Which welding process is more suitable for motor windings?
Anyone who has worked in motor manufacturing, inspection and quality management positions will have the same feeling. Some customers have very high and even demanding quality requirements for motors; while there are also customers who position the quality of motor products as just being usable!
Higher customer requirements are a positive promotion for product quality improvement and process improvement. Compared with most other applications, automotive motors have relatively high performance requirements. Due to the relatively demanding installation space, specific requirements are put forward for motor volume and power density. According to relevant statistical data, the current power density of electric vehicles is about 3.2kW/kg, and the target value is 4kW/kg; pure power density requirements require improvements in the design and manufacturing process of the motor, which is why most automotive motors Important reasons for using flat wire windings.
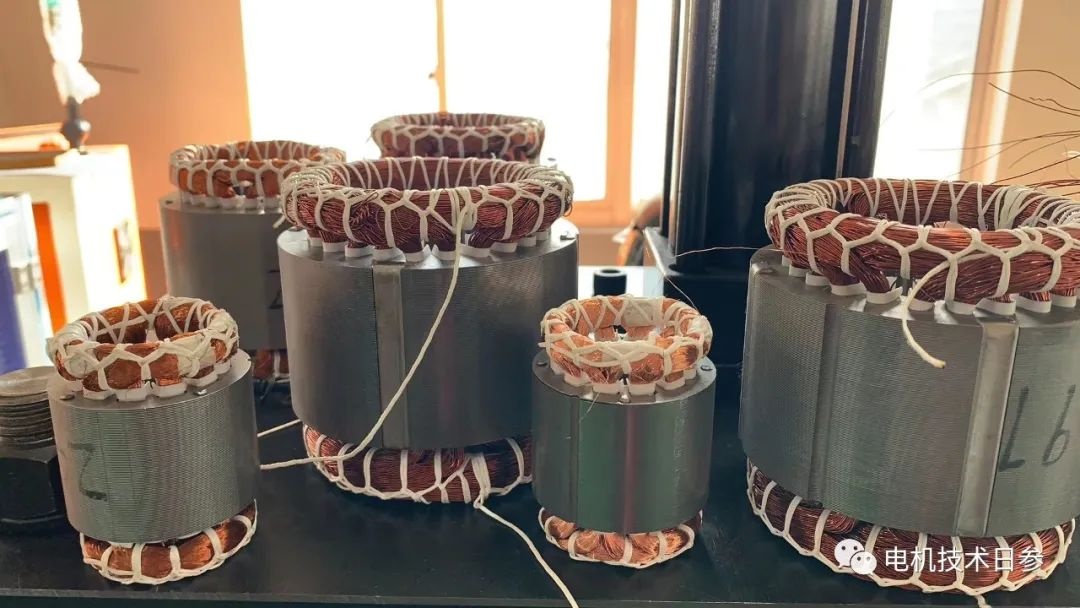
The manufacturing process of flat wire windings is more complicated than that of round wire windings, especially when there are many welding points during the winding processing. During the welding process of electromagnetic wires, the problem of whether to remove the paint from the enameled wires has always been a headache for motor manufacturers. , especially for round wire windings with a relatively large number of turns in parallel, and flat wire windings with many welding points, quality, efficiency and environmental protection are always contradictions in the motor winding manufacturing process; in order to solve this problem, it is necessary to directly Welding equipment has been put on the market, and the laser paint removal process with smaller impact area has emerged. The medium frequency welding technology with high welding efficiency and good quality has been well applied in many motor manufacturers.
In the performance test of electromagnetic wires, chemical methods are mostly used to remove the paint, which can better ensure that the size of the conductor does not change. However, the operability of this method in the motor production and processing process is poor. Laser paint removal utilizes the interaction process between laser and matter to achieve efficient removal of paint. In the process of laser paint removal, the laser beam irradiates the surface of the paint and converts light energy into heat energy, which reduces the adhesion between the paint and the substrate, thereby achieving the purpose of removing the paint. Laser paint removal will not damage the original performance and characteristics of the material, and can accurately control the removal depth and location.