Materials are the mother of industry. The birth of new materials is closely related to the adjustment of economic structure. The progress of many industries such as industry, communications and consumption cannot be separated from the progress of materials . Therefore, in recent years, the development of new materials has also attracted the attention of the world's industrial powers. Based on the national conditions and industrial development characteristics of each country, new materials development strategies and incentive policies have been launched, and projects such as materials infrastructure construction have been launched. my country has also successively introduced A range of policies and support programmes. At present, from the perspective of industrial development trends, policy support, industrial innovation, industrial correlation and diffusion effects, the new materials industry is an important industry development direction in the future.
Where is the "new"? The so-called new materials refer to the application of new ideas, new technologies, new processes, and new equipment to significantly improve the performance of traditional materials or to have new functions, or to design and develop functions or special functions that traditional materials do not have. s material. For example, ordinary steel becomes stainless steel by adding nickel; and sand, which was originally mainly used as a building material, is processed into silicon wafers, the main raw material for semiconductor devices and solar cells.New materials can be subdivided into advanced steel materials, advanced non-ferrous metal materials, advanced new petrochemical and chemical materials, advanced inorganic non-metallic materials, high-performance fibers and products and composite materials, cutting-edge new materials, new material-related services, etc. It seems strange at first glance, but in fact it is closely related to our lives. This article will mainly explore the application prospects of new materials in the motor industry.
In recent years, with the increasing market demand for miniaturization and lightweight of electric vehicle drive systems and high efficiency of drive motors, higher speed requirements have been put forward for drive motors. The application of carbon fiber materials exactly meets the demand for high-speed driving motors.
Figure 1 Carbon fiber composite
Carbon fiber refers to high-strength and high-modulus fibers with a carbon content of more than 90% . High temperature resistance ranks first among all chemical fibers. It is made of acrylic fiber and viscose fiber as raw materials and is oxidized and carbonized at high temperature. It is an excellent material for manufacturing high-tech equipment such as aerospace and aviation.Carbon fiber has the characteristics of high temperature resistance, friction resistance, thermal conductivity and corrosion resistance. It is fibrous in appearance, soft and can be processed into various fabrics. Because its graphite microcrystalline structure is preferentially oriented along the fiber axis, it has high strength along the fiber axis. and modulus. Carbon fiber has a low density, so its specific strength and specific modulus are high. The main use of carbon fiber is as a reinforcing material compounded with resin, metal, ceramics and carbon to produce advanced composite materials. Carbon fiber reinforced epoxy resin composite materials have the highest specific strength and specific modulus among existing engineering materials.Motor rotor: The rotor structure of the motor must overcome the centrifugal stress, generally using a metal sheath, the structure of the rotor itself (such as the fish skeleton of IPM, the rotor structure of IM), etc. Carbon fiber can be used to make motor rotors, especially in applications that require high speed rotation and lightweighting. The carbon fiber rotor has high strength and stiffness, allowing it to withstand centrifugal and inertial forces during high-speed rotation. In addition, the low density of carbon fiber can reduce the mass of the entire motor system, thereby improving energy efficiency and responsiveness.It can be seen that, whether in ultra-high-speed motors or high-power motors, foreign research on high-speed motors was relatively early, the technology is relatively mature, and it has begun to develop towards serialization and industrialization. Domestic research on ultra-high speed and high-power high-speed motors has achieved certain results, but above 100kW level (45×103r/min) and MW level (15×103r/min), the industrialization of high-power high-speed motor systems has just begun. , there is still a certain gap compared with foreign countries.
Driven by the pursuit of smaller size and higher power, the speed of motors has been rising, from two to three thousand revolutions in the early days to tens of thousands or even hundreds of thousands of revolutions. Higher speeds have improved power density and raw material utilization. Therefore, high speed is a strong trend. Taking new energy drive as an example, the maximum speed of the first-generation product launched by Toyota Prius was only 6,000 r/min, and the speed of the fourth-generation product reached 17,000 r/min. High-speed and ultra-high-speed applications have broad prospects but at the same time bring extremely high challenges to motors, which can be summarized into the following six categories: heat dissipation, motor selection, rotor structure, vibration and noise, efficiency, and bearings.
Figure 2 Motor rotor
Magnetic bearings: Carbon fiber materials are widely used in magnetic bearings. Magnetic bearings use magnetic fields to levitate and support the rotor, reducing mechanical contact and friction. The high magnetic permeability and low resistance properties of carbon fiber material make it an ideal choice for magnetic bearings because it can provide good magnetic field response and low energy loss.
Figure 3 Magnetic bearing
Structural components: Carbon fiber composites can be used to make structural components of electric motors, such as housings, end caps and brackets. These components need to be lightweight and strong to provide adequate structural support and protect internal motor components. The high strength and low density of carbon fiber composites make them ideal for manufacturing these components. Cooling system: In high-speed motors, the effectiveness of the cooling system is critical to maintaining stable operation of the motor. Carbon fiber has high thermal conductivity and can be used to manufacture heat sinks and fins in cooling systems. The thermal conductivity of carbon fiber can help transfer heat quickly and keep the temperature of the motor within an acceptable range, thus improving the efficiency and life of the motor .In general, the application of carbon fiber in high-speed motors mainly focuses on providing lightweight, high strength and good thermal conductivity. These characteristics can improve the performance, efficiency and reliability of motors and promote the development of high-speed motor technology.
The motor is an indispensable and important component in modern industry, and the performance of the motor often depends on the quality of the stator. Traditional motor stators are usually made of silicon steel sheet materials. Additive manufacturing technology is an emerging manufacturing technology that can produce more complex structures and greatly shorten the product development cycle. Fe-3wt.%Si ferrite material has excellent magnetic properties and mechanical properties, which can greatly improve the performance of the motor. At the same time, its resistivity is lower than traditional silicon steel sheets and its electrical properties are better. Therefore, it is of great significance and application value to use additive manufacturing technology and Fe-3wt.%Si ferrite materials to manufacture motor stators.Recently, researchers such as Tej N. Lamichhane from Oak Ridge National Laboratory in the United States conducted research on additive manufacturing technology and Fe-3wt.%Si ferrite material to manufacture motor stators. This technology can not only realize the manufacturing of complex-shaped stators , Offers greater flexibility and customizability. At the same time, it can greatly shorten the product development cycle and improve production efficiency. This research is supported by the U.S. Department of Energy and is a very promising technology research.The stator is printed using selective laser melting technology , then processed into thin layers and finally laminated to create the stator core. The study used Selective Laser Melting (SLM) technology to print Fe-3wt.%Si ferrite material. SLM technology is an additive manufacturing technology based on powder materials. The powder materials are melted and stacked layer by layer through a laser beam to finally form the required three-dimensional structure. Compared with traditional manufacturing methods, SLM technology has higher flexibility and customizability, and can manufacture more complex structures. Fe-3wt.%Si ferrite material is a material with excellent magnetic properties and mechanical properties, which can greatly improve the performance of the motor. At the same time, the resistivity of this material is lower than that of traditional silicon steel sheets, and its electrical properties are better. The application of this material can bring higher performance and better efficiency to the motor manufacturing industry.
Figure 4 3D printed Fe-3Wt.%Si stator
The study also tested the performance of the printed materials and compared them with traditional silicon steel sheets. The results show that the magnetic permeability of the stator is more than 20% higher than that of traditional silicon steel sheets, and the magnetic saturation induction intensity is also more than 10% higher than that of traditional silicon steel sheets. At the same time, the strength and hardness of the stator are much higher than traditional silicon steel sheets, the resistivity is also lower than traditional silicon steel sheets, and the electrical properties are better. This performance improvement can bring higher efficiency and better performance to the motor manufacturing industry.
2.2 Oriented steel
Due to its obvious magnetic anisotropy, oriented silicon steel material has extremely low loss and high magnetic permeability especially along the direction of orientation, but has poor electromagnetic properties and high iron loss in other directions, so it is mainly used for applications with a single magnetization direction. On various transformers, mutual inductors and other equipment. For axial flux motors with a single magnetization direction in the stator core, oriented silicon steel has entered the researchers' field of vision again.
Figure 5 Axial flux hub motor
Figure 6 Schematic diagram of the magnetic circuit of an axial flux motor
The three materials studied are non-oriented steel, oriented steel and soft magnetic composite materials, which are more typical ones. Their brands are M350-50A, B20R070 and SMC-700HR5P respectively.Axial flux motors using non-oriented steel, oriented steel and SMC materials were analyzed from different angles and the following conclusions were drawn:
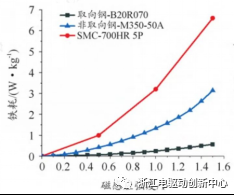
(a) Iron loss curve (50Hz)
Figure 7 Iron loss performance curve
Figure 8 Variation curves of stator core loss with rotation speed for three materials
Table 1 M350-50A, B20R070 and 700HR5P motor parameters
When oriented steel is used as the stator material, the motor magnetic field is significantly different from the other two materials. The magnetic fields of non-oriented steel and SMC motors are basically similar, with only certain differences in intensity.
When the three types of motors are excited by small currents, the output torque is basically the same (the SMC motor is slightly smaller). However, when excited by large currents, due to the different saturation points of each material, the oriented steel motor has the strongest anti-saturation ability and a larger output torque.Comparing the iron loss of each motor, the SMC motor has the largest iron loss, followed by the non-oriented steel motor. The YASA wheel motor using oriented steel material has the smallest iron loss in the motor speed range due to the special magnetic circuit structure combined with the loss characteristics of oriented steel. uneven distribution.In the temperature field , since the thermal conductivity of the stator core made of laminated non-oriented steel and oriented steel is small along this direction, the temperature at the end of the outer diameter of the core is significantly higher than that of the isotropic SMC core.Finally, after comparing the electromagnetic solutions of the three materials, oriented steel was selected as the optimal stator material for the axial flux motor.