Abstract: In-wheel motor drive technology represents an important development direction for new energy vehicle drive systems. This paper introduces the characteristics of in-wheel motor drive electric vehicles, summarizes the technical requirements and drive forms of in-wheel motor drive, and briefly compares and analyzes the research overview of in-wheel motor drive forms at home and abroad. The key issues that need to be solved in in-wheel motor drive technology are proposed, and the core technologies of reducing unsprung mass, suppressing vertical vibration effects, and reducing in-wheel motor torque pulsation are discussed, and the development trend of in-wheel motor drive technology is predicted.With the increasing problems of energy shortage and environmental pollution, vigorously developing energy-saving and environmentally friendly new energy vehicles has become an inevitable choice for the development of the world's automobile industry. Pure electric vehicles have developed rapidly in recent years with their outstanding advantages such as high efficiency, no pollution, and low noise. In-wheel motor-driven electric vehicles have unique advantages in many aspects, such as simple and compact structure, efficient and energy-saving transmission system, and independent controllable driving and braking torque, representing an important direction for the development of the next generation of electric vehicles.As the core component of the electric vehicle drive system, the performance of the wheel hub motor is crucial. Since the wheel hub motor is installed in a small wheel hub space, the motor system is significantly affected by factors such as temperature rise, magnetic field saturation, road excitation (vibration, impact), torque fluctuation, and load mutation, which seriously restricts the control performance of the wheel hub motor. In addition, due to the introduction of the wheel hub motor, the unsprung mass of the car increases, reducing the ride comfort and safety of the car. With the development of new energy vehicles, the wheel hub motor has become a research hotspot in the field of electric vehicles.This paper introduces the characteristics of electric vehicles driven by wheel hub motors, summarizes the technical requirements and drive forms of wheel hub motors, and compares and analyzes the research overview of wheel hub motor drive forms at home and abroad. It discusses the key issues and core technologies that need to be urgently solved in wheel hub motor drive technology, and predicts the future development trend of wheel hub motor drive technology.1. Characteristics of electric vehicles driven by wheel hub motors
Compared with traditional centralized vehicles, electric vehicles driven by wheel hub motors have the following characteristics:
(1) Improved transmission efficiency. The engine, clutch, transmission, drive shaft and main reducer are eliminated, which greatly simplifies the power transmission system structure and significantly improves the transmission efficiency.
(2) Simplified chassis structure. The chassis structure of the electric vehicle driven by the in-wheel motor is greatly simplified, which saves space inside the vehicle and improves the utilization rate of the vehicle body space.
(3) Reasonable axle load distribution. The vehicle layout design is flexible and the vehicle mass distribution design has a large degree of freedom, making the axle load distribution more reasonable.
(4) Flexible drive system layout. In-wheel motor drive technology increases the flexibility of the vehicle power system layout. By coordinating the drive mode and drive wheels, multi-axle and multi-wheel drive of electric vehicles can be achieved to meet the driving requirements under different working conditions.
(5) Improved vehicle driving stability. In-wheel motor drive technology achieves control of the electric vehicle chassis by independently controlling the speed, driving or braking torque of different wheels. The torque response speed and response accuracy of the in-wheel motor have an important impact on improving vehicle driving stability.
(6) Improved regenerative braking recovery rate. The electric vehicle hub motor drive system uses electromechanical composite braking or electric braking to achieve energy recovery and utilization, reduce energy consumption, and increase the driving range of electric vehicles.2. Technical requirements and drive forms of hub motor drive2.1. Technical requirements for wheel hub motor driveTaking into account the complexity of electric vehicle operating conditions and the characteristics of the wheel hub motor drive mode, the technical requirements for the wheel hub motor mainly include: (1) Due to the limited weight of the vehicle and the limited wheel hub space, the wheel hub motor is required to have a higher torque density; (2) In order to meet the requirements of rapid starting, acceleration, climbing and frequent starting and stopping of the vehicle, the wheel hub motor should have a very wide speed regulation range and strong overload resistance, and maintain high efficiency in a wide speed and torque working range; (3) The wheel hub motor should be able to withstand the influence of high temperature, low temperature, severe vibration and changeable weather, and be able to work normally in various harsh environments; (4) Under a variety of complex driving conditions, the wheel hub motor should have strong anti-interference ability and high control accuracy.DC motors, induction motors, permanent magnet synchronous motors and switched reluctance motors have been widely used in electric vehicle drive systems. Compared with other drive motors, permanent magnet synchronous motors have the advantages of small size, light weight, fast response and high efficiency. In addition, in addition to high power density, high torque density and high efficiency, permanent magnet synchronous motors also have unique weak magnetic expansion capabilities. Permanent magnet synchronous motors are increasingly used in electric vehicle drive systems. Permanent magnet synchronous motors can meet the above-mentioned technical requirements of wheel hub motors. Therefore, permanent magnet synchronous motors are the best choice for electric vehicle wheel hub motors.2.2. Hub motor drive formAccording to the type of drive motor rotor, hub motors are divided into two categories: high-speed inner rotor motors and low-speed outer rotor motors.2.2.1 Inner rotor hub motorThe maximum speed of a high-speed inner rotor hub motor is 15,000 r/min. In order to meet the actual wheel speed requirements, it needs to be used in conjunction with a reduction device to achieve the purpose of reducing speed and increasing torque. The inner rotor hub motor does not have high requirements for the motor, but the introduction of a reduction mechanism makes the hub motor structure complicated and increases the unsprung mass of the vehicle. In addition, the reduction mechanism wears quickly, which can easily lead to defects such as shortened service life of the hub motor and difficulty in maintenance.Japan has conducted in-depth research on high-speed inner rotor hub motors. Electric vehicles such as ECO developed by Keio University and other institutions, UOT March II developed by the University of Tokyo, ColtEV developed by Mitsubishi, Colt KAZ developed by Keio University, and FINE-T developed by Toyota all use planetary gears as the reduction mechanism of inner rotor hub motors. The electric drive vehicles of QinetiQ Company in the UK are equipped with reduction gear boxes as the reduction mechanism of hub motors. In addition, the Suzuki Swift electric vehicle Q'mo developed by NTN Company uses cycloidal gears as the reduction mechanism of hub motors. Michelin Company of France has developed an active wheel for electric vehicles, which integrates components such as drive motors, active suspension, suspension motors and disc brakes. Due to the superior performance of Michelin's active wheels, the four-wheel drive sports car Venturi Volage developed by the French sports car company Venturi uses this active wheel technology. The inner rotor hub motor developed by Michelin Company is shown in Figure 1.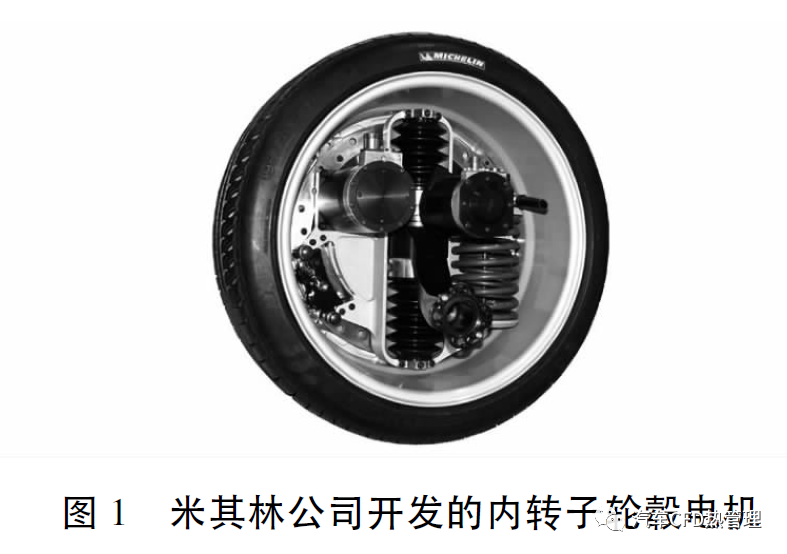
The parameters of the inner rotor hub motors of some of the above electric vehicles are shown in Table 1.2.2.2 External rotor hub motorThe low-speed outer rotor hub motor drives the wheels directly without the need for a reduction mechanism. The maximum speed of the outer rotor hub motor is 2000 r/min. Compared with the inner rotor hub motor, the outer rotor hub motor has a simple and compact structure, a reduced axial size, and further improved transmission efficiency. However, when the car starts and climbs a slope, the motor torque demand is large, and the resulting large current can easily damage the power battery and permanent magnet.The electric car IZA developed by Keio University and other institutions in Japan, the Lancer Evoluation MIEV developed by Mitsubishi Corporation, the Volvo Recharge C30 and Ford0150 launched by PML Flightlink of the United Kingdom, the GM's S10 developed by General Motors, the Protean Drive launched by Protean Electrics of the United Kingdom, the hub motors developed by Bridgestone of Japan and TM4 of Canada all use the outer rotor hub motor drive method.Compared with foreign countries, the research and development of electric vehicles driven by wheel hub motors in my country started late. Tongji University New Energy Vehicle Engineering Center and other units jointly developed the "Chunhui" and "Dengfeng" series of electric vehicles, with the maximum speed of the wheel hub motor of 510 r/min and the maximum speed of the car of 50 km/h. BYD has developed the ET wheel hub direct-drive pure electric vehicle, with the maximum speed of the wheel hub motor of 5500 r/min and the maximum speed of 165 km/h. Chery Automobile Company developed and displayed the "Riich" X1 electric vehicle at the Shanghai Auto Show, with the maximum power of the wheel hub motor of 166 kW and the maximum torque of 1650 N·m. In addition, Guangzhou Automobile Group launched the "Trumpchi" electric vehicle at the Guangzhou Auto Show, using the wheel hub motor of Protean Electric, with a maximum power of 83 kW and a maximum torque of 825 N·m. Domestic automobile manufacturers, universities and research institutes have a certain ability to develop electric vehicles, but the research on wheel hub motor drive technology is still immature, and there is still a big gap compared with foreign advanced technology. Therefore, conducting research in the field of electric vehicle hub motors, enhancing awareness of independent innovation, developing hub motor drive technology with independent intellectual property rights, and improving the mass production capacity of core components of electric vehicles in my country are of great practical significance for promoting the development of the electric vehicle industry.3. Research overview and existing problems of wheel hub motor drive technologyAlthough the wheel hub motor drive technology has a series of advantages, the introduction of the wheel hub motor has caused problems such as the increase in the unsprung mass of the vehicle, the negative effect of vertical vibration, and the torque pulsation of the wheel hub motor, which have a crucial impact on the vehicle's dynamic performance and safety performance. The above problems restrict the development of the wheel hub motor drive technology. In response to the above problems, domestic and foreign scholars have conducted a lot of research on reducing the unsprung mass, suppressing the negative effect of vertical vibration, and improving the torque characteristics of the wheel hub motor.3.1. Reduce unsprung massIn-wheel-driven electric vehicles not only eliminate the engine, clutch, transmission, drive shaft and other devices, but also install a hub motor inside the wheel rim, resulting in a reduction in sprung mass and a significant increase in unsprung mass. Excessive unsprung mass affects the ride comfort of the car, which is more obvious for vehicles traveling at high speed on roads with poor road conditions. At present, the main methods for reducing unsprung mass at home and abroad are lightweight design and unsprung mass conversion.(1) Lightweight and integrated design. Lightweight design mainly refers to the selection of suspension, rims and other components made of aluminum or magnesium alloy, or the structural integration of motors, rims, hubs, hub bearings and brake systems. At present, BMW, Audi A8 and other cars widely use aluminum alloy suspension or hubs, which greatly reduces the weight of the vehicle. Tongji University has highly integrated the suspension and electric wheel module, which greatly reduces the vehicle chassis structure. The new rare earth material neodymium iron boron is increasingly used in the production process of hub motors. The disc-type coreless permanent magnet hub motor designed by Wang Xiaoyuan et al. has high power density, output torque and wide speed regulation range. Chai Feng et al. combined permanent magnet materials with soft magnetic materials to design axial flux reverse salient permanent magnet hub motors, which solved the problem of weak magnetic field speed expansion capability and improved the utilization rate of permanent magnet and hub space. The literature proposes an integrated design method for hub motors, rims, hubs and other components to achieve the purpose of improving the vertical dynamics performance of the vehicle.(2) Transfer of unsprung mass. Yu Zhisheng pointed out that when the ratio of sprung mass to unsprung mass decreases, the vehicle smoothness index performance decreases near the wheel resonance peak, and the relative dynamic load of the wheel changes greatly, so the relative dynamic load of the wheel must be reduced. Hredzak et al. designed a disc hub motor, which converted the motor stator mass into the vehicle sprung mass and realized the transfer of unsprung mass. The literature converts the hub motor suspension element into the absorber mass, which improves the ride smoothness of the whole vehicle. Zhao Yan'e et al. proposed a new hub motor layout, which uses a vibration reduction device to realize the transfer of the hub motor stator mass from sprung mass to unsprung mass. However, this method is prone to cause eccentricity between the hub motor stator and rotor, thereby affecting the vehicle dynamics performance. Jin LQ et al. introduced a universal joint to convert the wheel-side motor from unsprung mass to sprung mass, reducing the influence of the wheel-side drive form on the vehicle mass distribution, improving the vehicle smoothness and reducing the tire dynamic load. Luo Yutao and Tan Di elastically isolated the wheel hub motor from the unsprung mass, converted the wheel hub motor into a mass connected in parallel with the sprung mass, and increased the ratio of the sprung mass to the unsprung mass. The structural schematic diagram of the new wheel hub motor they designed is shown in Figure 3. Figure 3 (a) shows the structure of the inner rotor wheel hub motor, which contains a reduction mechanism; Figure 3 (b) shows the structure of the outer rotor wheel hub motor, which does not contain a reduction mechanism.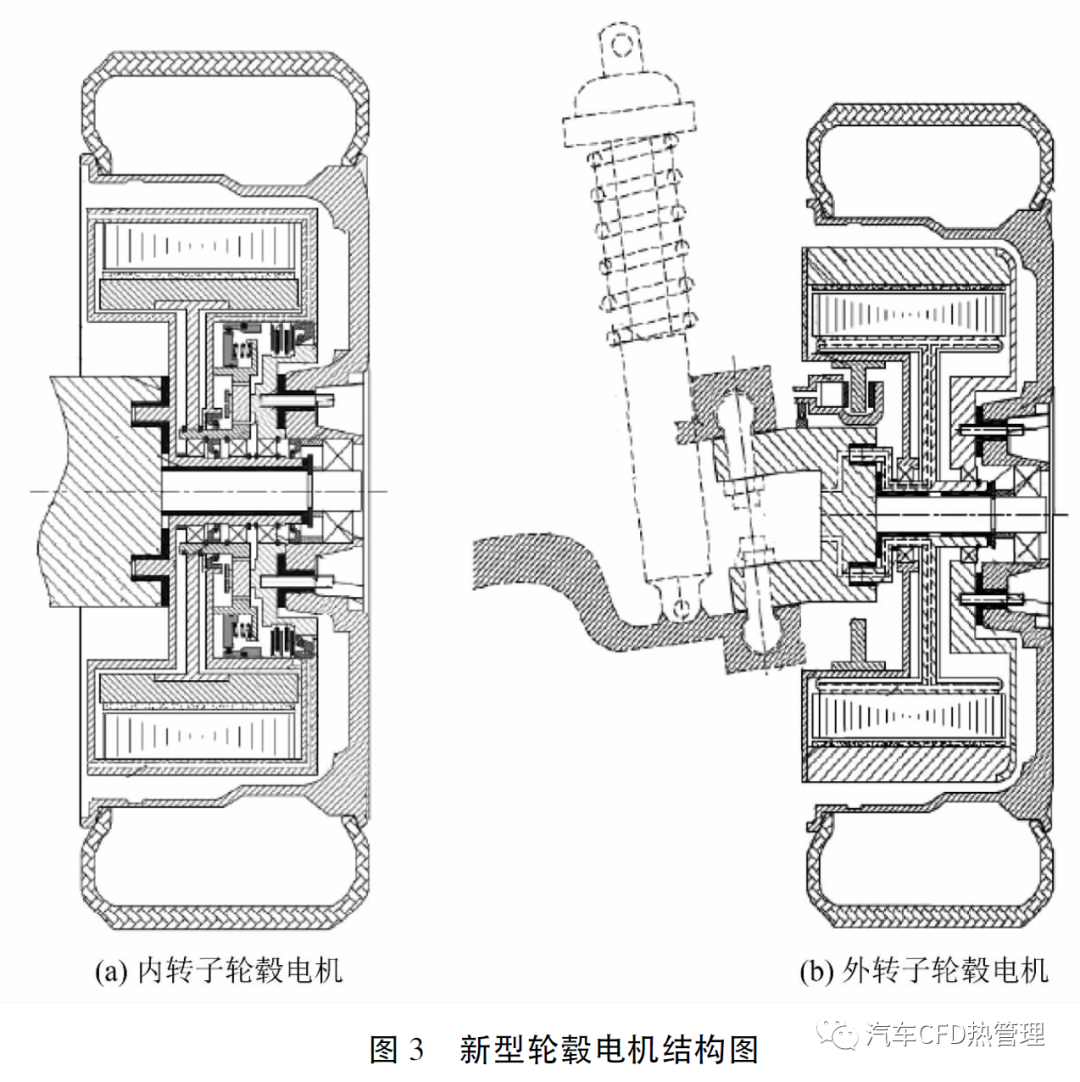
3.2. Suppressing the negative effects of vertical vibrationThe increase in the unsprung mass of the vehicle and the moment of inertia of the wheels will cause the negative vertical vibration effect of the wheel hub motor, which will have a bad impact on the ground contact performance of the tire and the driving smoothness of the car. In severe cases, it will cause the car to skid or roll over, greatly reducing the safety of the car. In order to improve the comfort of wheel hub driven electric vehicles, it is necessary to find a way to solve the negative vertical vibration effect of the car. At present, the methods of suppressing the negative vertical vibration effect of wheel hub motors at home and abroad are as follows.(1) Design of dynamic vibration absorber and vibration reduction device. The literature proposes a wheel-side drive system design method that uses a dynamic vibration absorber to convert the wheel hub motor into a vibration absorber mass element, which greatly improves the smoothness and safety of the vehicle. The literature achieves improved vehicle driving smoothness by installing a dynamic vibration absorber on the wheel steering knuckle. Ma Ying et al. designed a vibration reduction device between the wheel hub motor and the wheel so that part of the mass of the wheel hub motor is suspended in the wheel, and the wheel hub motor serves as a dynamic vibration absorber for the vehicle body and the wheel at the same time, as shown in Figure 4. This method improves the vehicle driving smoothness to a certain extent, but the design of the spring and damping vibration absorber in the wheel hub space is difficult, and the vibration absorber parameters need to be recalculated when the mass of the vehicle body, wheel, and wheel hub motor changes.(2) Suspension system improvement. The active suspension, semi-active suspension, and passive suspension systems can be improved, new suspension structures can be designed, and low-stiffness, low-slope resistance tires can be selected. Wang Yanyang et al. designed a feedback-type magnetorheological semi-active suspension shock absorber, as shown in Figure 5. The power flow method was used to analyze the energy-feeding characteristics of the energy-feeding suspension. The results showed that the energy-feeding characteristics of the energy-feeding magnetorheological semi-active suspension were improved.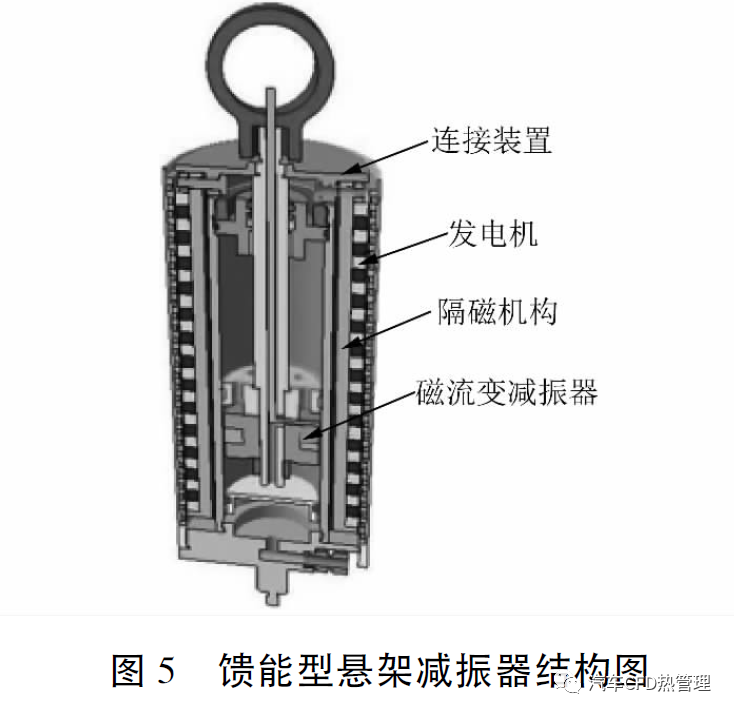
With the continuous emergence of new technologies and new products, traditional suspension will eventually be replaced by new intelligent suspension. The eCorner electric wheel car developed by Siemens and the active wheel technology launched by Michelin combine the hub motor with the intelligent suspension, effectively improving the driving smoothness and handling stability of electric vehicles. The development of a new intelligent suspension system and control strategy for electric vehicles driven by hub motors with independent intellectual property rights has not only become an important development direction for electric vehicle research, but also has important theoretical significance and engineering application value for my country's "13th Five-Year Plan" development plan for new energy vehicles.3.3. Reduce the torque pulsation of the hub motorA lot of research has been done at home and abroad, and the results show that the torque pulsation of the hub motor is the main factor affecting the smoothness of the vehicle's ride. According to the different mechanisms of torque pulsation, the torque pulsation of the hub motor is mainly caused by the cogging torque fluctuation and the commutation torque fluctuation. Therefore, the suppression of the torque pulsation of the hub motor is mainly carried out from the aspects of the optimal design of the hub motor and the motor control strategy. Many experts and scholars at home and abroad have conducted in-depth research on suppressing the torque pulsation of the hub motor.Prabhu S believes that the vibration intensity of the hub motor is affected by the shape of the stator and the rotation period of the motor. When the vibration amplitude is small, it can be simplified to the linear superposition of modes. Rojas A et al. studied the measures to solve the deterioration of vehicle smoothness and handling stability by using different types of suspension under different hub motor driving torques, and explored the relationship between the dynamics, safety and comfort of wheel-side drive electric vehicles. Yu Zengliang et al. studied the in-vehicle noise of hub direct-drive electric vehicles and believed that the fluctuation of wheel circumferential torque caused by the torque pulsation of the hub motor is the main factor causing the vibration of the powertrain. Zuo Shuguang et al. studied the vibration response of the electric wheel under high-frequency torque signal excitation and analyzed the relationship between tire ground force and torque pulsation. Tan D et al. applied the Maxwell stress tensor method to derive the analytical expression of the electromagnetic force of the hub motor, and substituted it into the vehicle suspension dynamics equation to calculate the suspension vibration response characteristics under electromagnetic composite excitation. The time domain and frequency domain responses of the relative displacement of the stator and rotor under time-varying eccentricity are shown in Figure 6.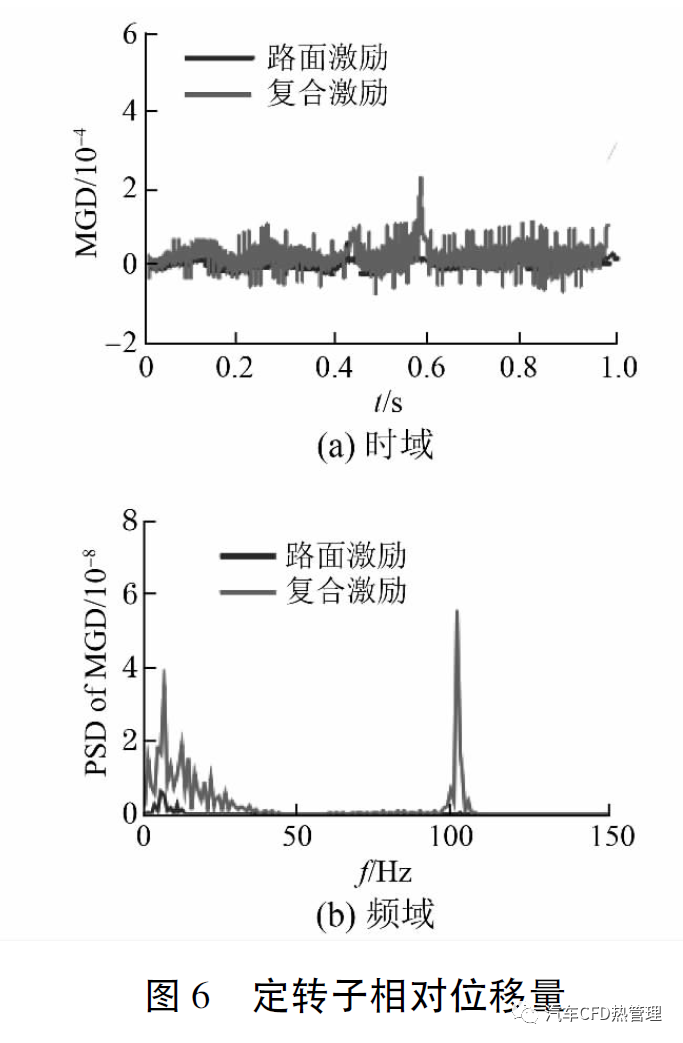
In addition, the torque pulsation of the hub motor can be reduced by studying factors such as current harmonics, rotor eccentricity, and stator natural frequency.4. Development trend of wheel hub motor drive technology(1) Lightweight. The drive system of a hub-driven electric vehicle consists of a hub motor, brake, rim, hub, tire, transmission and bearing. Each component can be lightweighted by optimizing size, structure and selecting new materials. The lightweight of the hub motor can be achieved by increasing power density and optimizing the motor structure design.(2) Integration. In order to effectively apply the wheel hub motor drive technology to electric vehicles, it is necessary to modify the existing electric vehicle chassis, adjust the vehicle suspension structure and parameters, integrate the wheel hub motor with the suspension, maintain the ratio of sprung mass to unsprung mass, develop a vehicle chassis suitable for wheel hub motors, and give full play to and reflect the superiority of wheel hub motors. The integrated wheel hub motor drive system that integrates key components such as wheels and wheel hub motors is a key technology that needs to be studied in the future.(3) Wheel hub motor cooling technology. The operating conditions of electric vehicles are complex and changeable. The wheel hub motor is installed in a narrow wheel, which is prone to insufficient cooling and motor overheating. When the car brakes, the brake generates a lot of heat, which will be directly transferred to the motor, causing the motor to overheat. When the permanent magnet material reaches above 140°C, it will cause demagnetization, which will directly affect the performance of the whole vehicle. At present, the wheel hub motor cooling system is not perfect enough. It is necessary to develop a suitable wheel hub motor cooling system to cool the rotor and stator respectively through air cooling, water cooling, etc., so as to avoid demagnetization of the permanent magnet material.(4) Demagnetization suppression technology for permanent magnet materials. Permanent magnet hub motors with higher energy density represent the future development direction of hub motors. In addition to thermal demagnetization, permanent magnet hub motors will also experience demagnetization under high-intensity vibration conditions, which is determined by the permanent magnet materials. Developing permanent magnet materials that are resistant to impact and vibration and suppressing the demagnetization of permanent magnet hub motors to a greater extent are the key points of future research.(5) Torque pulsation suppression technology. Solve the torque pulsation problem of the hub motor under the coupling of multiple fields such as electromagnetic, temperature, and stress, correct and compensate the motor parameters, reduce the motor torque fluctuation, improve the hub motor speed and torque control accuracy, and improve the hub motor control performance. The application of hub motor drive technology in different types of vehicles is increasing. Improving the speed and torque coordination control performance between multiple hub motors under different operating environments and different working conditions is the future development direction of hub motor drive technology.(6) Electronic differential control technology. Since the mechanical transmission part of traditional vehicles is eliminated, the wheel hub motor directly drives the vehicle. When the vehicle speed exceeds a certain value, the vehicle will become obviously unstable. At present, electronic differential control technology at home and abroad is still in the initial accumulation stage, which requires that the electronic differential control technology of wheel hub motors must be tackled so that the electronic differential technology level exceeds that of traditional mechanical differentials.(7) Sensorless control technology. Although the rotor information of the hub motor can be obtained conveniently and accurately through mechanical sensors, the rotor's rotational inertia is also increased. In addition, mechanical sensors not only have defects such as poor sensor sensitivity under harsh working conditions and commutation errors caused by inaccurate installation, but also increase system costs and maintenance difficulties. Traditional mechanical sensors can no longer meet the requirements of precise control of permanent magnet hub motor speed and torque. In recent years, with the development of motor technology and the continuous improvement of sensorless control technology, sensorless control of electric vehicle hub motors will inevitably become the development direction of hub motor drive technology.(8) Coordinated control technology. When wheel hub motors are applied to vehicles in pairs (at least one pair), not only is it required that the performance of the wheel hub motors on the left and right sides of the vehicle body be consistent, but also that the torque of multiple motors be able to be synchronously coordinated to ensure that the vehicle can drive safely under various driving conditions. In addition, the vibration acceleration of the wheel hub motor is relatively large during driving. In order to extend the service life of the wheel hub motor, it should have good durability.(9) Intelligence. With the development of intelligent networked vehicle technology, the environmental perception ability of new energy vehicles is constantly enhanced, and the control algorithm is constantly improved. In-wheel direct-drive electric vehicles will develop in the direction of networking, intelligence, and unmanned operation. Future vehicles can be called "wheeled mobile robots." This development trend will inevitably force the key technologies of in-wheel motor drive systems (such as speed regulation, torque distribution, braking control, electronic differential control, energy management control strategy, cooling system control, bus control, etc.) to develop in the direction of intelligence, electronization, and informationization.(10) Low cost. In new energy vehicles, wheel hub motors have overturned the power system of traditional vehicles and are a completely new driving method. From a research perspective, wheel hub motors make people very optimistic about the development of future driving technology. However, due to its high cost, large-scale commercial application of wheel hub motor driving technology has not yet been realized. Therefore, reducing the cost of wheel hub motor driving technology will definitely enhance the market competitiveness of this technology.In-wheel motor drive technology represents an important development direction for new energy vehicle drive systems, and has important theoretical significance and engineering application value for promoting the development of the pure electric vehicle industry. However, in-wheel motor drive technology still faces many key technical problems that need to be solved, and there is still a large gap between China and foreign countries in terms of in-wheel motor drive technology. If large-scale commercial applications of in-wheel motors are to be realized in the future, it is necessary to overcome the bottleneck limitations of in-wheel motor drive technology and make breakthroughs in key technical fields of in-wheel motor drive systems. Only in this way can in-wheel motors have broad market application prospects.