How to choose a motor for a robot?
This article mainly discusses the selection method of DC motor.
01
Motor requirements
【Introduction to DC Motor】
There are many kinds of DC motors on the market. According to incomplete estimates, there are thousands of motor manufacturers in China alone. Not to mention Japan, Germany and other established motor production powers. Even for a small DC motor, it has a complex internal structure and a lot of product information. Here, we only consider the requirements for motor performance from the perspective of robots.
The choice of motor is often a compromise between our requirements for motor performance and the price we can accept. Therefore, in the process of motor selection, we need to consider all the parameters of the motor as a whole, select the parameters that are important to us, and choose the appropriate motor based on our needs.
For a motor, it often has multiple operating characteristic curves. Here we will list some of the most important characteristics and then explain them. For a motor, from the perspective of robot drive, our main concerns are:
a) Operating voltage - For a motor, there may be multiple voltage parameters; the most commonly used is the rated voltage under continuous operation conditions; some motors can operate at a speed and torque above the rated voltage, but after running for a period of time, they may have local overheating problems; that is, partial overvoltage can only be operated for a short time, not for a long time;
b) Speed – the speed at which the motor rotates, usually expressed in revolutions per minute, but sometimes also expressed in radians per second or degrees per second;
c) Torque – the ability of a motor to change its rotational speed; for example, when a wrench is used to turn a screw, the torque of the wrench causes the screw to rotate; in the field of robotics, torque is generally used to make a robot move or to make a robotic arm perform various actions; torque is equal to the product of force and lever arm, and its unit is Nm;
d) Current - For a motor, there may be multiple current parameters, such as no-load current , rated current, and locked-rotor current;
e) Physical parameters - such as motor size, motor shaft size, cross-sectional dimensions, and location of fixing holes;
f) Other parameters - some motors also provide other components, such as encoders, brakes, gearboxes, bases, etc.
【DC reduction motor】
Obviously, the DC motor is powered by a direct current, so it can be powered by a battery; this is one of the reasons why DC motors are widely used in robots; small DC motors may vary in size, but the basic parameters are generally the same; the direction of rotation of a DC motor can be changed by changing the sign of the supply voltage;
Small DC motors generally operate in the high-speed and low-torque operating range, which is inconsistent with the motor drive requirements in robots; the field of robotics usually requires motors to operate in the low-speed and high-torque range; therefore, in order to reduce the motor speed while increasing the motor speed, a shaft system, i.e., a reducer, is generally added between the motor and the output shaft; by combining different reducers, the motor can obtain different rated speeds and rated torques; many DC motors currently available on the market already have reducers when they leave the factory, and are therefore often called DC reduction motors;
The advantages of reduction motors are : easy use, high output torque, low speed, and a wide range of options.
The main disadvantage is the low precision. Even if the same batch of reduction motors are produced by the same manufacturer, the output of the reduction motors may be different if the same voltage or current is applied. Therefore, in robot applications, it is generally necessary to introduce speed closed-loop control when controlling the reduction motors, and open-loop control cannot be used.
Here are some common factors to consider when choosing a geared motor:
a) Versatility - Generally speaking, the more versatile a motor is, the cheaper it is;
b) Working voltage: Generally, the working range of small reduction motors is 6-24V;
c) Output torque: Generally, the output torque of a small reduction motor is between 0.1-0.5Nm; it can generally be used to drive a robot weighing 20-30kg;
d) Speed - The motor speed and tire size determine the maximum speed of the robot. In general, the tire size of wheeled robots is between 5-20cm, with 6-10cm being the most common.
Although most reduction motors can rotate forward and reverse, some can only rotate in one direction. In addition, although reduction motors generally have many parameters, from the perspective of robots, we generally do not pay attention to many parameters such as the moment of inertia of the motor shaft . The most important parameters of reduction motors for robot applications are motor speed, torque and rated voltage.
The following is an example of a reduction motor on Taobao:
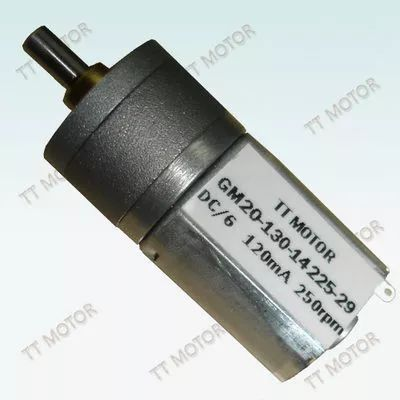
Its parameters are:
-
Brand: ** Installation method: horizontal Number of levels: 3 Tooth surface hardness: hard tooth surface Layout form: coaxial
-
Reduction ratio: 103 Rated voltage: 24V Rated speed: 131RPM
-
No-load speed: 155RPM Rated torque: 0.014Nm Peak torque: 0.075Nm
Motor size:
-
Motor diameter: 20mm Motor length: 45.5mm Output shaft diameter: 4mm
-
Output shaft step height: 0.5mm Output shaft length: 11mm
Through the product introduction, we can see the product model, control speed, rated speed, rated torque, etc. Before further discussing the reduction motor, let's first determine the specific requirements for motor parameters in the robot.
【Motor parameter requirements】
First, we need to determine the robot's operating environment, such as whether the robot will mainly operate outdoors or indoors, on smooth or rough surfaces, whether it needs to climb slopes, etc. Secondly, we need to determine the robot's specific mechanical parameters, such as size, weight, etc. Next, we need to determine some of the robot's operating parameters, such as operating speed and torque.
The motor drives the robot's tires to make the robot move. The robot's movement speed mainly depends on the motor speed and the tire diameter. The motor's rotation speed depends on the input voltage and its load torque. Under the same supply voltage, the motor's rotation speed is higher when it is unloaded than when it is loaded. Under the same supply voltage, the greater the output required by the motor, the lower the motor speed and the greater the motor current. When the output increases to a certain level, the motor will stop rotating, that is, stall. At this time, the motor current is the largest. If the motor is stalled for a long time, the motor temperature will rise, and in severe cases, the motor will be damaged.
The relationship between the robot tire speed and the motor rotation speed is:
V=0.02*pi*w*R/60;
Where: V is the robot running speed (m/s);
w is the motor rotation speed after passing through the reducer (rpm); R is the motor radius (cm);
Assuming that we require the average speed of the robot to be Vavg, then the required speed of the reduction motor is:
w=60*Vavg/(0.02*pi*R) (1)
Motor torque requirements:
The motor torque requirements are mainly related to the friction and slope of the ground on which the robot is running.
Assuming that the friction coefficient of the robot is C and the mass of the robot is m (kg), the torque required for the robot to run at a constant speed on the ground is:
T=0.01Ff*R=0.01C*mg*R;
Where Ff is the friction force (N), R is the tire radius (cm);
In addition to uniform motion, we may also specify the robot's maximum climbing angle theta and the required maximum acceleration a. In this case, the two can be equivalent to friction. In this case:
C = C0 + sin (theta) + a / g;
Among them, C0 is the inherent ground friction coefficient, theta is the maximum climbing interpretation, a is the maximum acceleration, and g is the gravitational acceleration;
T = 0.01CmgR; (2)
The above formulas 1 and 2 are the methods for selecting the motor speed and torque of the robot.
02
Motor operating conditions
When the DC motor starts to be powered, the motor shaft has not yet started to rotate. At this time, the click is in a stalled state, the maximum motor current is iS, and the torque generated by the motor is also the largest; therefore, the motor starts to rotate. At this time, as the motor speed increases, the motor back EMF increases, the motor current decreases, and the torque decreases. When the motor torque is equal to the load torque, the motor reaches a balanced state, which is the balanced motor speed.
The motor balance state means that the motor torque is equal to the load torque. In the robot, the load torque mainly includes factors such as friction, climbing, and acceleration.
In the field of robotics applications, we are often more concerned about the maximum speed that the motor can achieve under different load conditions.
For example, under no-load conditions, the maximum speed that the motor can reach is w0; under load conditions, the speed that the motor can produce when it is stalled is the maximum torque, and the stall torque is Ts;
Under other conditions, the motor operates on a linear line between the two;
That is, if the load torque is T, then at this time, the maximum speed of the motor is:
w=w0*(1-T/Ts);
If the motor requires a maximum speed of w, then the maximum torque that the motor can generate is:
T=Ts*(1=w/w0);
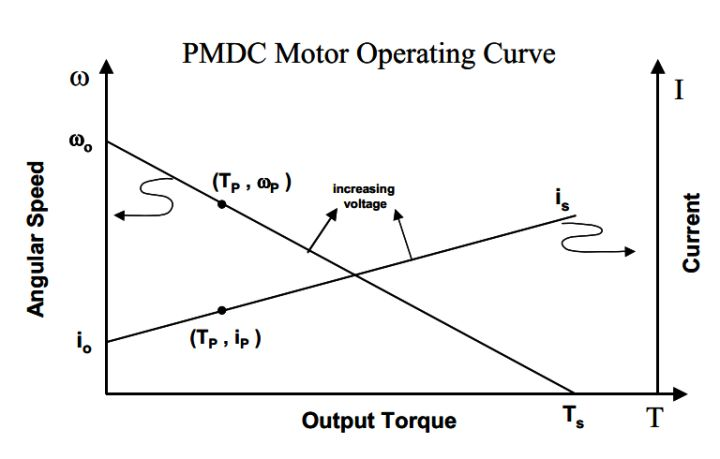
The above figure reflects the linear relationship between the maximum speed and maximum torque of the motor, and between torque and current.
The maximum no-load speed of the motor is w0, and the no-load current is i0; as the load torque increases, the motor speed decreases linearly and the current increases until the load torque reaches the maximum torque and the motor is blocked. If the motor torque continues to increase, the motor will be in the power generation state.
When the motor torque is T, the motor current is:
i=i0+(is-i0)*T/Ts;
Where i0 is the no-load current, is is the locked-rotor current; Ts is the locked-rotor torque;
After the above discussion, we can draw the conclusion that when choosing a reduction motor, the following parameters should be considered first:
Motor operating voltage, no-load speed, speed at a certain torque, and current at a certain torque.
1. Motor operating voltage: When selecting the motor operating voltage, we need to choose a motor operating voltage that corresponds to the robot battery. Most motor operating voltages are 6V, 12V, and 24V. For robots with a general size of 15cm-30cm, NiMH batteries are generally used, and for large robots, lead-acid batteries are generally used; NiMH batteries are generally standard AA, C, and D sizes, and the voltage ranges from 3.6 to 48V. For 12V motors, 7.2V or 9.6V is generally used for power supply; for 24V motors, 3*9.6V is generally used for power supply.
2. Motor speed: For the estimation of motor speed, we generally choose the motor speed that can meet the conditions under rated voltage and rated torque. For robots with tire sizes between 5-20cm, the motor speed range is generally from 40-300rpm;
3. Motor torque: When selecting motor torque, we generally leave a 50% margin based on the calculation in the previous part; in addition, if there are more than one motor, the motor torque requirement can generally be divided by the corresponding number.
4. Motor current: The motor current will determine the robot's running time. Generally, based on the motor current data, we can roughly evaluate its application range. For example, if a motor current is 0.01A, then for most robot occasions, the motor will be too small; on the contrary, if the motor rated current is 1A, then the motor will be too large;
In addition, when choosing, you also need to pay attention to the size of the robot body to ensure that the motor can be installed. In addition, you also need to choose a suitable position sensor - photoelectric encoder or rotary transformer, etc. according to the control accuracy requirements.
03
Robot Motor Selection Example
Here, we take a mobile robot platform that I am developing as an example to explain the motor selection process in detail.
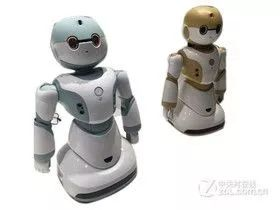
The robot platform is roughly as shown in the figure above. It weighs 4kg and requires a maximum running speed of 1m/s. Two motors drive it to move. The maximum climbing angle is 5 degrees. The motor power supply voltage is 24V and the tire diameter is 65mm.
1. Speed requirement: Speed = 60*Velocity/(PI*d) = 290rpm;
2. Torque requirement: For the motor torque requirement, since the overall system weight is 4kg, assuming the friction coefficient is 0.03, the click torque is: T=Ff*R=(0.03+sin5)*4kg*9.8kgm/s^2*32.5*10^-3m=100mNm; share it on the two motors, and the torque of each motor is 50mNm.
The preliminary parameters of the reduction motor are: torque: 50mNm, speed 290rpm.
The following are some motors selected on Taobao:
The final motor selection can then be determined based on other mechanical or price factors.