The "big three electric" drive system of new energy vehicles includes a drive motor, a motor controller and a reducer. The main function of the drive motor is to provide power for new energy vehicles and convert the electric energy of the power battery into mechanical energy. The main components include stator, rotor, housing, and structural parts; Alternating current, according to the vehicle control command to control the operation of the drive motor, the main components include power semiconductors, control software and sensors; the reducer is also called the transmission system, the main function is to reduce the output speed and increase the output torque. The "small three power" power system of new energy vehicles includes an on-board charger (OBC), a DC-DC converter, and a high-voltage power distribution unit (PDU). The main function of the on-board charger is to charge the power battery of new energy vehicles. The main components include PFC circuit, isolated DC/DC and low-voltage auxiliary power supply; The direct current is converted into low-voltage direct current, and the main components include the main control board, power devices and inductors; the main function of the high-voltage power distribution unit is to be responsible for the power distribution and management in the high-voltage system solution of the new energy vehicle, and the main components include copper bars, relays, and fuses. devices, pre-charge resistors, current collectors, etc.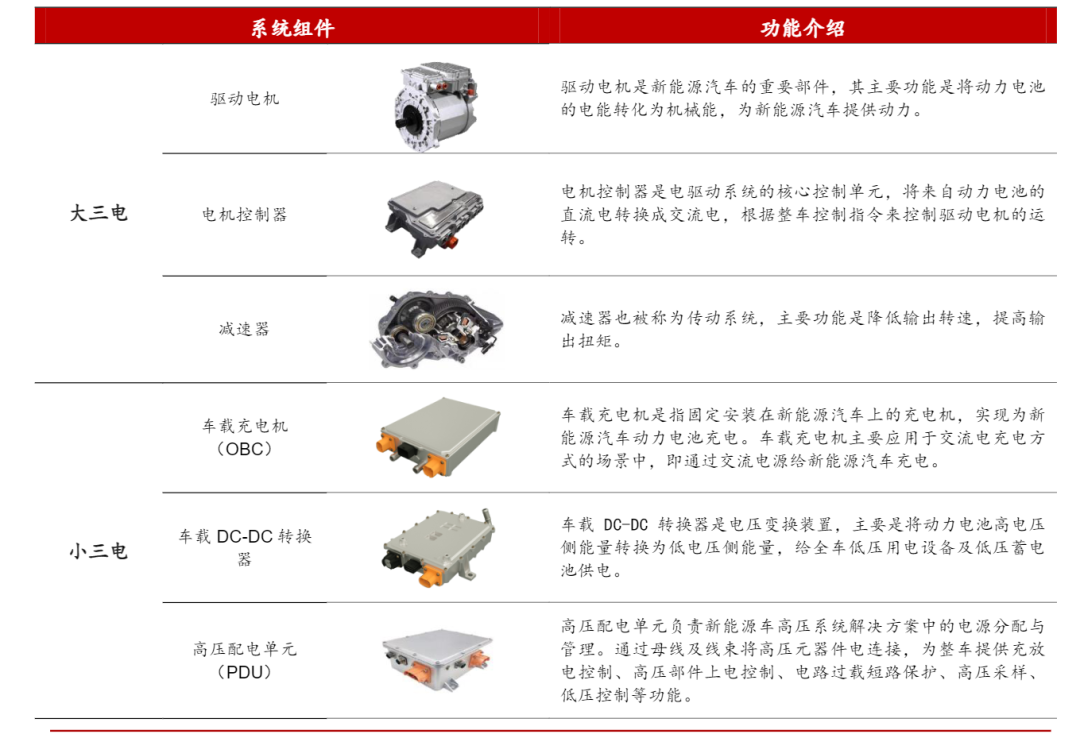
Source: Inboll, Jingjin Electric, China Merchants Bank Research Institute
Above: Function introduction of new energy vehicle electric drive system
Permanent magnet synchronous motor has become the mainstream, and flat wire oil cooling is the direction of technological development
The drive motor is an important part of the electric drive system, and its main function is to convert the electric energy of the power battery into mechanical energy to provide power for new energy vehicles. The drive motor utilizes the principle of electromagnetic induction to generate a rotating magnetic field by means of an energized coil (stator winding) and act on the rotor to form a magnetoelectric force, thereby generating rotational torque to drive the vehicle. There are four main technical routes for new energy vehicles: DC motors, AC asynchronous motors, permanent magnet synchronous motors and switched reluctance motors. Power density and torque density have become key indicators for measuring motor performance. Due to many defects, DC motors have been gradually eliminated by the market. Switched reluctance motors have higher torque ripple, but higher vibration and noise, and are mainly used in commercial vehicles. In the field of passenger vehicles, permanent magnet synchronous motors and AC asynchronous motors are mainly used at present.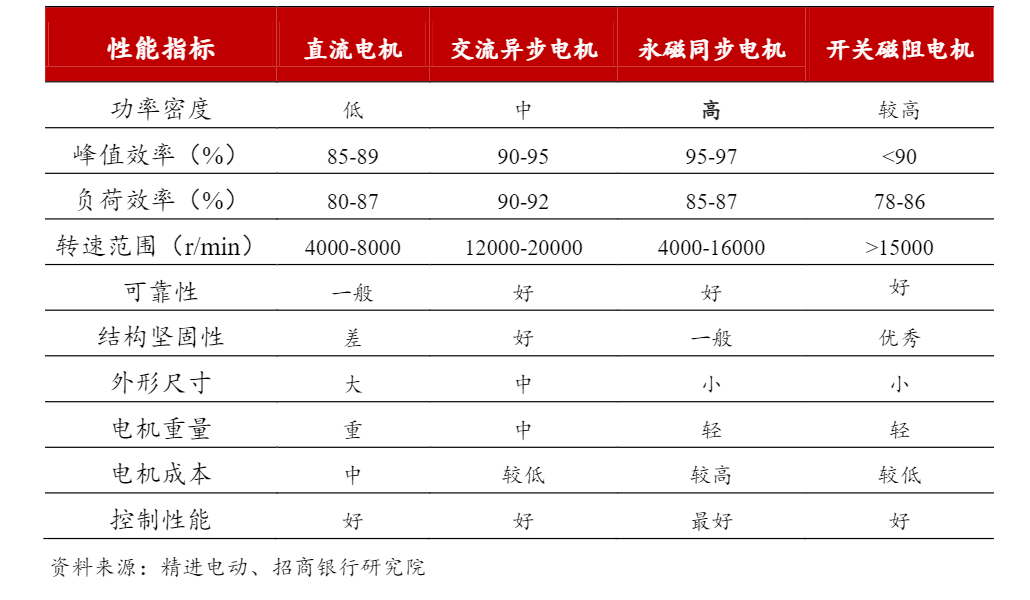
Above: Comparison of the main technical routes of drive motorsPermanent magnet synchronous motors have excellent performance and have become the mainstream choice for new energy vehicles . The AC asynchronous motor generates a rotating magnetic field by energizing the stator windings, and the rotor rotates with the rotating magnetic field of the stator, finally driving the motor to rotate. The speed of the rotor of the AC asynchronous motor is slower than that of the stator, and the rotor and the stator form an asynchronous operation. The main difference between the permanent magnet synchronous motor and the AC asynchronous motor is the rotor structure. The permanent magnet synchronous motor places permanent magnets on the rotor, and the rotor magnetic field is generated by the permanent magnets, eliminating the need for excitation current or induction current. The rotating magnetic field of the stator will pull The rotors rotate synchronously. From the performance point of view, the permanent magnet synchronous motor can still guarantee high efficiency in the transient state, and at the same time has a greater power density, which is suitable for frequent start-stop conditions and small passenger car layout space.
Permanent magnet synchronous motors account for 90% of the installed capacity of passenger cars, and AC asynchronous motors are partially used in high-end models with dual motor configurations. From the perspective of installed capacity, permanent magnet synchronous motors have occupied most of the installed market of new energy passenger vehicles by virtue of their performance advantages; AC asynchronous motors have better performance in high-speed scenarios and are mainly used as a dual-motor supporting solution for high-end models. According to the data of the NE era, from January to July 2022, there will be 2.796 million sets of driving motors for new energy passenger vehicles in my country, including 2.502 million sets of permanent magnet synchronous motors, accounting for 89.5%; 91,000 sets of AC asynchronous motors, accounting for 3.3% %. AC asynchronous motor supporting high-end models include Tesla Model 3, Tesla Model Y, Weilai ES 6, Weilai ES8, Mercedes-Benz EQA, Mercedes-Benz EQB, Volkswagen ID4.X, Volkswagen ID6.X, etc. The concentration ratio of the electric motor market has declined slightly, with OEMs taking the lead, and third-party suppliers have fierce competition. According to the data of the NE era, in H1 of 2022, the installed capacity of new energy passenger car drive motors in my country will be 2.318 million sets, a year-on-year increase of 129.3%. Due to the hot new energy vehicle market and many new entrants in the drive motor market, the market share of TOP10 suppliers will drop from 81.6% in 2020 to 75.6% in H1 in 2022.In H1 2022, the top 10 suppliers of drive motors for new energy passenger cars in my country are BYD, Tesla, Founder Motor, Nidec, Inovance Technology, NIO Drive Technology, Shanghai Electric Drive, United Electronics, Juyi Power, Shuanglin car. Among them, BYD and Tesla continued to expand their market share relying on the advantages of vehicle sales; third-party suppliers competed fiercely, Founder Motor steadily occupied the third place in the market, and the competitive advantages of other suppliers were not significant.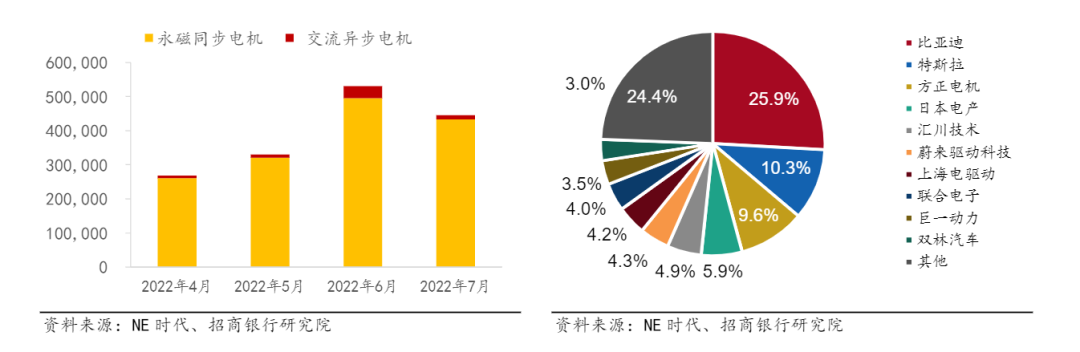
Left of the picture above: Installed capacity of drive motors for new energy passenger vehicles from April to July 2022Above right: Market share of drive motors for new energy passenger vehicles in H1 in 2022Continue to improve power density and torque density, and flat wire and oil cooling have become the main technical development directions of motors. The performance and efficiency of the drive motor directly affect the power, torque and reliability of the vehicle. With the continuous advancement of motor technology, various technological innovations have appeared in the form of motor windings and motor cooling methods, among which flat wire windings and oil-cooled motors have become the main technology development direction, with high power, high efficiency, better heat dissipation performance, etc. advantage. The flat wire motor has a higher power density and a rapid increase in penetration rate. The notable feature of the flat wire winding motor is that flat copper wire with a larger cross-sectional area is used in the stator winding to increase the slot fullness of the motor. Compared with ordinary round enameled wire windings, flat wire windings have the characteristics of higher energy density, higher motor efficiency, stronger heat dissipation capacity, and lower mechanical noise and electromagnetic noise under the same volume. In 2020, the penetration rate of flat wire motors for new energy vehicles in the world will be 15%, and the penetration rate of flat wire motors in my country will be about 10%. In 2021, as car companies such as Tesla, Volkswagen, BMW, BYD, and Weilai began to replace flat wire motors on a large scale, the penetration rate of flat wires will increase significantly.In the first half of 2022, almost all mid-to-high-end new energy vehicles will use flat wire motors. As of July 2022, the penetration rate of flat wire motors in new energy passenger cars in my country will reach 41%.
Oil-cooled motors can further improve the thermal management efficiency of motors, and the penetration rate of supporting flat wire motors will continue to increase. The power efficiency of the motor is limited by the thermal management capability of the motor. Improving the cooling capacity of the motor can increase the power density and improve the service life of the motor. Common motor cooling methods include air cooling, water cooling, and oil cooling. The air-cooled motor mainly uses the heat dissipation fins outside the casing to take away the heat through the flowing air flow. It is characterized by small size, light weight, and relatively poor heat dissipation performance. The water-cooled motor adopts the method of adding water channels in the motor casing to take away the heat through heat exchange. It is characterized by good heat dissipation and has become the most important heat dissipation method at present. Oil-cooled motors replace the heat dissipation medium in water cooling with special oil materials, which are characterized by good cooling effects, especially suitable for flat wire motor scenarios, and are the main development direction in the future. According to the data of the NE era, the penetration rate of oil-cooled motors for new energy passenger vehicles in my country will reach 27% in July 2022, and the penetration rate of liquid-cooled motors will remain at around 60%.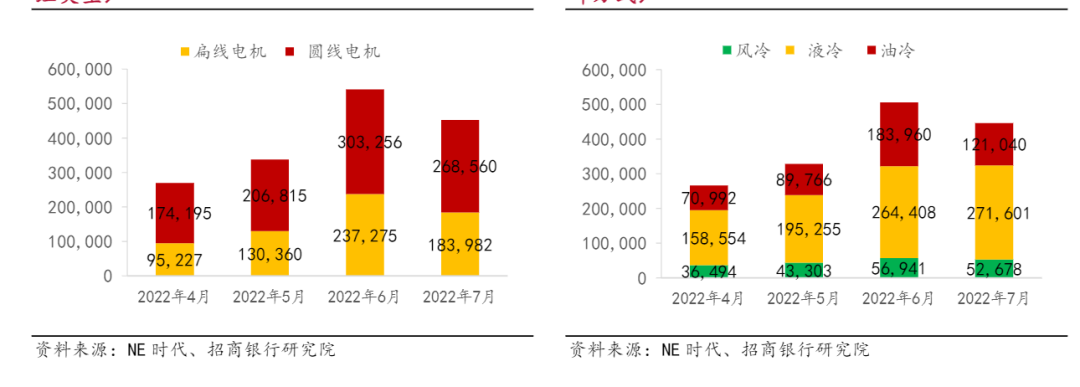
Above left: Installed capacity of new energy passenger car motors (winding type) from April to July 2022Above right: Installed capacity of new energy passenger car motors (cooling type) from April to July 2022
Focusing on improving the volumetric power density, IGBT and power modules are the mainstream solutions
The motor controller is the core control unit of the electric drive system, which converts the DC power from the power battery into three-phase AC power, and controls the operation of the drive motor according to the vehicle control instructions. The motor controller is mainly composed of main control board, drive board, power device, film capacitor, current sensor, etc., with high-frequency and high-power module as the core, and hardware and software development, power electronics design, and control algorithm optimization are carried out around it, so as to realize the Precise control of motor speed, steering, angle, and response time.
Motor controllers require close cooperation between hardware and software, and improving volumetric power density is its core goal. In terms of hardware, the motor controller must not only meet the various electrical performance indicators of the vehicle, but also pursue high power density and high cost performance. The hardware relies on high-frequency and high-power semiconductor process technology. By improving hardware circuit design capabilities, providing electromagnetic compatibility capabilities, and improving heat dissipation effects, the overall performance of the motor controller is finally improved.In terms of software, motor control technology generally uses vector frequency conversion speed control software. Due to the difference in motor parameters and the large variation of motor parameters with temperature when the vehicle is running, it is necessary to monitor the motor parameters in real time through software and adjust the working parameters of the controller. By identifying the motor parameters, the motor can be precisely controlled to ensure the operating efficiency of the drive system, reduce system heat generation, and increase mileage. The core index of the motor controller is the volume power density. In the past ten years, the volume power density of the motor controller has continued to increase, from 11KW/L based on IGBT in 2010 to 22KW/L based on IGBT in 2017, and to 2022 based on SiC. 60KW/L. The rapid increase in volume power density has promoted the explosive growth of new energy vehicles.
Above: The main technical indicators of the motor controllerThe demand for motor controllers is growing rapidly, and the market concentration continues to increase. According to the data of the NE era, in 2022 H1, the installed capacity of motor controllers for new energy passenger vehicles in my country will be 2.318 million sets, a year-on-year increase of 129.3%. Among them, the market share of TOP10 suppliers continued to increase, from 69.9% in 2020 to 77.1% in H1 in 2022. According to the data of the NE era, the TOP10 suppliers of motor controllers for new energy passenger cars in my country in H1 2022 are BYD, Tesla, Inovance Technology, Nidec, Sunshine Electric Power, Inboll, Weilai Drive Technology, United Electronics, Juyi Power, Shanghai Electric Drive. Among them, BYD and Tesla continue to expand their market share relying on the advantages of vehicle sales; third-party supplier Inovance Technology has steadily occupied the third place in the market.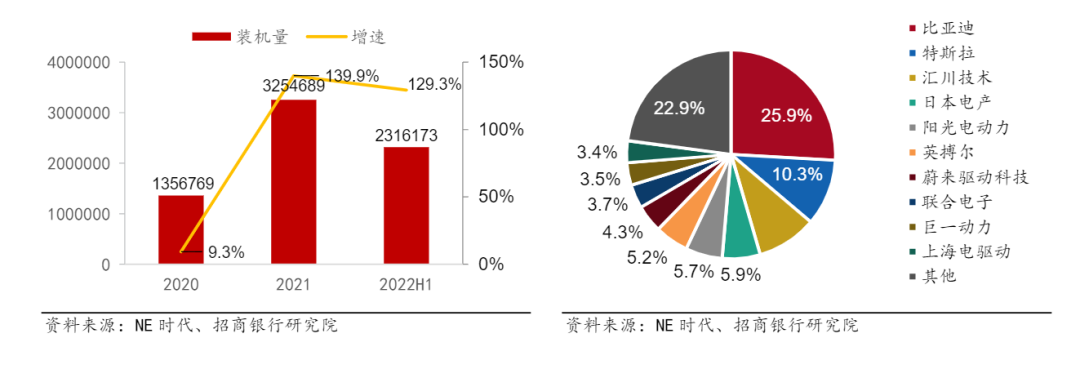
Above left: 2020-2022H1 New Energy Passenger Vehicle Electric Control Installed CapacityAbove right: 2022 H1 New Energy Passenger Vehicle Electronic Control Market ShareIn the cost structure of the motor controller, the power module occupies an important position. The main components of the motor controller include power modules, PCB boards, sensors, housings, and control software. The performance of the power modules has a great influence on the reliability and stability of the motor controller products. The power modules include IGBTs (insulated gate bipolar transistors) , MOSFET power field effect transistor, SiC-MOSFET (silicon carbide) and other solutions. In terms of the cost composition of the IGBT solution, the power module accounts for about 37%, the drive circuit accounts for about 12%, the control circuit accounts for about 16%, the housing accounts for about 12%, and the current sensor accounts for about 5%. Gate driver chips account for about 4%. Domestic suppliers have made major breakthroughs in the field of power modules. Power modules account for the highest proportion of electronic control costs, and price fluctuations have a greater impact on the cost of motor controllers. The main players in the market are foreign chip giants. According to Yole data, major suppliers in the power module market include Infineon, STMicroelectronics, Bosch, Texas Instruments, and ON Semiconductor. According to the data of the NE era, the TOP10 suppliers of power modules for new energy passenger vehicles in my country in H1 2022 are Infineon, BYD Semiconductor, Star Semiconductor, CRRC Times, STMicroelectronics, ON Semiconductor, Bosch, Fuji Electric, Borg Warner, Hitachi. Among them, BYD Semiconductor, STAR Semiconductor, and CRRC Times have made major breakthroughs, becoming major suppliers of domestic automotive power modules, and rapidly expanding their market share.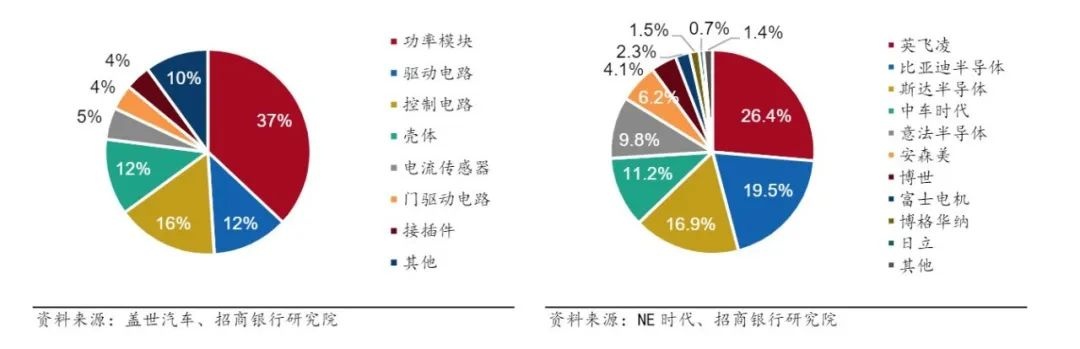
Above left: Cost structure of motor controllerAbove right: Market share of new energy passenger car power modules in H1 in 2022IGBT is currently the most mainstream power chip, and SiC-MOSFET is the future development trend. The power module of the motor controller mainly uses three power chips: IGBT, Si-MOSFET, and SiC-MOSFET. IGBT has both the advantages of high input impedance of MOSFET and low conduction voltage drop of GTR. It has low driving power and low saturation voltage. It is very suitable for the field of new energy vehicles with a DC voltage of 600V and above. With its performance and cost advantages It has become the most mainstream installed power chip at present. Si-MOSFET has relatively poor performance and low voltage resistance, and is better at low-power motor controllers. It is mainly used in AOO and A0-class models, including Wuling Rongguang Mini, Chery QQ, Beiqi Big Cat, Punk Duoduo, Dongfeng Fengshen E70, Dongfeng Xiaokang MINI , Roewe Clever, Baojun E200, etc. SiC-MOSFET has the advantages of high switching frequency, high efficiency, high power density, etc., but the current cost is relatively high, and it is mainly used in mid-to-high-end B-class and C-class cars, including Tesla Model Y, Model 3, Weilai ET7, BYD Tang EV, BYD Han, etc. According to the data from the NE era, in July 2022, IGBTs accounted for about 85%, Si-MOSFETs accounted for about 12%, and SiC-MOSFETs accounted for about 3% of the motor controller power module vehicle shipments in July 2022. Power modules are currently the most mainstream packaging route for motor controller power devices. The application of power chips in new energy vehicles can be divided into two technical routes: module and single-tube parallel connection. The single-tube parallel connection scheme adopts the method of IGBT and MOSFET single-tube to expand power through parallel connection. The cost of a single tube is significantly lower than that of the module, which has the advantage of high cost performance. The disadvantage is that the process is complicated and the reliability is poor. It is mainly used in high-cost For models below A-level, domestic Inovance Technology, Sunshine Electric Power, and Inboer have all launched single-tube parallel solutions and achieved mass production. The module solution uses standardized IGBT and SiC-MOSFET module products of specific specifications. The advantages are high integration, high reliability, and reduced system design complexity. The disadvantage is high cost. It is mainly used in mid-to-high-end B-class and above models. The main suppliers of modules are overseas giants such as Infineon and STMicroelectronics. Shanghai Electric Drive has launched mass-produced products based on domestic power modules. According to the data of the NE era, in July 2022, among the shipments of motor controller power packaging types, single-tube splicing accounted for 19%, and modules accounted for about 81%.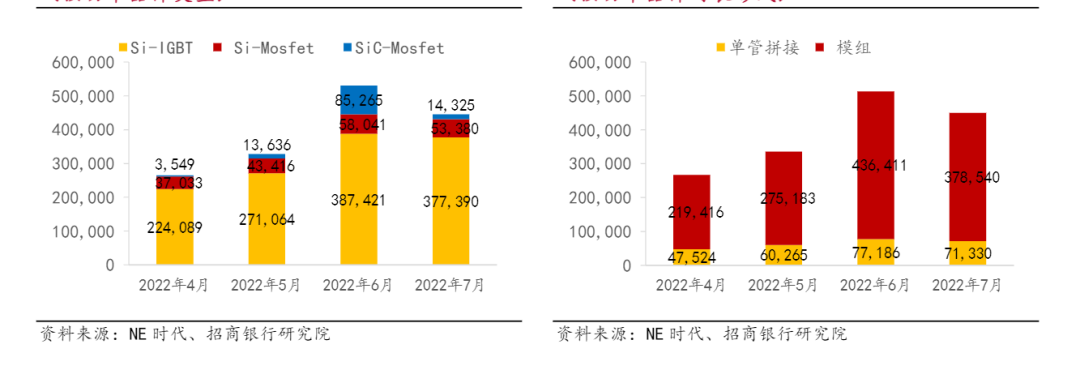
Left in the above picture: Installed capacity of new energy passenger vehicle electronic control from April to July 2022 (by type of power device)Right in the above picture: Installed capacity of new energy passenger car electronic control from April to July 2022 (according to the packaging form of power devices)
Single-stage is the current mainstream solution, and multi-stage is the future development trend
The configuration of the reducer is the mainstream solution for new energy vehicles. The reducer is also called the transmission system. It is mainly composed of transmission parts (gears or worms), shafts, bearings, boxes and accessories. It is generally installed behind the drive motor, or integrated with the drive motor as a "drive + transmission" combination 1. Integrated Products. The main function of the reducer is to reduce the output speed and increase the output torque. If the reducer is not configured, the torque output from the motor to the wheels is too small, and it is difficult to meet the demand in high-torque scenarios such as climbing. In order to increase the torque of the wheels, choosing a high-torque motor will lead to the problems of extremely high price and poor cost performance of the whole vehicle. Considering the two aspects of technology maturity and cost, motor supporting reducer has become the mainstream solution for new energy vehicles. According to the classification of transmission grade, the reducer can be divided into single-stage reducer, two-speed reducer and multi-speed reducer. Since the motor has different working characteristics from the traditional internal combustion engine, there is no need to add a multi-speed reducer, but only a single-stage reducer or a two-speed reducer.
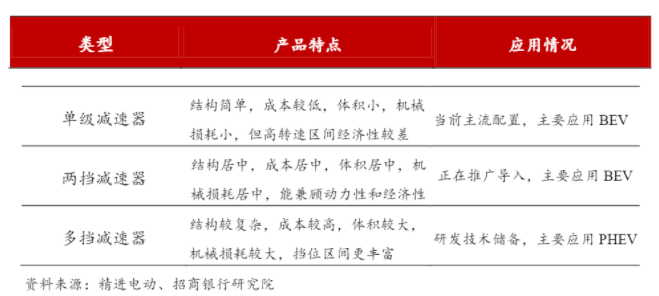
Above: The main technical characteristics and application of the reducerSingle-stage reducer is the main choice for pure electric vehicles at present. With the advantages of high transmission efficiency, abundant optional resources, small development difficulty, and low cost, single-stage reducers can not only meet the requirements of small and medium-sized new energy vehicles, but also reduce the adaptation threshold for selecting motors. Therefore, the solution with single-stage reducer has become the solution adopted by mainstream pure electric vehicles in the world.
Two-speed and multi-speed reducers are expected to become the future development trend. In the high-speed scene of the single-stage reducer, the efficiency of the motor is low, and the torque will drop rapidly. Adding one gear to the single-stage reducer can make the motor work in the high-efficiency speed range as much as possible, so as to reduce loss and increase the cruising range. The two-speed reducer has become the development trend of pure electric vehicles. The multi-speed reducer can reduce power consumption and improve the battery life of electric vehicles, making it the main choice for plug-in hybrid vehicles. The concentration of the reducer market has declined, and the complete vehicle supporting enterprises have taken the lead. According to the statistics of the NE era, in July 2022, the penetration rate of single-stage reducers for new energy passenger vehicles in my country will reach 77%, and the penetration rate of two-speed and multi-speed reducers will be around 23%. Among them, the market share of TOP10 suppliers has declined, from 72.6% in 2021 to 69.5% in H1 in 2022. In H1 2022, the top 10 suppliers of new energy passenger car reducers in my country are BYD, Tesla, Wuling Industry, Zhuzhou Gear, Shuanghuan Transmission, Qingshan Transmission, Magna, Meiqiao, Honeycomb Transmission, and Shanghai Transmission. Among them, BYD, Tesla, and Wuling Industry rely on the advantages of vehicle sales to occupy the top three; among the third-party suppliers, Zhuzhi has become the leader and steadily occupies the fourth place.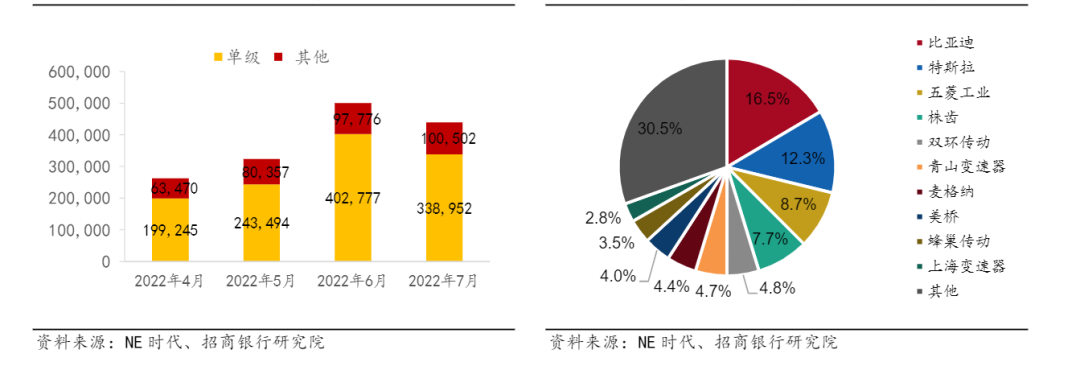
Left in the picture above: Installed capacity of new energy passenger car reducers from April to July 2022Above right: 2022 H1 new energy passenger car reducer market share
All-in-one integration has become an industry trend
The new energy vehicle power system is also called "small three power", generally including on-board charger (OBC), on-board DC-DC converter and high-voltage power distribution unit (PDU), its main function is to provide power battery charging and discharging, power conversion and power distribute.
The on-board charger has become a must-have system, which can be selected according to power level and voltage level. The charging methods of new energy vehicles mainly include AC charging and DC charging. The on-board charger is mainly used in the scenario of AC charging, that is, charging new energy vehicles through AC power. When using AC charging, since the input port of the power battery is required to be DC, an on-board charger needs to be used to convert the AC to DC; when using DC charging, the DC power can be directly adapted to the input port of the power battery, and there is no need to use an on-board charger. From the perspective of OEMs, in order to meet the diversity of user charging scenarios, on-board chargers have become a must-have system. From the perspective of power level, it can be divided into 3.3kW, 6.6kW, 11kW, and 22kW, of which 6.6kW bidirectional charger will be the mainstream configuration, and 11kW and 22kW will be optional for mid-to-high-end models. In terms of voltage levels, it can be divided into low-voltage, medium-voltage, and high-voltage platforms. The 200V-500V medium-voltage platform is still the mainstream, and the 700V-1000V high-voltage platform will become an option for mid-to-high-end models.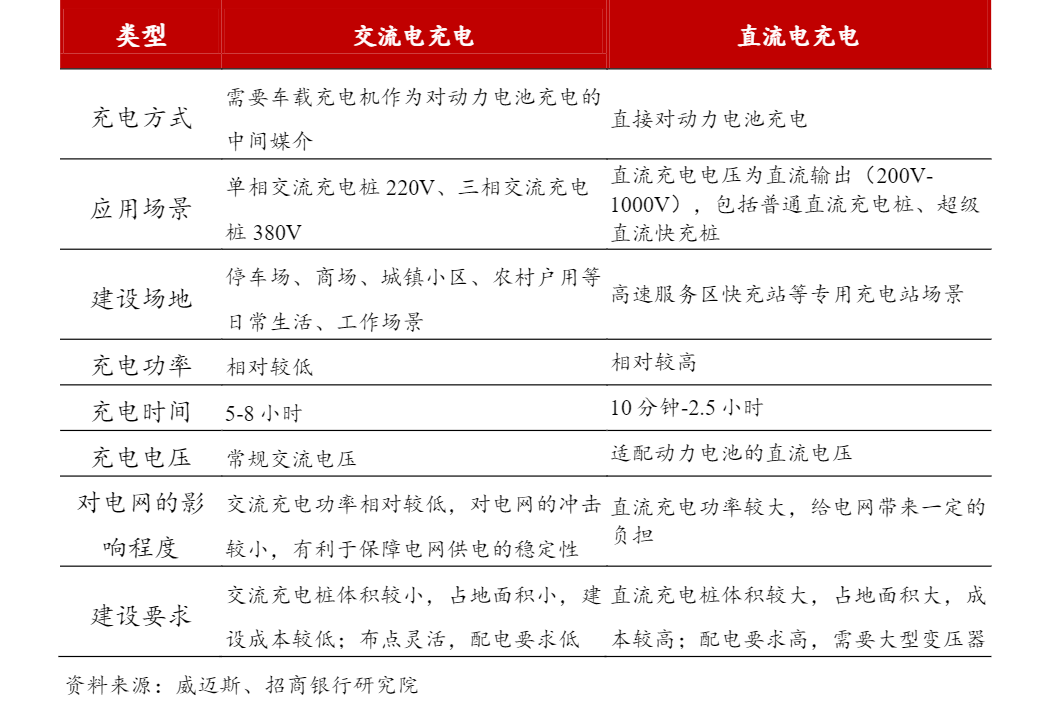
Above: Comparison of different charging schemes for new energy vehiclesThe market concentration of on-board chargers has increased, with third-party suppliers as the main players. The on-board charger market is highly concentrated, the market competition pattern will continue to be optimized, and the competitiveness of leading suppliers will continue to increase. According to the data of the NE era, the installed capacity of on-board chargers for H1 new energy passenger vehicles in 2022 will be 2,083,407 sets. The market concentration of vehicle chargers has increased, and the market share of TOP10 suppliers will rise from 91.3% in 2021 to 94% in H1 in 2022. In H1 2022, the TOP10 suppliers of on-board chargers for new energy passenger vehicles in my country are BYD, Vmax, Inpower, Ford Technology, Tesla, Xinrui Technology, Tiecheng Technology, Kostal-Huayang, Huawei, Panasonic. The on-board charger market is dominated by third-party suppliers, among which VMAX ranks first among third-party suppliers. 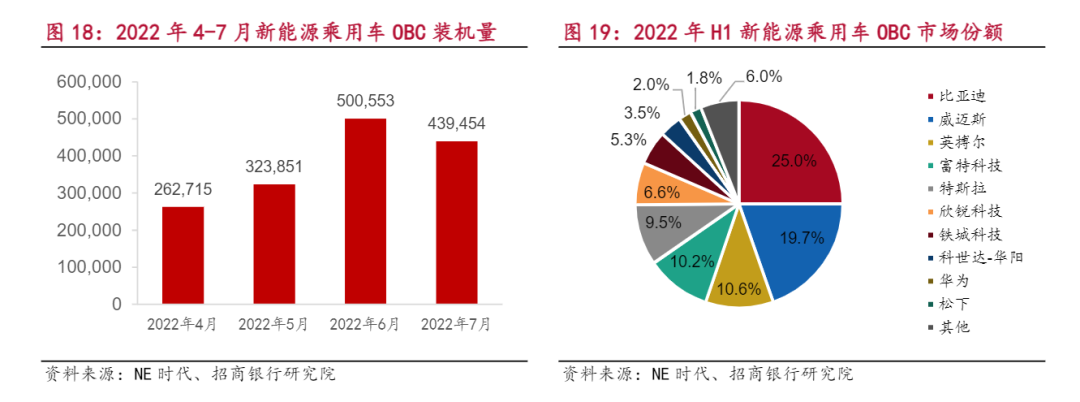
Left in the above picture: OBC installed capacity of new energy passenger vehicles from April to July 2022Above right: 2022 H1 new energy passenger vehicle OBC market shareThe main function of the DC-DC converter is a new energy vehicle voltage conversion device. The vehicle-mounted DC-DC converter converts the energy on the high-voltage side of the power battery into energy on the low-voltage side, and supplies power to the low-voltage electrical equipment and low-voltage batteries of the entire vehicle. When the low-voltage electrical equipment of new energy vehicles is running, it cannot directly get power from the high-voltage power battery, but gets power from the low-voltage battery or from the high-voltage power battery through a DC-DC converter; the energy stored in the low-voltage battery is also obtained through DC- The DC converter obtains electricity from the high-voltage power battery. Vehicle-mounted DC-DC can be divided into 2KW platform, 3KW platform and 5KW platform according to power, among which 2KW and 3KW will be the mainstream configuration schemes, and 5KW platform is optional for mid-to-high-end models. The packaging methods of vehicle-mounted DC-DC converters include water cooling, air cooling, natural air cooling, and module methods.The main function of the high-voltage power distribution unit is responsible for the distribution and management of power in the high-voltage system of new energy vehicles. The high-voltage power distribution unit provides functions such as charge and discharge control, power-on control of high-voltage components, circuit overload and short-circuit protection, high-voltage sampling, and low-voltage control for the entire vehicle. The high-voltage power distribution unit distributes the high-voltage power of the power battery to the motor controller, drive motor, electric air-conditioning compressor, DC-DC and other high-voltage electrical equipment, and at the same time distributes the high-voltage charging current of the charging interface to the power battery for charging. The high-voltage power distribution unit has heat dissipation structures such as water cooling and air cooling. The all-in-one integrated design of the power system has become a trend. As new energy vehicles have higher and higher requirements on the power system, products integrating on-board chargers, on-board DC-DC converters and high-voltage power distribution units have gradually become the mainstream solution for on-board power supplies. Through the integration of vehicle power supply systems, high power, miniaturization, integration, intelligence, and high cost performance have become the development direction of vehicle power supply products.
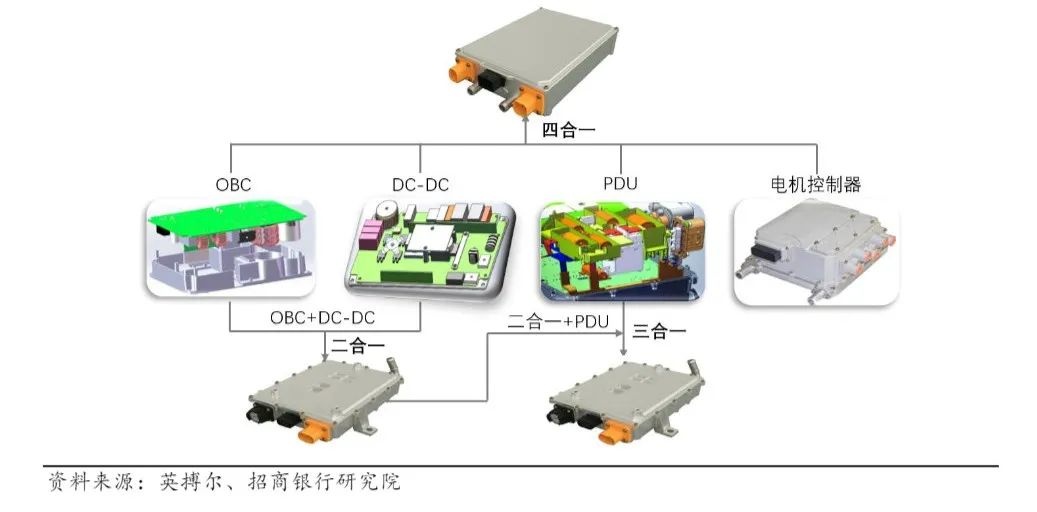
Above: All-in-one integrated design of power supply is the trend