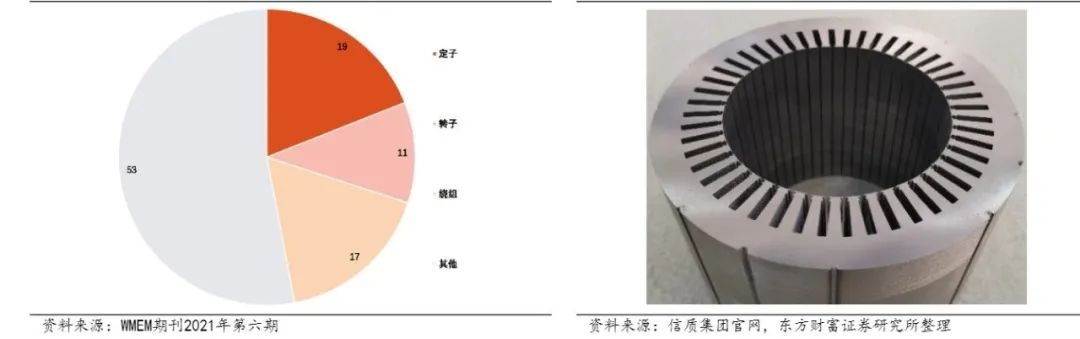
Xinzhi Group
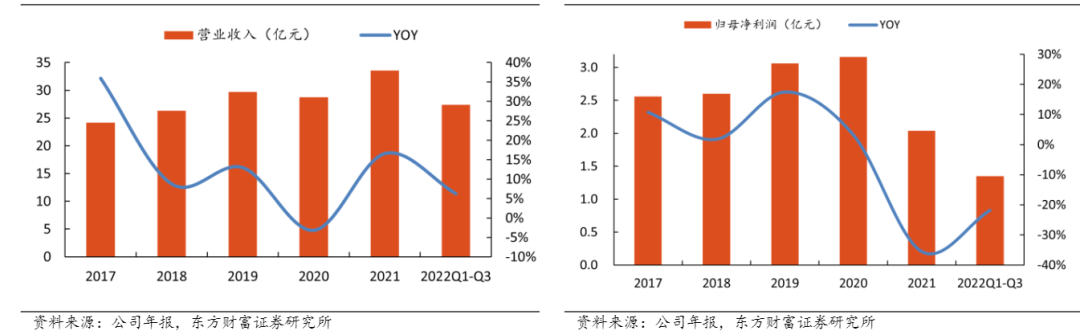
Longsheng Technology
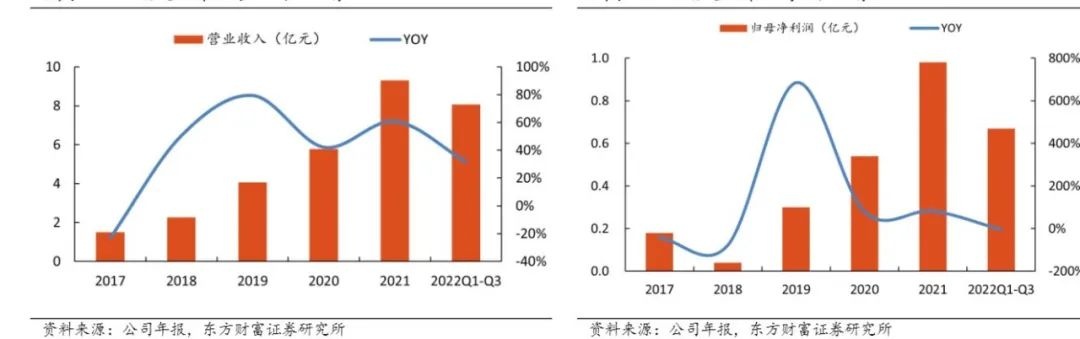
Zhenyu Technology
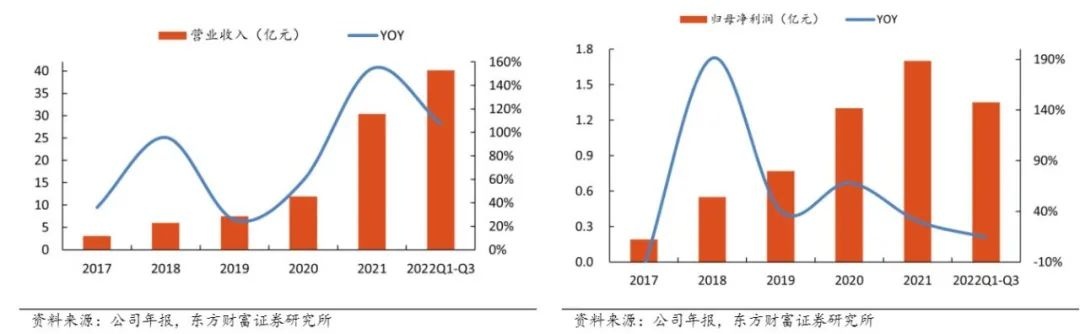
Xinzhi Group
Longsheng Technology
Zhenyu Technology