If he motor bearing has failed, what should we do?
Date:2023-10-23 Author:Shandong Xinda Motor Co., Ltd.
Bearings are important components for the operation of electric motors. Based on many years of maintenance experience, the author knows that whether they are properly maintained will directly affect the service life of the bearings and the safe and efficient operation of the electric motors. Therefore, it is very necessary to do a good job in daily maintenance and deal with the faults in a timely manner to avoid the expansion of faults; thereby avoiding burning out the motor and causing greater economic losses.
1. Causes and solutions for abnormal noise in rolling bearings
1. When the motor is running, you can use a screwdriver with the tip against the outer cover of the bearing and your ear close to the wooden handle of the screwdriver to listen for the noise from the bearing. If there is a faint rolling sound from the rolling elements in the inner and outer rings, and the sound is monotonous and uniform, making people feel relaxed, it means that the bearings are in good condition and the motor is running normally. If you hear abnormal noise, you should analyze the cause and deal with it.
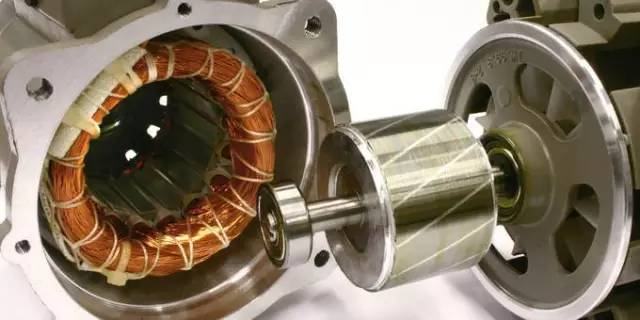
1.1 If you hear obvious rolling and vibration sounds of the rolling elements, it means that the bearing clearance is too large or is severely worn and needs to be replaced.
1.2 If the rolling elements sound hoarse and have a heavy tone, it means that the bearing lubricating grease is too dirty and impurities have invaded. The bearings need to be cleaned with kerosene and replaced with new lubricating oil.
1.3 Irregular impact sounds from the rolling elements indicate that individual rolling elements in the bearing are broken and need to be replaced.
1.4 A sound similar to a whistle, mixed with the rolling sound of rolling elements, indicates that the bearing lacks lubricating oil or the lubricating oil is improperly selected. Clean lubricating oil needs to be added or a suitable lubricating oil needs to be replaced.
2. Causes and treatment methods of rolling bearing heating
2.1 If the motor is left idle for too long, the lubricating grease will deteriorate and harden; new lubricating grease should be replaced.
2.2 If too much or too little lubricating oil is added to the bearing chamber, 1/3-2/3 of the volume of the bearing chamber should be added; and lubricating oil of the same type and brand should be added regularly and quantitatively according to the motor instructions.
2.3 If there are debris in the bearing chamber, the bearing needs to be cleaned with kerosene and replaced with new lubricating oil.
2.4 If the bearing wear is excessive or the inner ring and outer ring are broken, new bearings of the same model should be replaced.
2.5 Motor running vibration, improper coupling installation, too tight transmission belt and bent shaft will all cause bearing heating; the causes should be eliminated according to the situation.
2.6 If the bearing does not fit well with the shaft shoulder, disassemble the bearing cover, use a copper rod to push against the inner ring of the bearing and tap in symmetrically with a hammer.
2.7 If the end cover or bearing cover is poorly assembled, it should be reassembled so that the end covers at both ends fit well with the base seam, and the fastening bolts of the bearing cover are tightened diagonally.
2.8 The working performance of rolling bearings not only depends on the manufacturing accuracy of the bearing itself, but also is related to the dimensional accuracy, geometric tolerance and surface roughness of the shaft and hole it matches, the selected fit and the correct installation.
If the fit between the inner ring of the bearing and the shaft is too tight, or the fit between the outer ring of the bearing and the inner hole of the bearing chamber of the end cover is too tight, that is, when the tolerance is too large, the bearing clearance will become too small after assembly, sometimes even close to zero. In this way, the bearing will not rotate flexibly, and it will generate heat during operation, and even burn the bearing.
However, if the fit between the inner ring of the bearing and the shaft is too loose, or the fit between the outer ring of the bearing and the end cover is too loose, then during operation, the inner ring of the bearing and the shaft, or the outer ring of the bearing and the end cover will move relative to each other, causing friction and heat. Cause the bearing to overheat. The appropriate interference fit between the inner ring of the rolling bearing and the shaft and the fit between the outer ring of the rolling bearing and the end cover generally adopt overfitting. See the manual or instruction manual for their fit tolerances.
2. How to clean rolling
bearings. Before assembly, bearings must be cleaned carefully. The cleaning agent usually uses gasoline or kerosene. The purpose of cleaning is:
1. Wash off the anti-rust agent on the bearings.
2. Wash away the stolen goods and debris that may have entered the bearing accidentally. Bearings with dust caps or sealing rings on both sides have lubricant added before leaving the factory. Do not clean them during installation.
Do not place the cleaned bearing directly on the workbench or in an unclean place. Use a clean cloth or paper to place it under the bearing. Do not handle it directly with your hands. It is best to wear canvas gloves that are not easy to shed hair.
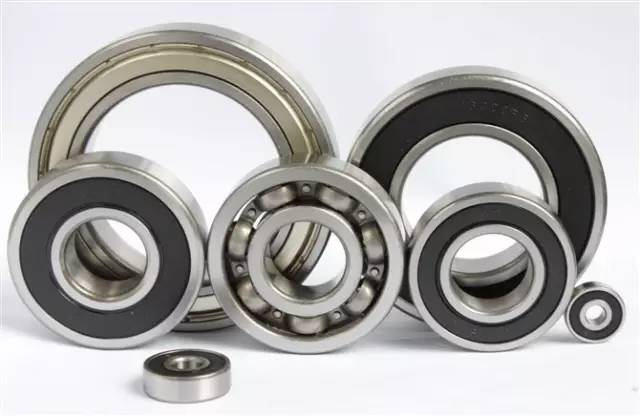
3. How to diagnose whether the rolling bearing is damaged and whether it can continue to be used:
1. For small motors, move the shaft extension of the rotor up and down by hand. If the rotating shaft can move a lot at this time, it means that the bearing is seriously worn.
2. Disassemble the end covers at both ends of the motor for inspection. If oil stains are found on the surface of the windings and core, it means that the bearings are leaking oil, the seals are not tight or are deformed.
3. After the bearing is removed, wipe off the grease in the bearing, and then clean the bearing with gasoline. Then rock the outer ring back and forth relative to the ball by hand. The clearance of a good bearing is almost imperceptible. If the gap between the ball and the inner and outer rings is large, it means that the bearing is seriously worn and needs to be replaced with a new one.
4. Correct assembly
of rolling bearings . There are two key issues in the assembly of rolling bearings. One is the cleaning method of the bearing, and the other is the installation method of the bearing. Experience has proven that the cleaning and installation methods of bearings have a great impact on the noise and vibration produced by the motor. Correct cleaning and installation methods can reduce motor vibration and bearing noise. Incorrect cleaning and installation methods are often the main reasons why the motor produces vibration and noise, the bearing is damaged, or its service life is reduced. Therefore, the cleaning and installation of rolling bearings must be carried out carefully and in accordance with the correct method.
1. Preparation before assembly
1.1 The place where the bearing is assembled must be clean to prevent dust or small particles from entering the bearing.
1.2 Check the shape and position tolerance of the shaft. If it does not meet the requirements, it cannot be assembled. At the same time, check the fillet size at the root of the shaft shoulder and the perpendicularity of the shoulder to the shaft. Generally, the fillet radius at the root of the shaft shoulder should be smaller than the fillet radius of the bearing inner ring so that the bearing can be close to the shaft shoulder.
1.3 The assembly surface of the parts needs to be cleaned with gasoline or kerosene. No rust, spots or solid particles are allowed.
2. Bearing assembly process
There are two methods for assembling bearings and shafts: hot sleeve and cold sleeve. However, thermal sleeves are generally used because the inner ring of the bearing and the journal are generally overfitted and are easy to sleeve after heating.
2.1 Oil heating method
When hot-sleeving, take out the heated bearing from the oil tank, and immediately wipe off the oil stains and attachments attached to the bearing surface with a lint-free white cloth, then pad it with a cloth, keep both hands flat, and align them with the rotating shaft. Push to the shaft shoulder. If it does not go in, it may be too slow, the bearing has cooled, or the bearing ends are not equalized by hand. At this time, a copper sleeve can be used to hold the inner ring of the bearing and gently tap in with a hammer. After the bearing is sleeved, clean the transformer oil in the bearing, and then add the grease with the motor nameplate logo. Generally, it is between 1/3-2/3 of the volume of the bearing chamber, and should not be too much or too little. Too much will cause the bearing to heat up and leak oil, while too little will accelerate the wear of the bearing and make loud noises.
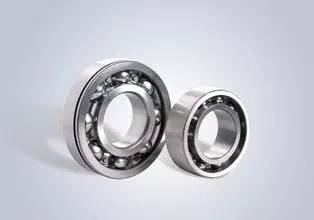
5. Causes and treatment methods of sliding bearing failures 1. The causes and treatment methods of overheating of sliding bearings are as follows: 1.1 Damage to the oil ring causes bearing overheating. Oil rings are often used in sliding bearings to bring oil into the space between the rotating shaft and the bearing bush. If the oil ring is deformed or worn In severe cases, the oil ring will not rotate or rotate slowly, thereby reducing the amount of oil between the shaft and the bearing bush and causing overheating. Open the bearing seat cover, inspect the oil ring and replace it in time. 1.2 Problems with lubricating oil cause bearing overheating.
There are many types of lubricating oil. If you choose improperly, the oil is too dirty, or the amount of oil is not enough, it can cause the bearing to overheat. The oil used for sliding bearings depends on the power and speed of the motor. Please check the relevant technical manual.
1.3 Poor machining of the bearing bush causes bearing overheating.
Poor scraping of the bearing bush causes the bearing bush to become eccentric, causing serious wear of parts of the bearing bush. As a result, the contact angle between the rotating shaft and the bearing bush is too large, and the oil wedge cannot be formed, which destroys the friction of the oil body and causes the bearing bush to heat up; The bearing bush should be re-scraped or replaced with a new one.
1.4 Poor cooling causes bearing heating.
There is oil on the bearing shell, which causes poor heat dissipation, or the bearing is overheated due to the influence of the temperature and volume of the cooling water. The bearing shell should be kept clean and the cooling water pipes should be kept clear and descaled regularly; the cooling water quality and heat dissipation should be ensured well.
1.5 Oil circulation system failure causes bearing heating
. Sliding bearings lubricated by pressure oil circulation often suffer from oil shortage or oil cutoff due to oil pipeline blockage or oil pump failure, causing bearing heating. In addition, the water temperature of the circulating cooling water of the pressure oil is too high, resulting in a high temperature of the pressure oil; it will also cause the bearing to heat up. The oil pipes should be unclogged frequently and promptly, especially in summer, to ensure that the temperature of the circulating cooling water is not high.
2. Scraping and grinding of the bearing bush of the sliding bearing
2.1 The bush lining of the bearing bush generally needs to be scraped. The purpose of scraping the bearing bush is to make the bush lining form a certain geometric shape, so that there is a wedge-shaped gap between the bearing bush and the journal, so as to ensure that when the journal rotates, a wedge-shaped oil film can be formed between the friction surfaces, causing the journal to rise away from the bush lining. It operates under the buoyancy of the oil film to reduce friction with the tile lining and reduce its wear and power consumption.
2.2 The bearing bush is inspected using the coloring method. When inspecting with the coloring method, clean the bearing bush first and check that the bearing bush should be free of cracks, blisters, shelling, etc. Then apply a thin layer of red lead evenly on the journal. Do not apply it too thickly, as it will affect the inspection effect. After the journal is coated with red paint, install the bearing bush and rotate it twice; then take out the bearing bush, so that you can see that the protruding part on the bearing bush is colored red. The distribution of dyeing points is required to be within 60°-70° of the center of the bearing, with 2-3 points per square centimeter. It should not be too many or too few; otherwise, it needs to be scraped.
2.3 The bearing bush is scraped using the dry grinding method. Use a triangular scraper to first scrape the large spots into small pieces, scrape the dense spots thinly, and then scrape them once in one direction, twice if necessary. The directions of the knife marks should intersect between each pass to form a network and fish scale shape. After scraping, use a white cloth dipped in alcohol to clean the tile surface and journal. Repeat the above scraping method to make the stained spots on the bearing bush become finer and finer, until they meet the requirements.
2.4 No contact points are allowed outside the 70° angle at the center of the bearing. If there are any, they should be scraped off and the two sides of the bearing should gradually expand into a wedge-shaped gap.
6. Conclusion
Whether the motor bearings can operate normally is directly related to the safe and efficient operation of the motor. Only by strengthening inspections and correctly maintaining motor bearings can the safe operation of the motor be ensured.